
비접촉식 헤드의 박판 파지 특성에 관한 실험 및 수치적 평가해석
Abstract
In this study, a vortex cup and non-contact gripping were considered with commercial specifications for large flat plate application. The stable gripping force range of the cup and non-contact gap that maintains balance between vacuum and thrust were examined numerically and experimentally. In the calculation model, a gripping force of 8 to 14 N and an effective non-contact gap of 0.7 mm were derived according to the flow rate (up to 4,38e-4 kg/s). In actual floating distance measurements using a displacement sensor, the average non-contact gap was 0.6 mm. Further, the flatness could be improved only when using an appropriate flow rate and adjusting the interval between cups. When the gripping force of the cup was greater within the non-contact possibility range than the weight of the sample, then the non-contact gripping of the large plates was considered efficient while ensuring adequate arrangement conditions.
Keywords:
Air head, Gripper, Non-contact, Thin plate, Vortex cup1. 서 론
지금까지 산업 전반에 존재하는 많은 공정에서 다양한 방식으로 적용하고 있는 이송용 또는 작업 파지용 유닛(unit)들은 대부분 접촉식이다. 최근에는 파지방법이나 적용 대상물의 특수성 등의 여러 조건에 따라 사용 방식과 유닛의 구조 또한 다양하게 변화가 이루어져 왔다. 특히 공압(pneumatic power)을 이용하는 방식은 사용의 논리 회로에 따라 간결성과 용이성으로 자동화에 매우 적합하며 응용 면에서도 광범위하다. 소형 제품의 이송 또는 작업용으로는 적은 공기 소모량만 뿐만 아니라 제한 된 공간에서도 그 쓰임새가 충분한 가치를 가지고 있다.
그러나 반도체 웨이퍼, 디스플레이와 같은 정밀을 요하는 작업품 처리 과정에서는 접촉에 의한 표면 손상이나 오염 등을 최대한 방지하고자 다양한 비접촉 유닛들이 개발되고 있다[1,2]. 자기장과 같은 방식의 비접촉 유지는 재료의 물성과 장치의 운용에 제한을 받지만 공압을 이용한 정밀 비접촉 유닛들은 로봇 핸드에 장착되어 쉽게 작업을 처리되고 있다[3]. 현재 소형 제품에 적합한 비접촉 유닛은 주로 베르누이와 보텍스 원리를 이용한 원통 모양의 헤드에 집중되어 있으며 이 기능을 확대하기 위해 운동 에너지를 극대화하면서 안정된 유동 흐름과 이를 바탕으로 이송과 작업 처리에 맞는 변화된 구조를 추구하고 있다[4,5].
베르누이 효과의 압력 차이를 이용한 방식이나 스월 움직임을 극대화하는 방식으로 진공을 얻는 비접촉 헤드 유닛의 연구와 실용 제품은 소형 평판 작업품을 대상으로 이미 많은 결과물들이 존재 하고 있다[6.7]. 상용으로 작업품의 크기(중량) 및 형태에 따라 다양한 모듈들이 출시되어 있으며, 최대 사양으로 본다면 보텍스 방식은 258 l/min 공기 소비율로 최대 100 mm 외경을 적용하여 44 N 파지가 가능하며 베르누이 방식은 최대 외경 150 mm와 291 l/min 공기 소비율로 14 N까지 나타나고 있다[2].
디스플레이 제조 공정에서는 대형 평판의 이송 방식으로 컨베이어를 기본으로 대부분 적용하고 있으며 일부 공정에서 노즐 공 또는 회전 팬을 이용하여 하부에서 압축공기를 토출시키는 공기 부상(air floating)방식을 적용하고 있다[8,9].
표준 원판인 웨이퍼 크기가 현재 300 mm (12 인치)에서 450 mm (18 인치)로 확대되는 추세에서 초소형 비접촉 에어 컵 3개를 사용하여 단일 컵의 회전 등과 같은 움직임을 원천 배제하여 정렬과 같은 정밀성을 높여 사용하고 있다[10]. 이와 같은 맥락에서 작업품의 가공 표면에 대한 공기의 오염원이 제거된다면 상부로 접근하여 파지하는 방식으로 파지 능력이 좋은 보텍스 모양의 컵을 다수 이용하여 파지력을 증가시키고 평판을 수직으로 파지 및 부상이 가능하다.
보텍스 컵은 다른 베르누이 방식에 비해 기본적으로 공기 소모량이 더 많이 요구되고 있으나 그만큼 파지력이 우수하여 여전히 시스템에 포함시켜 활용하는 포괄적인 검토가 많이 이루어지고 있으며 실험적 정보를 바탕으로 설계 및 연구에 대한 기술을 확립하는데 집중해오고 있다[11,12]. 공기 소모량 저감, 대형 평판에의 확장, 박판에의 적용 등이 해결되면 정밀 제조 산업 분야에서 자동 이송시스템에 간단한 구조로 셈플 표면에 저진공으로 비접촉 적용 가능한 흡착력을 만들 수 있기 때문에 반도체 웨이퍼, 유기발광다이오드(OLED), 태양전지판, 의약품, 식품 등의 공정으로 확대 가능하다[13].
