
SM53C 탄소강 자동차 부품 곡면부의 고주파 열처리 미세조직 및 경도 변화
Abstract
High-frequency induction hardening is one of the most commonly used heat treatment techniques for steel and by which enhanced surface hardness can be achieved for fatigue and wear resistance. During this process, a certain depth of products is rapidly heated and quenched so that the microstructure of the hardened surface is finer than those of the other parts of the product. In general, the hardening depth is more uniform in the straight surface than in the irregular-or complex-shaped surfaces because of the non-uniform heating and cooling rates in the irregular surfaces applied from the induction coils. This non-uniform hardening depth can cause unexpected deterioration of the fatigue properties. In this study, high-frequency induction hardening was applied to an SM53C steel automotive part having a 90° curved shape, and the microstructure and hardness variation in the curvature area were characterized in detail.
Keywords:
High frequency induction, Heat treatment, Carbon steel, Microstructure, Hardness, Electron backscatter diffraction1. 서 론
자동차, 철도, 항공기, 선박 등의 운송 산업에 사용되는 구조용 부품들은 사용 목적에 따라 다양한 기계적 물성이 요구되고 있으며, 최근 고속화 및 고성능화에 따라 강도뿐만 아니라 내구성과 수명 향상에 대한 요구가 급격하게 증가하고 있다. 이를 위해 신규 소재 개발과 더불어, 기존 소재에 대해서도 가혹한 환경에서 충분한 피로수명과 내구성을 갖도록 열처리 등 후처리 기술의 개발이 매우 중요하다. 특히, 자동차 구동 부품 중 등속조인트, 밸브가이드 등의 부품에서는 구동 특성상 고속회전에 의한 피로와 편마모 현상이 많이 발생하며, 슬립 현상도 수반되어 피로수명의 저하로 이어지게 된다[1]. 이는 부품의 수명을 단축시키고, 차량 전체의 내구성을 떨어뜨리며, 등속조인트 부품의 파단 경우에는 극단적으로 자동차 바퀴가갑자기 탈거되는 매우 위험한 결과를 초래할 수도 있다.
따라서 등속조인트, 밸브가이드 등의 부품은 내피로 물성과 내마모성 향상을 위해 사용 환경에 적합한 후처리 공정을 적용하는 것이 필수적이다. 강종의 표면경화 후처리 공법으로는 침탄, 질화 등 확산을 이용한 열처리 방법과 고주파 유도가열을 통한 열처리 방법이 대표적이다[2]. 이 중에서 고주파 열처리 방법은 대상 금속소재의 표면층만 급속하게 가열 및 냉각시키기 때문에 일반 열처리로 얻어지는 미세구조에 비해 조직이 훨씬 미세하다. 또한 표면에 압축 잔류응력을 발생시켜 피로물성을 향상 시킨다[3-6]. 이때 부품소재가 불필요하게 취화되는 것을 방지하기 위해 고주파 열처리 조건을 조절하여 표면경화 깊이를 제어한다. 고주파 열처리 대상 부품의 형상에 있어서, 환봉과 같은 단순한 형상에 대한 고주파 열처리 연구는 비교적 많이 이루어졌다. 이는 고주파 가열 코일과소재의 간격이 일정하여 온도 분포가 균일하기 때문이며, 대부분 주파수 및 유지시간에 따라 경화 깊이가 직선적으로 증가된다[7].
그러나 형상이 복잡하거나 곡면을 포함하는 부품의 경우 순간 가열 및 냉각조건이 부위별로 일정하지 않아 경화 깊이의 제어가 쉽지 않으며, 균일한 강화상 조직을 얻기 어렵기 때문에 표면경화 효과 면에서 취약한 부위가 발생할 여지가 많다. 그럼에도 불구하고, 이와 관련된 연구는 쉽게 찾아보기 어렵다. 본 연구의 목표는 자동차용 등속조인트, 밸브가이드 등과 같이 곡면부를 포함하는 부품의 고주파 열처리 특성을 확인하는 것으로서, 유지시간에 따른 직선부 및 곡면부의 경화 깊이의 변화, 미세조직의 변화 및 표면 경도의 변화를 관찰하여 관련 연구 자료를 구축하는데 그 목적이 있다.
