
차량 범퍼 하부에 대한 사출성형 변형해석
Abstract
The lower stiffener for an automobile bumper has a problem in that deformation occurs during injection molding. This degrades the impact absorption properties of the stiffener. Therefore, research on reducing the deformation during the molding process is required. In this study, the filling time, maximum pressure, maximum mold clamping force, and solidification time of the injection molding process were analyzed as the basis for the research. To analyze the cause of deformation and to improve the quality of the parts, a series of design changes and analyses were performed. As a result, an excellent design was derived that reduces deformation compared to the preliminary design.
Keywords:
Lower stiffener, Polypropylene, Injection molding analysis, Shrinkage deformation1. 서 론
최근 교통사고로 인한 피해자는 줄어들고 있으나, 보행자에 대한 상해율은 아직도 높은 비율을 차지하고 있다. 따라서 차량의 안전법규 강화 및 충돌안전성 평가 기준 강화로 인하여 보행자 충돌 안전기술에 대한 관심이 증가하고 있다. 보행자 충돌 안전기술이란, 충돌 직전 보행자를 사전에 감지하여 사고를 미연에 방지하는 사고 회피 기술과 충돌 과정에서 보행자의 충격을 감소하고 상해로부터 신체적 안전을 확보하는 기술이 대표적이다. 후자의 경우 보행자의 신체 부위별 상해 발생빈도가 머리와 다리에 집중되기 때문에 각각이 충돌하는 후드와 범퍼에서 상해를 저감하기 위한 충격흡수 구조 및 소재에 대한 다양한 연구가 진행되고 있다[1].
특히, 보행자 다리를 효과적으로 보호하기 위해서는 차량 범퍼 시스템의 디자인을 개선하고, 새로운 부품을 범퍼 하단에 추가하는 것이 필요하다[2,3]. 차량용 로워 스티프너(lower stiffener)는 Fig. 1과 같이 범퍼 내부 부품 중에서 가장 앞쪽에 위치하여 보행자 다리의 충돌 하중을 감소시킴과 동시에 보행자 다리의 꺾임각을 줄여 상해를 최소화하는 부품이다. 메쉬(Mesh)형상의 복잡한 구조로 되어 있어 하중에 따른 변형을 유도하여 충격을 흡수하는 역할을 한다.
로워 스티프너는 충격흡수의 목적에 부합하도록 변형이 많이 일어나는 특성이 있다. 따라서 단단한 수지를 사출성형으로 생산하면 잔류 응력이 존재하더라도 가공 변형이 발생하지 않지만, 상대적으로 부드러운 결정성 수지인 폴리프로필렌을 사출성형 공정으로 생산하기 때문에 변형이 현저하게 나타나는 단점이 있다.
또한 사출성형은 수지가 회전하는 스크류와 배럴에 의하여 이송 및 용융되는 가소화 과정, 용융수지가 노즐을 통과하여 금형내의 공동부를 채우는 충진 과정, 압력제어를 통하여 금형 내 수지의 수축량을 보상해주는 보압 과정, 금형에 충전된 수지를 열변형 온도 이하로 냉각 및 고화시키는 냉각 과정, 제품을 금형으로부터 취출하기 위한 형개폐 과정으로 이루어진다[4]. 일련의 성형과정은 압력과 온도의 변화를 동반하기 때문에 결정성 수지인 폴리프로필렌의 변형을 증가시킨다.
현재 생산되는 로워 스티프너는 변형을 해결하기 위해 수차례의 금형수정을 하고 수정으로 미흡한 제품은 변형된 제품을 강제로 피는 지그를 제작하여 변형을 개선하고 있으나, 이러한 과정에서 시간과 금전적인 손해를 지속적으로 발생시키고 있다.
따라서 본 연구는 자동차 범퍼 내부의 로워 스티프너로 사용되는 결정성 고분자 수지인 폴리프로필렌 사출품의 변형을 줄이기 위한 성형 해석을 수행하였다. 변형의 원인을 분석하고 개선함으로써 변형 방지 지그 제작비용을 절감하고, 성형품의 품질을 개선하는 것을 목적으로 하였다.
2. 본 론
2.1 수축과 변형
성형품의 수축은 금형의 전 지역에서 일정하게 발생하고 제품의 형태 변화 없이 단지 크기와 체적만 감소하는 단순 수축과 수축 방향 위치에 따라 수축율이 다른 불균일 수축이 있다. 그리고 결정성 재료는 전이온도 이하로 냉각되었을 때 분자들이 보다 규칙적인 방법으로 재배열되어 결정을 만드는 반면 비결정성 수지의 미세구조는 상변화가 일어나지 않는다. 따라서 결정성 재료는 용융상태와 고체상태(결정상태)사이에 매우 큰 비체적의 차이로 수축이 발생한다[5].