보텍스 컵은 움직이는 부품이 없는 수동형 팽창 장치이며 고압 유체 흐름에 의해 활성화되어 에너지를 전달하고, 부분 운동량을 통해 흡착을 위한 진공과 배기를 위한 추력(thrust)을 갖는 정교한 균형으로 활용된다. 이 균형을 바탕으로 그대로 얇은 평판위에 적용했을 때 효과를 극대화할 수 있는 요인은 단순하며 변수는 대략 3~4개로 압축 된다. 주로 컵 내부 챔버의 유로를 따라 공기의 흐름을 제어하는 유동부분과 그러한 유동과 관련되어 고체에 미치는 힘의 크기에 따라 결정된다.
따라서 본 연구는 컵 챔버에 의한 진공 생성과 연관되는 에어 컵 성능에 대하여 논의하며 작동 특징, 고체 표면에 영향을 미치는 조건을 검토하고자 모델링 방법과 실험 및 수치계산을 통한 결과로 분석한다. 선행 연구[1,14]를 바탕으로 하는 보텍스 컵을 적용하고 평판을 파지했을 때 공기소모량, 파지 능력 그리고 컵의 배열 그리고 파지 공작물의 기계적 성질 등의 관계를 고려하기 위해 Fig. 1과 같이 2개의 컵과 500 mm × 330 mm의 샘플을 적용하고자 하며 비접촉 거리를 확인하기 위해 실험적 부분과 해석적 부분을 병행한다. 이를 통해 실질적인 비접촉 거리 범위를 제시하게 되며 수치적 해석으로 파지력과의 상관관계를 도출한다.
2. 비접촉 이격 측정 장치 구성 및 측정 방법
2.1 측정 장치 구성
공압식 헤드 하단부가 작업품을 수직방향으로 파지하여 들어 올리는 동안 유지되는 비접촉 간격을 측정하기 위해 레이저 변위 센서를 사용하였다. 전체적인 실험 장치의 구성은 Fig. 2와 같이 구성되며 수평 정반위에 고정된 기본 프레임에 두 개의 에어 컵을 설치하고 그 하단에 레이저 변위센서 헤드부가 위치하고 유효 거리 내에서 에어 컵 헤드가 파지하는 평판 하단부의 목표 지점으로 투사되고 그 반사 신호 크기를 인식한다. 센서 헤드부는 앰프와 컨트롤러와 연결되고DAQ (data acquisition)와 LabView에서 보정을 거쳐 거리를 측정한다.
레이저 변위 센서는 기준 거리(lo) 80 mm에서 측정 범위 ±15 mm를 가지며 그리고 아날로그 출력 ±5 V와 해상도 3 µm2를 유지하였다. 기본적인 전압 출력 대비 거리에 대한 관계를 구하기 위해 레이저 헤드를 하단부에 위치하여 Fig. 3과 같이 lo = 80 mm 높이 기준으로 샘플의 하단 높이를 75 mm에서 90 mm 높이까지 15 mm의 범위를 주고 1 mm 간격으로 출력 신호(voltage output)를 측정했다. 센서의 출력 신호는 NI (national instruments)의DAQ와 LabView를 이용하여 받았으며 그 결과를 토대로 Fig. 4의 일차 관계를 도출하였으며, 거리 이동에 따른 레이저 센스 헤드가 인식하는 전압 출력 기준으로 기울기인 관계식을 얻었다.
2.2 측정 방법
Keyence LK-81 레이저 변위 센서는 스펙 상으로 80±15 mm에서 유효성을 가지므로 Fig. 3과 같이 하단 변위 센서부에서 비접촉 헤드 하단부(샘플 두께 포함)까지 거리(l*)는 그 유효성 안에 있게 했다. 그리고 샘플이 헤드 하단에 접촉하는 거리와 최초 샘플의 비접촉 부상 위치와의 차이인 e는 10 mm 이내로 하였다. 헤드 하단부 끝단에서 샘플 표면과의 비접촉 파지 거리(h)는 비접촉 부상일 때인 l을 측정하여 l*와 l 차이를 구한 다음 관계식인 2.9928 mm/V을 적용하여 식(1)과 같이 구하였다.
(1) |
여기서 h는 비접촉 환산 거리(mm)이며 l은 레이저 출구에서 부상중인 샘플 하단부까지 측정된 거리에 준하는 출력 전압(mV)이다.