2. 실험방법
2.1 소재
본 연구에서는 자동차 구동 부품 제조에 많이 사용되는 SM53C 중탄소강을 이용하였고, 그 조성은 Table 1과 같다. SM53C 강은 평균적으로 0.53 wt.%의 탄소를 포함하고 있고, 조성이 비교적 단순하여 가격이 저렴하며, 가공성과 내마모성을 동시에 보유하고 있어서 부품 제조 산업 전반에 걸쳐 널리 사용되는 소재이다. 일반적으로 페라이트와 펄라이트 조직으로 구성되어 있으며, 열처리 후 냉각 조건에 따라 잔류 오스테나이트, 베이나이트, 마르텐사이트 등의 조직이 형성되어 강도 및 경도를 향상 시킬 수 있는 재료이다.
2.2 고주파 열처리
본 연구에 사용된 자동차 부품의 형태는 Fig. 1과 같으며, 고주파 열처리를 통해 경화처리가 필요한 부분은 직선 부위와 곡면 부위를 모두 포함하고 있다. 직선 열처리 부위는 톱니바퀴 형상의 치형부를 포함하고 있으며, 곡면 열처리 부위의 곡률반경은 R5이다. 고주파 열처리는 재료의 고유저항 및 주파수(Hz), 사용전력(kW), 사용전압(V), 발열체 코일 이송속도와 유지시간, 온도 등이 변수로 작용한다. 본 실험에서는 고주파 열처리 시 공석 상변태 온도(725°C) 이상에서 탄소강의 초기 조직들이 오스테나이트로 상변태가 될 수 있는 충분한 온도(880°C)가 되도록 사용전압 및 주파수에 따른 온도 변화를 적외선 온도 센서로 측정하였으며, 결과를 바탕으로 열처리 조건을 설정하였다. 이는 해당 자동차 부품의 실제 생산 현장에서 SM53C 소재의 고주파 열처리 시 일반적으로 사용되고 있는 조건이다. 유일한 열처리 변수 조건인 가열 유지시간은 일반적으로 사용 소재에 따라 10초 전후의 시간으로 선택하는데, 본 연구에서는 5초와 10초로 차이를 두어 고주파 열처리 실행하였으며, 고주파 열처리 이후 냉각수를 10~12초 동안 분사하여 상온까지 냉각시켰다.
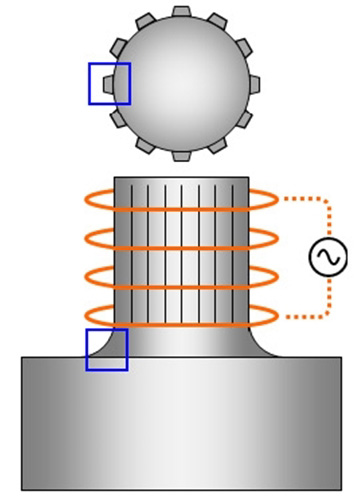
Schematic of high frequency induction heat treatment of SM53C steel automotive component showing both stem and curve parts with blue squares for hardness measurements and microstructure analysis
2.3 미세조직 분석 및 경도 측정
고주파 열처리 시 가열 유지시간에 따른 경화 깊이 차이와 미세조직 변화를 관찰하기 위하여 미소경도 측정과 광학현미경 및 전자현미경 분석을 실시하였다. 경도 측정은 Matsuzawa AMT-X7FS micro-Vickers 경도기를 이용하여 300 gf 하중으로 10초 동안 압입하여 측정하였다. 경도 측정을 수행한 영역을 격자 형태를 형성하며 가로, 세로 일정 간격으로 측정한 후 경도 값을 2차원 color-coded contour map으로 나타내었다. 직선 열처리 부위에서는 6 mm × 6 mm 횡단면 영역에서 가로, 세로 300 μm 간격으로 경도를 측정하였고, 곡면 열처리 부위에서는 10 mm × 10 mm 종단면 영역에서 가로, 세로 500 μm 간격으로 경도를 측정하였다.