변형은 사출공정의 특성에 기인하며, 수축의 편차에 따른 응력분포에 따라 발생한다. 이때 내부에 형성된 응력을 in-plane stress라 하며, 응력이 발생하는 영역과 발생하지 않는 영역으로 인하여 차이가 발생하게 된다. 즉, 내부 응력의 평형이 깨지면 in-plane stress가 방향성을 가지며 한쪽으로 치우치게 된다. 따라서 응력 분포의 불균형으로 인한 변형이 발생하며, 이를 좌굴(buckling)이라고 한다[5].
2.2 해석방법
해석은 사출성형 플라스틱 제품의 변형을 확인하고, 금형이 가공되기 전에 제품의 변형을 방지할 수 있는 방안을 모색하는 것을 목적으로 한다. 따라서 선형 좌굴해석(linear buckling analysis)을 통하여 성형품의 두께가 얇은 부분에 대한 좌굴 발생 여부를 판단하여 적절한 재료를 선정하고 성형조건을 결정하여 최종 성형품의 품질을 향상시켰다.
본 연구에서는 플라스틱 제품, 부품을 사출성형 공정으로 제조할 때 발생하는 문제점을 예측 및 분석하는 소프트웨어인 3D TIMON을 사용하였다. Table 1은 로워 스티프너 사출공정조건이며, 수지의 제조사 및 등급, 종류와 같은 정보와 부품의 투영면적, 금형의 온도 및 수지의 녹는 온도를 정리하였다. Fig. 2는 로워 스티프너 성형품의 형상으로 폴리프로필렌 수지 주입을 위한 3개의 게이트 위치와 크기를 표기하였다. 선행 해석을 통하여 충진 밸런스, 체적 수축분포, 고화시간과 함께 부품의 축 방향 변형을 확인하고, 게이트위치에 따른 변형 해석을 하여 개선방안을 모색하였다. 마지막으로 선행 해석에서 확인한 축 방향 변형을 감소시키기 위한 설계 변경과 이를 검증하기 위한 해석을 추가적으로 수행하였다.
2.3 선행 해석
Fig. 3은 폴리프로필렌 수지가 하단의 게이트에서 입력되어 금형의 상단까지 채워지는 과정이다. 충격을 흡수하는 로워 스티프너 구조상 벌집구조(honeycomb structure)의 복잡한 유로를 형성하고 있으나 대칭 구조의 게이트로 인하여 완전히 충진 될 때 까지 균일한 밸런스를 유지한다. 또한 충진 완료 상태까지 4.5 s의 시간이 소요되며, 최대 압력 58 MPa과 최대 형체력 695 Ton의 결과를 확인하였다.
Fig. 4는 보압 과정에서 제품이 대기 온도로 냉각되는 시점까지의 밀도 변화 백분율인 체적수축의 해석 결과이다. 충진 과정에서 고온의 수지가 마지막으로 주입되는 게이트에 인접한 제품 선단부에서 체적 수축분포가 크게 나타난다. 이는 결정성 수지가 냉각되며 재결정화 되는 과정에서 온도 차이가 발생하기 때문에 제품의 변형이 발생한다.
Fig. 5는 사출품의 고화시간에 대한 해석 결과이다. 평균 고화시간은 90 s이며, 제품 선단부는 160 s의 고화시간을 가진다. 선단부는 게이트에 인접하기 때문에 완전한 형상을 만드는 마지막 단계까지 고온의 수지가 채워지기 때문에 상대적으로 긴 고화시간이 필요하다. 이 또한 위치별로 수축 냉각의 구배가 존재하기 때문에 제품의 변형을 유발한다.
Fig. 6은 z축 방향 변형으로 로워 스티프너 중심으로부터 끝단으로 갈수록 증가하는 경향을 보이며, 끝단에서 최대 1.8 mm로 변형된다. 단일 축 방향 해석 결과로 본다면 길이에 비해 얇은 두께 비율로 인하여 냉각 수축과정에서 발생하는 변형이다. 즉, 결정성 수지를 가열과 냉각하는 공정에서 영역별로 잔류하는 응력의 편차로 변형이 현저하게 나타난다.
Fig. 7은 x축 방향 변형으로 z축 방향 변형과 동일하게 끝단으로 갈수로 음(-)의 방향으로 증가하는 경향을 보이며, 최대 -7.1 mm로 변형된다. z축 방향 변형보다 큰 변형을 보이는 것은 게이트에 인접한 선단부가 느린 냉각속도로 수축하는 과정에서 먼저 냉각된 부위에 인장력을 부가하기 때문이다.