실제 적용에 있어서 Fig. 1과 같이 2b (여기서 b = 10, 12.5, 15 mm)거리를 유지하고 있는 두 개의 에어 컵으로 L = 500 mm 크기인 얇은 판재(t = 2 mm)를 비접촉으로 파지했을 때 두 개의 센서를 대칭적으로 수평방향으로 이동시켜 가면서 헤드 하단 주변 여러 지점에서 이격되는 거리를 측정했다. 에어 컵에 사용되는 압축 공기압은 0.5 - 2.5 bar (여기에 대응되는 공기 질량 유동율은 각각 1.93e-3 kg/s ~ 4.74e-3 kg/s이다.)이다.
3. 비접촉 헤드 모델링 및 수치 해석 설정
3.1 비접촉 헤드 모델링
실험과 수치해석에 사용되는 비접촉 에어 컵은 Fig. 5(a)와 같으며 컵 형태 및 제원은 외경 60 mm, 내경 47.34 mm, 내부 높이 34.4 mm인 원통 모양으로 헤드 내부 측면으로 두 개의 접선 방향의 공기 주입구(직경 2 mm)를 가지고 있는 보텍스(Vortex) 방식이다. 컵 내부 챔버에서 스월 흐름으로 진공을 발생시키면서 흡착 능력을 발생시키고 한편으로는 샘플 표면과 헤드 끝단(tip)사이에 토출되는 공기의 운동 에너지에 의해 비접촉 공간을 동시에 확보하는 원리이다.
하부 파지 대상이 되는 투명 수지 재질의 샘플은 500 mm × 330 mm 크기의 박판(t = 2 mm)이며 자중에 의해 탄성으로 휨이 존재한다. 헤드 하부의 토출 영역에서의 팁은 45° 챔퍼(chamfer)를 갖는 형태를 유지하여 토출과 관련하여 유동 메커니즘과 관계가 되며, 제원이 큰 형태의 보텍스 모양으로 안정적인 공기 흐름과 과다한 공기 소모량을 줄이고 비대칭 공기 주입구 두 군데를 적용했으며 2 mm 직경을 사용했다. Table 1에 해석 모델의 전체적인 설계 인자 및 조건을 정리하였다.
수치계산을 위한 모델링의 제원과 비접촉 간격 범위는 이전 연구 결과와 실험을 통하여 측정 확인 된 부분을 고려하여 정했으며 팁의 길이가 1 mm이고 측정 샘플 중량이 288.5 g이기 때문에 적정 사용 공기 유동율을 고려하여 공기압을 0.5 - 2.5 bar 수준에서 결정했다. 기타 파지를 위해 헤드 내부와 하부 끝단의 구조의 특성에 따라 나타나는 성능 그리고 하부 끝단에 해당되는 변수들에 의한 파지 능력 결과는 이전 연구에서 제시했다[1].
Fig. 5(b)와 같이 샘플의 직사각형 장축 방향으로 대칭 구조로 컵에 의한 유동영역과 이에 영향을 받는 고채 파지 부분의 영역으로 이를 기준으로 해석 모델링 영역은 절반 모양의 대칭 구조를 갖게 된다. 해석은 유체-구조 연성 FSI (fluid-structure interaction) 단방향 해석 방법이 적용되며 그러기 위해 3D구조로 보텍스 내부 챔버 유동 영역, 컵 하단 및 토출 유동영역, 그리고 파지 대상인 샘플 고체영역으로 연결되어 구성되며 각각 해석 도메인을 갖는다. 컵 하단 및 토출 유동영역은 컵 하단부를 거쳐 샘플 표면위로 토출되면서 거의 대기압 수준으로 이루어지기 때문에 컵 외경보다 큰 크기(DD)를 갖는 원통 영역으로 확대하였다.
3.2 수치 해석 설정 및 방법
연성해석으로 유체 영역의 유동 운동을 통하여 압력 분포를 얻어내어 그 결과를 고체 해석에서 샘플 표면에 경계 하중(load)조건으로 적용하여 컵의 팁 하단부 아래 비접촉 간격부분을 지지대로 하여 휨 정도를 분석하였다. 유동영역은 tetra 모양의 격자이며 미세 통로, 벽, 토출부위의 급격한 유동변화가 예상되는 부분은 매우 조밀한 모양의 비균등 격자를 사용했다. 격자 품질에 의한 신뢰를 확보하기 위해 성능 목표치인 진공흡입력 기준으로 일정 편차 내에서 이루어질 수 있도록 격자수를 조정하여 절점(node) 기준 약 720.3만개 수준에서 수렴 결정하였다.