미세조직 분석을 위한 시편은 cutting, mounting, grinding의 과정을 거쳐 0.04 μm colloidal silica를 이용하여 최종 polishing하였다. 광학현미경 분석은 연마된 시편을 5% Nital 용액으로 etching한 후 실시하였고, 전자현미경 분석은 Hitachi SU-70 FE-SEM과 EDAX Hikari XP EBSD 장비를 이용하여 시행하였다. EBSD 분석은 20 kV에서 0.5 μm step size 조건으로 진행하였고, 분석 결과는 TSL OIM 7.1 software를 이용하여 standard clean-up 방식으로 노이즈 제거 후 inverse pole figure(IPF) map으로 나타내었다.
3. 실험결과 및 고찰
Fig. 2는 치형부를 포함하는 직선 부위 단면에서의 고주파 열처리 가열 유지시간에 따른 경화 깊이 차이 및 경도 분포를 보여준다. 고주파 열처리 시 요구되는 경화 기준은 일반적으로 약 520 Hv이다. 이러한 기준을 적용하여 가열 유지시간 5초와 10초 시편의 520 Hv 이상 경화 깊이를 비교하였을 때, Fig. 2(a)의 5초 시편이 약 4.8 mm, Fig. 2(b)의 10초 시편이 약 5.0 mm로서 표준 경화 깊이에는 큰 차이가 없었다. 또한 탄소강의 마르텐사이트 경도인 770 Hv 이상의 경도를 기준[8]으로 경화 부위를 비교하였을 때는, 유지시간 5초 시편이 약 3 mm 깊이까지 770 Hv 이상의 경도로 경화된 반면, 10초 시편의 경우는 표면으로부터 약 3.5 mm 깊이까지 770 Hv를 상회하였다.
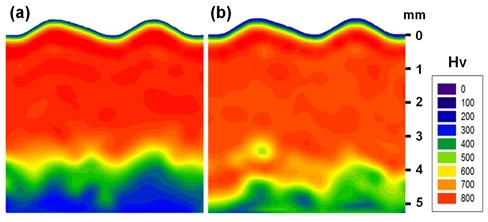
Hardness distribution at cross-section of stem part after induction heating with holding times of: (a) 5 sec and (b) 10 sec
Fig. 3은 곡면 부위 단면에서의 가열 유지시간에 따른 경화 깊이 및 경도 분포를 나타낸다. 이 경우에는 고주파 열처리 경화의 일반 기준인 520 Hv 이상으로 경화된 깊이를 비교하였을 때, 가열 유지시간에 따라서 경도 분포의 차이가 컸다. Fig. 3(a)의 5초 시편이 약 2.2 mm, Fig. 3(b)의 10초 시편이 약 4 mm 깊이였다. 마찬가지로, 곡면 부위에서 경도 770 Hv 이상의 경화 부위를 비교하였을 때는, 두 유지시간 시편 모두 약 0.5 mm 깊이까지만 경화되었다. Fig. 2와 Fig. 3의 경도 측정 결과를 Table 1에 정리하였다. 고주파 열처리 시 유지 시간이 길수록 혹은 스캔 속도가 짧을수록 스킨 효과(skin effect)로 인한 열 영향부가 증가한다[7]. 본 연구에서도 10초 동안 고주파 열처리 시, 열 영향부의 증가로 인하여 마르텐사이트로의 상변태 영역과 경화 깊이 모두 증가한 것으로 판단된다.