2.4 게이트위치 해석
로워 스티프너 금형 내부로 수지가 충진되는 게이트의 위치에 따라서 국부적인 변형의 편차가 발생할 수 있다. 따라서 기존 모델의 전면 게이트 위치 Fig. 2와 다르게 Fig. 8와 같이 측면 게이트 위치 (a)와 후면 게이트 위치 (b)에 따른 변형해석을 수행하였다. 해석 조건은 Table 1과 동일하다.
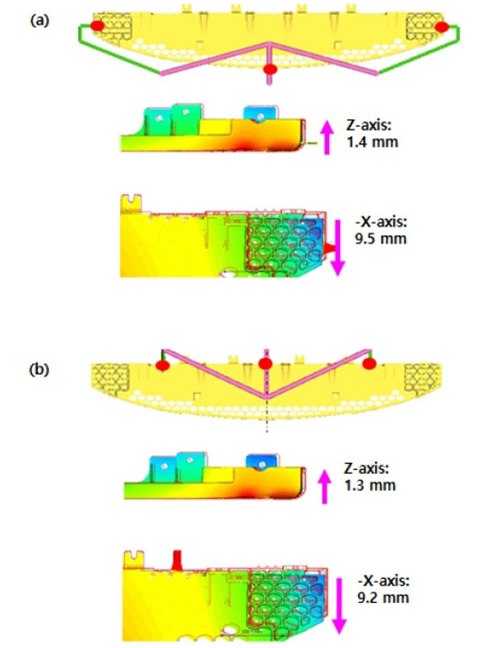
Deformation in injection molding process according to gate locations, (a) side and (b) back (Red dots are gate locations)
측면 게이트위치에서 z축은 기존보다 24% 감소한 1.4 mm의 변형, x축은 33% 증가한 9.5 mm의 변형을 확인하였다. 상대적으로 편차를 줄일 수 있을 만큼 넓은 영역에 분포한 게이트 위치가 두께 방향인 z축에 대한 좌굴 변형을 감소시킬 수 있지만, 측면 게이트에 인접한 끝단부의 변형은 증가한 것으로 확인된다.
후면 게이트 위치에서 z축은 기존보다 29% 감소한 1.3 mm의 변형, x축은 29% 증가한 9.2 mm의 변형을 확인하였다. 벌집 형상을 포함하지 않은 강성이 높은 영역에 집중적으로 게이트가 위치하기 때문에 z축 방향은 수축 변형이 감소하였으나, 끝단부의 변형은 증가하였다.
게이트 위치를 변경하면 z축 변형을 감소시킬 수 있지만, 동등한 비율로 x축 변형이 증가하였다. 해석 결과 변형을 감소시키는 이점이 없다고 판단하여 기존의 게이트 위치를 그대로 사용하기로 하였다.
2.5 설계변경 해석
선행 해석결과 제품이 두꺼운 부분에서 고화시간이 길어지고, 이로 인하여 전체적인 응력분포의 불균형에 기인한 변형이 발생하였다. 따라서 2차 해석에서는 Fig. 9와 같이 기존의 부품 형상에서 두꺼운 부분의 살빼기를 하여 해석을 수행하였다. 해석 조건은 Table 1과 동일하다.
Fig. 10은 개선된 설계안에 대한 변형이다. 변경 이전보다 부품의 수축분포가 균일하게 나타나는 것을 해석적으로 확인하였다. 이에 따라 기존 보다 33%감소한 -1.2 mm의 z축 변형이 발생하였으며, 응력 분포 양상의 변화에 따라 변형이 음(-)의 방향으로 바뀌었다. x축은 기존 보다 87% 감소한 0.95 mm의 변형이 발생했다. 게이트의 선단부에 살빼기 설계변경을 통하여 기존의 느린 냉각속도로 인하여 발생한 응력편차를 감소시키고, 변형이 감소하게 됨을 확인하였다. 즉, 선단부의 두께를 줄임으로써 냉각속도가 빨라져 편차를 줄이고 변형이 감소하였다.