해석 도구는 FSI-CFX이며 해석은 정상상태(steady-state)로 하였으며 모든 방정식의 수렴 조건은 10-4으로 설정하였다. Table 2에 경계조건을 포함한 나머지 설정 조건을 나타냈다. 질량 보존, 운동, 난류 방정식이 적용되며 작동 유체는 25℃ 공기로써 난류 모델은 표준 k-ε 모델에 따랐다.
4. 결과 및 고찰
4.1 에어 컵의 성능 평가를 위한 수치해석
FSI 연동 해석에서 우선 유동 해석을 수행했으며 Fig. 5(b)에서 에어 컵 하단에 일정 비접촉 거리를 두고 파지 물체가 하단 벽으로 직경 DD = 100 mm 크기로 존재하는 것으로 산정하였다. 이것은 실제로 거의 대기압 수준으로 토출하는 기체를 고려하여 경계조건을 주기 위해서이다. 압축 공기는 컵의 접선 방향으로 주입되어 벽면 가까이 스월 흐름을 유지하다가 팁 끝단에서 좁은 갭 사이로 사이클론 형태로 토출하는 과정으로 나타나게 되며 이 때 마지막 토출 단계에서 필요한 추력과 내부 공간에서 발생하는 진공과의 힘의 평형 상태를 유지하는 단계까지 컵 내부의 정상 상태를 가진다.
Fig. 6은 컵 내부의 정상 유동상태 결과로서 압력과 속도 분포를 보여주고 있다. 이 결과는 질량 유량율 3.38e-3 kg/s (작동압 1.5 bar)를 적용했으며 힘의 균형이 각각 0.3 mm, 0.7 mm, 1.0 mm에서 비접촉 간격으로 이루어짐을 전제로 했다. 이러한 전제는 실제 비접촉 거리는 컵의 구조와 사용 유량율, 샘플의 크기(하중) 등의 여러 조건에 의해 달라지지만 대체적으로 이전에 수행된 많은 결과[1,4,6,10,14]에서 도출한 비접촉 범위 내 (0.3 mm ~ 1.0 mm)에서 힘의 안정적(stable) 균형이 형성되어 파지되고 있는 점을 고려했다. 그중에서 상, 하한 갭과 중간 상태의 갭을 고려하여 비교 분석하고자 했다.
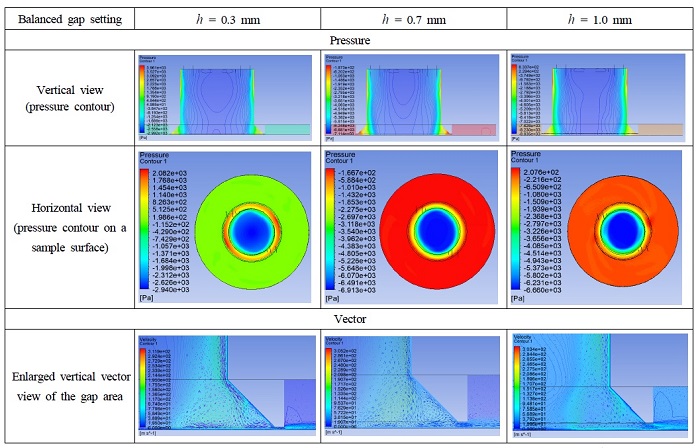
Isobars and vector fields in air cup; 3 different air gap settings (0.3, 0.7, 1.0 mm) and a flow rate (Q˙= 3.38e-3 kg/s)
주입 공기의 주 흐름을 통한 강한 전단력으로 내부의 공기를 지속적으로 유입시켜 외부로 지속적으로 토출함으로써 내부적으로 진공을 확보한다. 이 때 서로 다른 갭 환경에서 내부적으로 형성되는 분포 특성을 비교 할 수 있다. 주어진 상, 하한 갭 범위 내에서 수직면과 수평면으로 나타나는 압력 분포를 볼 때 작동압 1.5 bar에 의해 발생되는 내부 진공은 안정적이다. 그리고 현재 모델이 채택한 형상 설계에서 갭 하단부를 확대한 속도 벡터장을 보면 0.3 mm와 0.7 mm인 경우 모서리 수렴 영역에서 2군데서 순환(circulation)이 발생되고 있다. 하나의 순환은 출구 입구에서 일어나고 있으며 다른 하나는 내부로 크게 순환하는 흐름이다. 그러나 0.7 mm 경우는 토출과 함께 순환이 적절하게 이루어지고 있으나 상대적으로 0.3 mm의 경우는 출구의 순환이 일부 억제되고 있다. 토출 통로인 갭이 좁을수록 내부로 순환되는 비율이 커지며 실제는 빠른 속도로 밀어내기 위해 압력이 상승하게 되며 이것은 결국 추력의 상승으로 이어졌다.