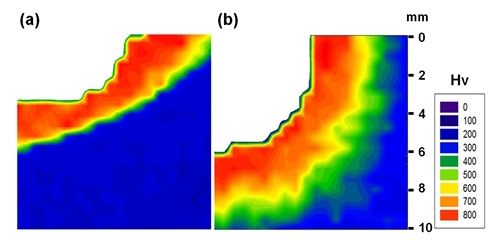
Hardness distribution at cross-section of curve part after induction heating with holding times of: (a) 5 sec and (b) 10 sec
가열 유지시간이 5초였을 때와 10초였을 때 모두 직선 부위보다는 곡면 부위에서의 경화 깊이가 얕았다. 특히 유지시간이 짧았던 5초 시편에서 직선 및 곡면 부위 위치에 따른 경화 깊이의 차이가 컸다. 직선 부위를 고주파 열처리 하였을 때는 소재 표면과 발열체 사이의 간격이 일정하여 전체적으로 고른 경화 깊이를 나타낸 반면, 곡면 부위의 경우 직선 부위에 비해 발열체와의 거리가 일정하지 않고, 곡면을 지나는 발열체가 경화시켜야 할 소재의 체적이 직선부의 그것보다 넓기 때문에 상대적으로 얕은 경화 깊이를 나타낸 것으로 사료된다. 그 중에서도 고주파 열처리에 따른 경화 깊이의 기준이 되는 열처리 경계부인 520 Hv 경도를 고려했을 때에는, 5초 유지시간으로 열처리하였을 때 곡면 부위의 경화 깊이가 2.2 mm로서 급격하게 떨어지는 것을 확인할 수 있었다. 또한 경도 400~600 Hv 구간의 경화 부위가 거의 존재하지 않고 열처리 경계부를 기준으로 급격한 경도의 변화를 관찰할 수 있었다. 실제 해당 부품이 겪게 될 다양한 하중 조건에서 곡면 부위에 응력이 집중될 것을 감안한다면, 곡면 부위에서의 매우 얕은 경화 깊이는 부품의 피로물성을 크게 악화시킬 가능성이 있다.
고주파 열처리 가열 유지시간에 따른 곡면 부위의 미세조직 변화를 관찰하기 위해 광학현미경 및 EBSD 분석을 실시하였다. Fig. 4는 곡면 부위에서 표면으로부터 3 mm 깊이까지 영역을 광학현미경으로 분석한 미세조직 사진이며, Fig. 3에서의 경도 측정 위치와 동일하다. 경도 분포 mapping image에서 알 수 있다시피, 곡면 부위에서 가열 유지시간이 5초일 때에는 경화부와 비경화부 사이의 경도 변화가 급격하고, 10초였을 때에는 경도 변화가 상대적으로 완만함을 알 수 있다.
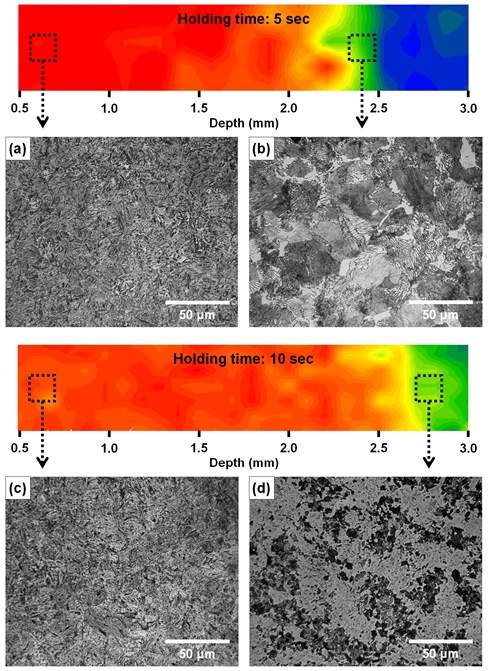
Optical micrographs of curve part after induction heat treatment with holding times of: (a, b) 5 sec and (c, d) 10 sec
이러한 차이를 Fig. 4의 광학현미경 사진으로 비교하여보면, 두 가열 유지시간 시편 모두 경화부에서는 미세한 결정의 마르텐사이트 상이 형성되었음을 알 수 있다(Fig. 4(a), 4(c)). 그러나 비경화부에서는 고주파 열처리 가열 유지시간에 따라 미세조직이 상이함을 알 수 있다(Fig. 4(b), 4(d)). 유지시간 5초 시편의 비경화부(Fig. 4(b))에서는 일반적인 SM53C 탄소강이 나타내는 펄라이트 + 페라이트 미세조직을 볼 수 있으나, 유지시간 10초 시편의 비경화부(Fig. 4(d))에서는 마르텐사이트 경화 조직과 펄라이트 + 페라이트 비경화 조직이 공존함을 확인할 수 있었다.