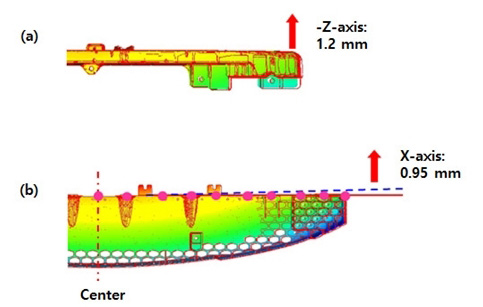
Deformation of injection molding product after first design change for deformation reduction, (a) z-axis and (b) x-axis
그러나 로워 스티프너의 사용목적인 보행자 충돌안전의 관점에서 무분별한 살빼기는 심각한 문제를 초례할 수 있다. 따라서 설계변경으로 약화된 강성을 보강하는 설계변경을 Fig. 11과 같이 수행하였다. 기존의 형상대비 두께를 증가시키고, 벌집구조의 횡 방향 강성을 강화하기 위하여 그리드 립(grid rip)을 추가하였다. Fig. 12는 두 번째 설계 변경에 따른 해석결과이다. 두께를 늘리고, 립을 추가하는 변경은 1차 변경보다 z축의 변형이 208%증가한 -3.7 mm이다. x축, 횡방향의 변형은 83% 감소된 0.16 mm이다. 결과적으로 z축 변형이 증가되었지만, 수정가능 범위 내에 있으므로 기존대비 x축 변형이 감소하고 강성이 증가한 2차 변경 모델로 최종 확정하였다.
3. 결 론
차량용 로워 스티프너(lower stiffener)는 결정성 소재인 폴리프로필렌을 재료로 사출성형 공정으로 생산하기 때문에 열과 압력에 따라 수축과 변형이 발생하는 문제가 있다. 따라서 변형의 원인을 분석하여 기존대비 시간과 금전적인 손실을 절감하고, 성형품의 품질을 개선하는 것을 목적으로 해석을 수행하였다.
(1) 로워 스티프너 부품은 성형공정에서 충진 완료 상태까지 4.5 s의 시간이 소요되며, 최대 압력 58 MPa과 최대 형체력 695 Ton의 결과를 확인하였다. 또한 게이트에 인접한 선단부에서 체적 수축분포가 크며 사출품의 고화시간이 평균 90 s, 선단부에서 160 s 이다.
(2) 게이트위치에 따른 변형을 해석한 결과, 기존 전면 게이트 위치보다 측면과 후면 게이트 위치에서 z축 변형이 각각 24%와 29%로 감소되는 것을 확인하였다. 그러나 각 위치에서 x축 변형이 33%와 29% 증가하여 동등한 증감으로 인하여 위치변화의 변형 저감 효과가 없기 때문에 기존 게이트 위치를 사용하였다.
(3) 부품의 두께에 따른 수축 변형 조절효과가 큰 것을 확인하였다. 기존 형상에서는 z축 변형이 1.8 mm, x축 변형이 7.1 mm이었지만, 1차 살빼기 설계 변경을 통하여 33% 감소한 z축 변형이 -1.2 mm, 87% 감소한 x축 변형이 0.95%로 개선되었다. 그러나 설계 변경과정에서 저하된 강성은 충돌안전의 관점에서 문제가 될 수 있기 때문에 개선안 대비 두께를 증가시키고, 그리드 립을 추가하여 해석을 수행하였다. 결과적으로 208% 증가한 z축 변형이 –3.7 mm, 83% 감소한 x축 변형이 0.16 mm로 기존대비 개선된 로워 스티프너를 설계하였다.
Acknowledgments
이 연구는 2018년도 산업통상자원부 및 산업기술평가관리원(KEIT) 연구비 지원을 받은 연구입니다(No.20000665).
References
- Jung, N. S., Lee, S. Y., Jo, H. A., (2009), Development of the Lower Stiffener Mounted on the Bumper Rail for the Pedestrian Impacts, The Korean Society of Automotive Engineers; Autumn Conference and Exhibition, KSAE09-A0377, p2192-2198.
- Peter, J. S., Bradley, S., (1998), Determination of Bumper Styling and Engineering Parameters to Reduce Pedestrian Leg Injuries, Society of Automotive Engineers, SAE 980361, p93-103.
- Han, Y. H., Park, S. H., Im, H. J., Kim, H. K., Hwang, C. S., (2011), Development of Front Bumper System for Low Speed Impact Performance, The Korean Society of Automotive Engineers; Spring Conference, p1557-1563.
-
Lee, J. H., Lee, S. B., (2016), Determined Car Door Latch Injection Molding Process Conditions through the Finite Element Analysis, Korea Academy Industrial Cooperation Society, 17(10), p499-508.
[https://doi.org/10.5762/kais.2016.17.10.499]
-
Shoemaker, J., (2006), Moldflow Design Guide: a Resource for Plastics Engineers, Hanser Gardner Pubns, Germany.
[https://doi.org/10.3139/9783446418547]
- Kang, I. J., (2013), A Study on the Deformation Improvement in Injection Product by CAE Analysis, A Thesis for a Master, Ajou University, Korea.