반대로 1.0 mm인 경우는 토출 통로가 넓어지면서 토출구 주변의 순환은 거의 사라지고 큰 내부 순환 흐름은 존재했다. 주입 시 높은 에너지를 가지는 유동 흐름의 높은 전단 작용 위주의 유입 효과 외에도 크고 작은 순환 작용이 주 흐름의 경계면에서 이루어지는 유입의 효과가 낮아져서 진공에 차이가 있는 것으로 풀이된다. 이것은 임의의 비접촉 개방 두께를 전제로 하여 나타나는 컵 내부의 유동 구조를 볼 때 특정 수준에서 진공을 효율적으로 발생시키는 환경을 가지는데 이는 사용유량, 컵의 제원과 형상 구조에 따라 갭의 크기에 의해 임계적인(critical) 상태를 충족하기 위한 관계로 얽혀 있다.
Fig. 7은 샘플 표면위에 작용하는 압력 분포를 바접촉 사용 가능 범위인 0.3 ~ 1.0 mm를 기준으로 그리고 유량율별로 비교하였다. Fig. 7(a)는 0.7 mm의 갭 설정을 전제로 하고 사용 압력에 의해 적용되는 유량율의 변화에 따라 컵 하단부 샘플 표면 위에 나타나는 압력 분포이다. 동알 컵 제원에서 유량율의 증가는 높은 운동에너지를 동반하게 되고 그 만큼 더 벽 가까이서 높은 전단력과 강한 순환을 유발하게 되어 비례적으로 진공은 높아졌다. 또한 Fig. 7(b)에서는 3.38e-3 kg/s를 적용하고 갭을 0.3 - 1.0 mm까지 임의로 설정하였을 때 진공 발생 효율은 0.7 mm가 좋다. 컵 하단 중심을 통과하는 단순 압력 분포선 비교에서는 0.6 mm에서 0.9 mm까지 큰 차이가 없다. 이것은 현재 사용하고 있는 유량율 기준으로 0.7 mm 갭에서 임계적인 특성을 보여주고 있다는 뜻이다. 이 임계값은 하단부의 팁 길이(T)나 컵의 직경 그리고 하단 경사부의 모따기(chamfer, c) 형상에 변화된다. 이러한 변화에 대한 일부 연구 결과는 이전 단계[1]에서 토의 된 바 있다. 수직 아래로 미는 큰 추력으로 갭의 크기를 증가시키기 위해서는 이러한 변수들의 조정이 불가피하다.
DD = 100 mm의 직경으로 산정한 샘플 표면위에 작용하는 파지력(흡착력)을 기준으로 3가지 다른 질량 유량율을 적용하고 갭을 0.3 mm에서 1.0 mm까지 변화를 주었을 때 비교되는 결과는 Fig. 8에서 보여준다. Fig. 7(a)에서 확인된 진공 발생 효율면 기준으로 무의미한 낮은 유량율인 두 경우를 제외했으며 하변 전체 바닥면에 수직으로 작용하는 압력을 대상으로 파지력을 계산하였다.
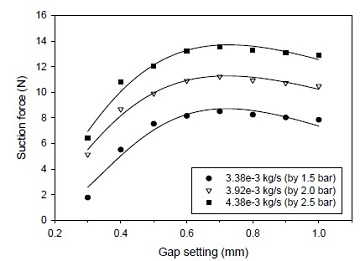
Suction forces according to varying gap settings when using 3 operating pressures and a constant gap of 0.7 mm
파지력은 0.7 mm 갭을 유지했을 때 정점으로 갭을 늘리는 경우 서서히 저하되는 것을 알 수 있다. 특히 0.3 mm 갭 수준으로 유지를 산정하는 경우에는 매우 급격하게 저하되었다. 파지력은 주입 유량율에 거의 비례하고 있으며 상용 에어 컵인 SMC 사이클론 ϕ60 모델 기준[2]으로 공기소모량 148 l/min, 샘플(워크)하중 0.45 N을 사용하여 7 N 수준의 파지력으로 워크와의 거리 0.7 mm 로 설계 사양하는 경우와 비교해볼 때 본 연구에서는 공기 소모량 0.338e-3 kg/s (171.5 l/min)을 적용하여 8.5 N을 가짐으로써 공기 소모량을 고려하면 파지력 대비 공기소모량 비율로 0.0472 : 0.0495으로 거의 비슷한 결과를 가졌다.
수치적 계산에서는 식 (2)의 자중(W)가 빠지기 때문에 파지력은 순수 적용 샘플 표면에 작용하는 압력으로 실제 적용에서 있어서 W = mg가 각각 파지력을 넘어서지 않는 한 안정적(stable)인 파지 범위 또는 가능한(feasible) 파지 범위에 해당된다. 또한 갭의 크기가 1.1 mm 이상에서 일정 범위 (2 mm 갭 수준)까지 증가하여도 이론적인 계산뿐만 아니라 실제에서도 자중에 따라 가능한 파지 범위 대를 유지할 수 있으나 내부 유동의 힘의 균형을 통해 안정적 또는 반발(repulsion) 조절이 이루어진다.