따라서 곡면 부위에서 고주파 열처리 가열 유지시간 5초 시편의 경우, 경도 770 Hv 이상의 마르텐사이트 경화 미세조직과 경도 500 Hv 이하의 비경화 미세조직이 열처리 경계부(약 2.2 mm 깊이)를 기준으로 중간 미세조직 없이 급격하게 변하고 있음을 알 수 있다. 반면에, 유지시간 10초 시편의 곡면 부위에서는 명확한 열처리 경계부 없이 경화부와 비경화부 사이 영역에서 두 미세조직이 공존하고 있음을 알 수 있었다.
일반적으로 고주파 열처리 발열체와 가까울수록 미세 마르텐사이트 상이 형성되어 기계적 물성이 크게 증가하게 된다[9]. 그러나 앞서 언급한 바와 같이 곡면 부위에서는 직선 부위에 비해 발열체와의 거리가 멀고 일정하지 않으며, 곡면 부위를 지나는 발열체가 가열해야 할 소재의 체적이 직선 부위보다 크다. 이러한 차이가 가열 유지시간이 5초일 때와 10초일 때 미세조직의 차이를 유발했다고 볼 수 있다. 유지시간 5초 시편의 곡면 부위에서 볼 수 있는 (i) 얕은 경화 깊이, (ii) 경화 조직과 비경화 조직의 급격한 변화, 이로 인한 (iii) 경도의 급격한 변화로 인해 일반적인 고주파 열처리 시편에서 기대되었던 것보다 상대적으로 낮은 피로주기에서 예상치 못했던 파단이 곡면 부위에서 발생하였다(피로시험 결과는 본 논문에 포함되지 않음).
Fig. 5는 Fig. 4에서 분석한 것과 동일한 곡면 부위에 대해서 EBSD 분석을 진행한 결과이다. Fig. 5(a)~5(d)는 각각 Fig. 4(a)~4(d)의 위치에 해당한다. 표면으로부터 매우 가까운 깊이인 Fig. 5(a)와 5(c)에서 모두 sub-micron 이하의 미세한 결정의 침상 마르텐사이트 상이 관찰되었다. 두 경우 모두 결정 방위는 완전한 임의 방위(randomly oriented)가 아닌 (112)면으로의 약한 집합조직을 나타내고 있다. 표면과 가까운 위치에서는 유지시간 5초와 10초 시편 모두 발열체를 통해 상승된 온도가 동일하고, 미세 마르텐사이트 상으로의 변태가 일어나기 충분한 열이 공급되었다고 할 수 있다.