(2) |
여기서 Flifting은 컵이 샘플 표면위로 파지 가능한 갭의 범위로 접근함에 따라 부상시키는 힘이며 순수 파지력으로 비접촉 갭에서 균형을 이루는 힘이다. pvortex는 컵에 의해 샘플 표면위에 형성되는 압력(Pa)으로 진공(vacuum)과 추력(thrust)으로 이루어진다. r은 컵의 반지름이다.
4.2 변위 센서를 활용한 비접촉 이격(h) 측정
Fig. 9는 Fig. 2의 실험 측정 장치를 통하여 DAQ로 받아들인 10초 동안 획득된 전압 출력 값이다. Fig. 3에서 l* 변환 거리를 구하기 위해 컵 하단부에 샘플 평판을 접촉시켜 얻어지는 신호값(A)을 구했다. 이때 컵 중심 간의 대칭간격을 100 mm로 유지하고 에어 컵의 주입 압력을 0.5 bar에서 2 bar까지 각각 시용했다. 그리고 컵 하단부에 일정 비접촉 거리에서 파지되는 평판의 하단부까지 거리 l에 해당되는 신호값을 각각 구했다.

Measured voltage line detected by the displacement laser sensor at a cup tip boundary during about 10 s with different working pressure and 100 mm half distance between air cups (equivalent to mass flow rate); sample thickness 2 mm
같은 방법으로 컵 중심 간의 절반 거리인 b = 125, 150 mm를 추가적으로 유지하고 주입 압력 1.0 ~ 2.0 bar를 사용하는 유량율을 적용하여 Table 2의 에폭시 레진(epoxy resin) 물성의 평판을 파지했을 때 Fig. 10과 같이 컵에 파지되는 평판 하단부의 5개 지점을 대상으로 측정했다. 5개 지점은 컵 중심인 s1을 기준으로 30 mm으로 간격을 유지했다. 컵이 생성하는 진공과 추력에 의해 형성되는 비접촉 파지능력은 컵 하단부 다섯 지점을 대상으로 획득되는 전압 신호의 평균 크기를 식 (1)에 의해 구한 비접촉 거리에 의해 나타냈다.
비접촉 거리 기준으로 Fig. 10을 분석하면 컵 하단부인 중심부(s1)에서 비교해보면 질량 유량율이 높을수록 내부 형성되는 진공 힘은 높아지지만 질량보존에 의해 토출하기 위한 추력도 상대적으로 같이 증가하면서 힘의 평형은 비접촉 갬의 미세한 차이 범위 내에서 이루어지고 있음을 알 수 있다. 또한 주입 압력에 의한 유량율에 따라 b = 100 mm인 경우 0.33 ~ 0.48 그리고 b = 125 ~ 150 mm인 경우 0.43 ~ 0.48 mm 범위로 측정되었다. 이 결과는 컵의 배열(간격)에 의해 파지에 미치는 지지(support)가 달라서 편중되어 발생되는 영향이다.
Fig. 10의 처짐량 결과로 분석해보면 두 컵 간격이 상대적으로 좁은 경우(b = 100 mm)와 큰 경우(b = 150 mm)는 중간 단계 경우(b = 125 mm)보다 평판 처짐량이 가장자리와 중간 지점에서 큰 것을 알 수 있다. 적절하게 컵을 배열하여 운용할 경우 처짐량을 최대로 억제하고 편평도를 높여 사용할 수 있다. b = 125 mm와 1.5 bar 사용하는 경우 직진도는 150 mm 기준으로 0.1 mm 이내에 충분히 해당된다. 파지가 가능한 상태에서 안정적인 범위에 충분히 들어갈 수 있으며 샘플 자중에 따라 1 bar 이하 적용으로 유량율을 저감시킬 수도 있다.
컵 하부에 바로 위치하는 s1, s2, s3 기준으로 보면 현재 물성값을 가지는 샘플의 탄성 처짐 범위를 극복하고 컵 내부에서 진공의 힘으로 지지하는 안정적 비접촉 범위 내에서 작동되고 있다.
4.3 에어 컵 성능을 평판에 적용한 비교 분석
지금까지 논의에서 에어 컵 위주로 수치적으로 실험적으로 비접촉 거리에 대하여 다루어졌다. 수치적으로 0.7 mm 비접촉 거리에서 가장 파지력 효율이 발생되고 있으나 실험에서는 s1 기준으로 자중과 여러 처짐량 등으로 s1, s2, s3의 평균으로 0.6 mm 수준에서 비접촉 균형이 형성되었다.
이를 검증하기 위한 연성해석으로 에어 컵에서 획득한 하단부 압력을 압력 경계 조건으로 부여하고 샘플 자체의 자중을 고려하고 그리고 컵 팁 하단부 중심 영역을 원점으로 고정하는 형태로 계산한 결과는 Fig. 11에 도시되었다. 결과는 변형량(처짐)으로 표시하였으며 샘플의 물성값은 표 2를 따르고 컵 사이의 간격 b = 100, 125, 150 mm 그리고 갭은 0.6 mm에서 이루어졌다.
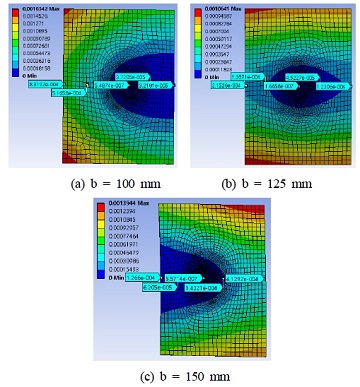
Deformation of a sample plate with holing power created by a cup with 1.5 bar working pressure, 0.6 mm gap; (a) b = 100 mm, (b) b = 125 mm and (c) b = 150 mm
Fig. 11에서 컵의 배치구도에 따라 대칭구조(대칭면은 오른쪽)로 나타난 장방향으로 처짐량 결과를 보면 Fig. 10에서 언급한 결과와 유사한 형태로 진행되었으며, 컵의 하단 및 팁 주변에서 파지가 집중 이루어지면서 횡 또는 종 방향으로 처짐이 발생하게 되는데 컵의 배치(간격)에 따라 그 처짐의 차이는 존재했다. 컵 중심을 통과하는 대칭적인 장방향 선을 기준으로 컵 정중앙 하단부는 일정 간격(비접촉 갭 0.6 mm)으로 유지한다고 볼 때 여기서는 그 처짐량 차이는 e-4 mm수준으로 거의 변함이 없다. 컵의 팁 하단부 주위에서는 b의 크기순으로 차례로 변화량은 0.037205 mm, 0.045227 mm, 0.14321 mm로 비접촉 변위 0.6 mm에 비해 적은 수치로 변화했다. 그러나 컵 간의 거리가 커짐에 따라 처짐량이 증가함을 알 수 있다.
또한 컵의 하단부위를 벗어난 왼쪽 가장자리 위치에서는 차례로 0.6 mm 기준에서 0.83192 mm, 0.21536 mm, 0.1266 mm의 처짐 변화량을 가졌다. 적절한 유량율( 1.5 bar 적용)을 사용하고 컵의 배치간격(b)의 변화로 통하여 간단하게 b = 125 mm를 유지할 때 안정적 비접촉 변위에 근접하는 편차가 낮은 편평도로 좋게 분석되었다.
5. 결 론
본 연구는 비접촉 에어 컵의 설계 사양을 재구성하여 효율적인 유량율을 소비하는 것을 전제로 얇은 평판을 안정적으로 파지하기 위해 2개의 컵을 적용했다. 컵은 대형 평판에 유리한 보텍스 형태 및 큰 제원 수준으로 구성되었으며, 컵의 안정적인 진공과 추력을 균형 있게 유지하는 비접촉 갭과 파지력을 수치 해석적으로 고찰하고 실험적으로 비교 확인했다.
컵의 하단부에 대한 유동 해석으로 컵 내부의 구조 특성과 사용 유량율 (4,38e-4 kg/s까지)에 따라 8 ~ 14 N의 파지력을 그리고 효율적 비접촉 거리가 파지 가능한 유효범위인 0.3 ~ 1.0 mm의 비교를 통하여 0.7 mm임을 모델링을 통하여 도출했다. 그리고 변위 센서를 이용하여 샘플 자중(2.827 N)을 고려하는 실 부상 거리측정에서 평균적으로 0.6 mm로 비접촉 이격 되는 것을 확인했다.
연성해석을 이용하여 컵의 배치에 따라 압력 분포를 경계 조건으로 활용하여 샘플(수지 계열 투명 판재)의 비접촉 파지되는 컵의 정중앙부에 비해 이루어지는 전체적인 판재의 처짐량을 계산 분석했을 때 처짐 변화량은 컵의 팁 토출 부 하단부에서는 비접촉 이격 차원 수준보다 매우 작으며 컵에서 멀어져 직접적인 파지 힘이 없어 탄성에 의해 휨이 유지되는 경우에도 비접촉 이격 차원 수준에서 이루어졌다.
적절한 유량을 사용하고 컵 간의 간격 조정만으로 전체적인 편평도를 향상시킬 수 있음을 확인하였으며, 전체적인 샘플의 무게에 대비하여 컵의 파지력이 비접촉 가능성 범위 내에서 우세하면 충분히 적절한 배열 조건 확보와 함께 대형 판재의 비접촉 파지에 효율성을 있음을 제시하였다.