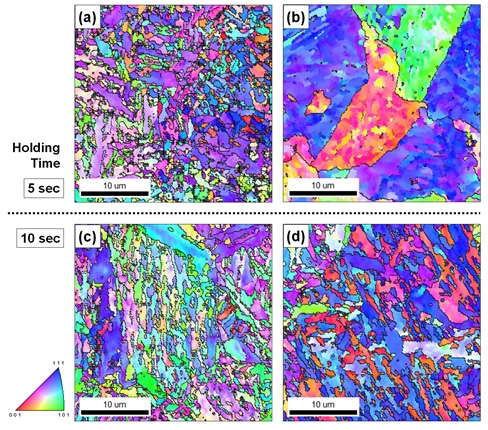
EBSD inverse pole figure map of curve part after induction heat treatment with holding times of: (a, b) 5 sec and (c, d) 10 sec
반면에 곡면 부위에서 표면으로부터 약 2.5 mm 전후의 깊이에서는 유지시간 5초 시편과 10초 시편의 결정립 크기와 형태가 달랐다. Fig. 5(b)의 유지시간 5초 시편 내부에서는 미세 침상 마르텐사이트 강화상을 전혀 찾아볼 수 없었고 원소재 SM53C 탄소강의 열처리 이전 미세조직인 수십 μm 크기 결정의 펄라이트와 페라이트 혼합 상이 관찰되었다. 결정 방위는 강화상에서 발견된 집합조직이 없는 완전한 무작위 방위였다. 그러나 Fig. 5(d)의 유지시간 10초 시편에서는 5초 시편에서 관찰된 비열처리 미세조직 내부에 부분적으로 미세 마르텐사이트가 형성되고 있음을 알 수 있다.
Fig. 4와 Fig. 5의 곡면 부위 미세조직 분석으로부터 알 수 있었던 것을 정리하면 다음과 같다. (i) 발열체와 가까운 표면에서는 (분석 깊이 약 0.5 mm) 고주파 열처리 가열 유지시간이 5초 일 때와 10초 일 때 모두 sub-micron 크기 이하의 미세 침상 마르텐사이트 강화상이 형성되었다. (ii) 약 2.5 mm 깊이에서는 가열 유지시간이 5초였을 때에는 마르텐사이트 강화상이 전혀 형성되지 않았다. 반면에 가열 유지시간이 10초였을 때에는 미세 마르텐사이트 강화상이 부분적으로 형성되었다. (iii) 결정립의 방위는 비열처리 부위에서는 완전한 무작위 방위가 관찰되었고, 열처리부 강화상에서는 (112) 면으로의 약한 집합조직이 발견되었다.
고주파 열처리에서는 냉각온도와 주파수, 그리고 열처리 시간에 의해 경화 깊이가 달라진다. 냉각 조건 및 고주파 열처리 주파수에 따른 경화 깊이(dc) 일반식은 다음과 같으며, T는 냉각온도, f는 주파수를 나타낸다[7].
(1) |
또한 고주파 가열 시 열전도에 의해 열처리 시간이 증가할수록 경화 깊이가 깊어진다. 고주파 열처리 시간에 따른 경화 깊이(ds) 일반식은 다음과 같으며, t는 열처리 시간을 의미한다[7].
(2) |
전체적인 경화 깊이는 위의 두 식을 합한 dc + ds로 표시할 수 있으며, 이를 본 연구의 직선 부위 경화 깊이와 비교하였을 때 위의 식과 동일한 결과를 보이는 것을 확인할 수 있었다. 그러나 본 연구의 곡면 부위 경화 깊이 분석에 적용하였을 때에는, 위 식으로부터 계산된 깊이와 실제 측정한 경화 깊이에 차이가 발생했다. 실제 측정값을 바탕으로 위의 식들을 곡면 부위에 맞게 새롭게 보정한 결과는 다음과 같다.
(3) |
따라서 고주파 열처리 시 냉각온도와 주파수에 의존하는 경화 깊이와 가열 유지시간에 의존하는 경화 깊이가 모두 곡면 부위에서 직선 부위에 비해 큰 폭으로 감소함을 수치로 확인할 수 있다.
본 연구를 포함하여 일반적인 고주파 열처리에서 주파수와 냉각온도는 급가열과 급냉 과정을 최적화하기 위해 원소재의 탄소 조성을 고려하여 고정된 값을 사용한다. 따라서 고주파 열처리 시 발열체의 끝부분에 곡면 부위가 존재할 경우, 가열 유지시간의 작은 변화가 곡면 부위 경화 깊이의 큰 차이를 유발할 수 있음을 본 연구를 통해 확인하였다. 이를 통해 곡면 부위에서 예상치 못한 피로파단이 일어나지 않도록 곡면의 형태와 곡률반경에 따라서 고주파 열처리 가열 유지시간의 최적화가 이루어져야 할 것이다.
4. 결 론
곡면 부위를 포함하는 SM53C 중탄소강의 고주파 열처리 시 가열 유지시간 변화에 따른 미세조직 및 경도의 변화를 확인하였다. 발열체와의 거리가 일정한 직선 부위에서는 가열 유지시간에 따라 경화 깊이의 차이가 거의 발생하지 않았다. 그러나 발열체가 끝나는 부분의 곡면 부위에서는 가열 유지시간에 따른 경화 깊이에 큰 차이가 발견되었다. 본 연구에서 사용된 소재의 고주파 열처리 시 사용되는 일반적인 가열 유지시간 5초의 경우에는 경화 깊이가 매우 얕고 경도 변화가 급격했다. 반면에 가열 유지시간을 10초로 늘렸을 경우에는 직선 부위와 크게 차이가 없는 경화 깊이를 보였다. 이는 곡면 부위에서 발열체의 끝부분이 경화시켜야 할 소재 부분이 부채꼴의 형태로 직선 부위보다 그 체적이 훨씬 크기 때문에 가열 유지시간이 충분하지 않을 때에는 충분한 깊이까지 경화가 이루어지지 않았기 때문인 것으로 사료된다. 따라서 곡면 부위가 존재하는 부품의 고주파 열처리를 수행할 때에는 대상 부품의 형상과 곡률 반경 등을 고려하여 발열체 코일을 설계하고 최적의 가열 유지시간을 확보해야만 필요 경화 깊이를 얻을 수 있을 것이다.
Acknowledgments
본 연구는 2015학년도 아주대학교 일반연구비 지원에 의하여 수행되었습니다.
References
- Lee, H. J., Park, S. H., Park, W. J., (2009), Characteristics of Fatigue Crack Growth for Camshaft Material Applied to High Frequence Induction Treatment, J. Ocean Eng. Technol., 23(3), p46-52.
- Park, J. D., Kim, S. W., (2003), Current Status and Prospects of Induction Hardening Technology, Journal of the Korean Society for Heat Treatment, 16(4), p224-231.
-
Tokaji, K., Ogawa, T., (1995), Fatigue Life Distribution and Its Simulation in Spheroidal Graphite Cast Irons, J. Soc. Mater. Sci., 44(497), p187-193.
[https://doi.org/10.2472/jsms.44.187]
-
Kristoffersen, H., Vomacka, P., (2001), Influence of Process Parameters for Induction Hardening on Residual Stresses, Mater. Des., 22(8), p637-644.
[https://doi.org/10.1016/s0261-3069(01)00033-4]
-
Totik, Y., Sadeler, R., Altun, H., Gavagali, M., (2003), The Effects of Induction Hardening on Wear Properties of AISI 4140 Steel in Dry Sliding Conditions, Mater. Des., 24(1), p25-30.
[https://doi.org/10.1016/s0261-3069(02)00099-7]
- Koga, H., Kawasaki, K., Wamazaki, T., (2004), Recent Trends on Induction Heat Treatment, Journal of the Korean Society for Heat Treatment, 17(2), p106-116.
- Suzuki, D., Yatsushiro, K., Shimizu, S., Sugita, Y., Saito, M., Kubota, K., (2009), Development of Induction Surface Hardening Process for Small Diameter Carbon Steel Specimens, JCPDS-ICDD, p569-576.
- Lauralice, C. F. C., Xin, Y., Jiangeng, G., George, E. T., (2008), A Historical Overview of Steel Tempering Parameters, Int. J. Microstructure and Materials Properties, 3(4-5), p474-525.
- Lee, J. H., Jeong, W. C., (2010), A Study on Mechanical Properties and Microstructure of Local-Hardening Heat-Treated Automotive Panel, Journal of the Korean Society for Heat Treatment, 23(6), p301-308.