Acknowledgments
이 연구는 2019년 한국연구재단 개인기초연구사업(기본연구) 과 제번호 2019R1F1A1056931의 연구비 지원으로 수행되었습니다.
References
-
Kim, J. H., Sung, J., 2019, Influence of Air Head Shape on Lifting Force and Stability of Swirl Flow in a Vortex-Type Non-Contact Gripper, Journal of the Korean Society of Manufacturing Technology Engineers, 28:4 224-231.
[https://doi.org/10.7735/ksmte.2019.28.4.224]
- SMC viewed 13 Jul. 2020, Web catalogue.
-
Fantoni, G., Capiferri, S., Tilli, J., 2014, Method for Supporting the Selection of Robot Grippers, Procedia CIRP, 21 330-335,https://doi.org/10.1016/j.procir.2014.03.152, .
[https://doi.org/10.1016/j.procir.2014.03.152]
-
Li, X., Kagawa, T., 2014, Theoretical and Experimental Study of Factors Affecting the Suction Force of a Bernoulli Gripper, Journal of Engineering Mechanics, 140:9 04014066.
[https://doi.org/10.1061/(ASCE)EM.1943-7889.0000774]
-
Dini, G., Fantoni, G., Failli, F., 2009, Grasping Leather Plies by Bernoulli Grippers, CIRP Annuals - Manufacturing Technology, 58 21-24.
[https://doi.org/10.1016/j.cirp.2009.03.076]
-
Li, X., Kagawa, T., 2013,Development of a New Noncontact Gripper Using Swirl Vanes, Robotics and Computer-Integrated Manufacturing, 29 63-70.
[https://doi.org/10.1016/j.rcim.2012.07.002]
-
Zhao, J., Li, X., 2016, Effect of Supply Flow Rate on Performance of Pneumatic Non-Contact Gripper Using Vortex Flow, Experimental Thermal and Fluid Science, 79 91-100.
[https://doi.org/10.1016/j.expthermflusci.2016.06.020]
-
Kim, J., Jeong, Y., Lee, T., Kim, T., Jung H., 2013, Non-Contact Level on Air Levitation Table with Porous Chamber Array, Journal of the Korean Society of Manufacturing Technology Engineers, 22:6 913-920.
[https://doi.org/10.7735/ksmte.2013.22.6.913]
-
Lee, T., Yu, J., Jung H., Kim, J.-H., Kim, J., 2013,Development of the Air Floating Conveyor System for the Large Glass Sheet, Journal of the Korean Society of Manufacturing Technology Engineers, 22:4 635-642.
[https://doi.org/10.7735/ksmte.2013.22.4.635]
-
Li, X., Kawashima, K., Kagawa, T., 2008, Analysis of Vortex Levitation, Experimental Thermal and Fluid Science, 32 1448-1454.
[https://doi.org/10.1016/j.expthermflusci.2008.03.010]
-
Savkiv, V., Mykhailyshyn, R.,Duchon, F., Mikhalishin, M., 2017, Energy Efficiency Analysis of the Manipulation Process by the Industrial Objects with the Use of Bernoulli GrippingDevices, Journal of Electrical Engineering, 68:6 496-502.
[https://doi.org/10.1515/jee-2017-0087]
-
Savkiv, V., Mykhailyshyn, R.,Duchon, F., Fendo, O., 2017, Justification ofDesign and Parameters of Bernoulli-Vacuum GrippingDevice, International Journal of Advanced Robotic systems, November-December, 1-10.
[https://doi.org/10.1177/1729881417741740]
-
Davis, S., Gray, J. O., Caldwell.,D. G., 2008, An End Effector Based on the Bernoulli Principle for Handling Sliced Fruit and Vegetables, Robotics and Computer-Integrated Manufacturing, 24 249-257.
[https://doi.org/10.1016/j.rcim.2006.11.002]
-
Kim, J. H., Lee, S.-J., 2015, Configuration of Noncontact Grip System for Carrying Large Flat Sheets Using Vacuum Air Heads, Journal of Tribology, 137:4 041103.
[https://doi.org/10.1115/1.4030710]
Research Professor in NDT Research Center, Seoul National University of Science and Technology.His research interest is Tribology.
E-mail: joonk61@seoultech.ac.kr
Graduated M.Sc. Program in theDepartment of Mechanical and Automotive Engineering, Seoul National University of Science and Technology.His research interest is Visualization and Fluid Mechanics.
E-mail: yg6223@naver.com
Professor in theDepartment of Mechanical and Automotive Engineering, Seoul National University of Science and Technology.His research interest is Flow Visualization.
E-mail: jysung@seoultech.ac.kr