
용접부 샌드 블라스팅 표면처리에 따른 부식 영향 연구
Abstract
Recently, consumer complaints on car corrosion have been steadily increasing. The main cause of corrosion is calcium chloride, which is commonly used in winter, and the lower parts of the car, such as suspension, are more affected by it. Corrosion affects the parts durability by weakening them and threatening the passenger safety if exposed to continuous loads. Therefore, herein, a method of improving corrosion performance was studied by applying the surface treatment to the welding part of the steel plate used in the manufacture of cross members among automobile suspension parts. Specimens were manufactured through brushing and the sand blasting surface treatment, and cross-cut adhesion tests and repeated corrosion tests were conducted. The test results showed that the cause of the electrodeposition coating and corrosion defects was the oxide layer formed from oxidation after welding, and the sand blasting surface treatment was very effective in removing the oxide layer.
Keywords:
Sand blasting, Cyclic corrosion test, Electro deposition coating, Corrosion protection, Surface treatment1. 서 론
최근 자동차 부식으로 인한 소비자 불만이 증가하고 있는 추세이다. 연례 자동차 기획조사에 의하면 6~10년 된 차량을 기준으로 배기통, 하체프레임, 현가장치, 연료통, 사이드 실 패널 부분에서 부식이 가장 취약한 것으로 알려져 있다[1]. 특히 겨울철 제설 목적으로 사용하는 염화칼슘이 주된 원인이며 현가장치와 같이 하부에 위치한 부품은 영향을 많이 받는다고 보고되고 있다[2]. 현가장치(suspension) 중 크로스멤버와 같이 크고 작은 구멍이 많은 부품에 염화칼슘이 유입될 경우 배출이 어렵고 높은 수분과 염화이온 분위기를 형성하여 국부부식의 형태로 나타난다. 국부부식이 진행되면 항복응력 이하에서도 파단 현상이 나타나고 지속적으로 반복하중을 받을 경우 급속파단이 발생하여 부품 내구성 및 승객의 안전을 위협한다[2-3]. 높은 신뢰성을 요구하는 크로스멤버는 부식을 최소화하고자 도장 부착력이 높고 방청 효과가 뛰어난 전착도장(electro deposition coating) 공정을 진행한다.
그런데, 크로스멤버 부품의 조립은 용접으로 접합되어 제작되기 때문에 용접 슬래그로 인한 전착도장 품질 문제가 자주 발생하고 있으며, 부식을 촉진시키는 요인으로 작용한다고 알려져 있다[4].
Fig. 1은 10년 동안 주행한 자동차의 리어 크로스멤버(rear cross member) 부품의 사례이다. 표시된 용접라인을 따라 도장층이 박리되었고 부식이 발생하여 주변으로 전파된 것을 알 수 있다. 이와 같은 문제 개선을 위한 방법으로 자동차 회사들은 용접 후 브러싱(brushing) 표면처리, 슬래그 저감 와이어 사용, 용접조건을 최적화하는 등 많은 노력을 하고 있지만 개선이 미흡한 실정이다[5].
자동차용 강판 용접부에 쇼트 블라스팅(shot blasting) 표면처리를 하여 부식성 향상에 관한 선행연구는 보고되었으나 열영향부 경계와 같이 엣지가 있는 부분은 용접 슬래그(slag) 제거가 힘들며 제거를 위해 과도하게 표면처리를 할 경우 부품 두께가 감소되는 문제점이 제기되었다[4].
따라서 부품의 두께 감소 없이 슬래그 제거가 가능한 샌드 블라스팅(sand blasting) 표면처리 방법의 가능성을 조사하고 분석하였다. 샌드 블라스팅은 약 0.037~1.19 mm 굵기의 모래입자를 일정한 속도로 금속표면에 분사하여 발생하는 운동에너지를 전이함으로써 표면에너지를 높이고 피닝 효과에 의한 압축 잔류응력 형성으로 경도와 내식성이 향상되는 소성가공이다. 과거에는 부식된 선박이나 건축물의 녹을 제거하고 도장을 위한 전처리 공정으로 많이 사용되었으며 최근 다양한 분사입자 및 마이크로 샌드 블라스팅 장비가 개발되어 높은 수준의 가공 정밀도를 요구하는 항공기 전자장비, 의료용 보철 등에 적용되어 사용되고 있다. 그러나, 자동차용 강판을 대상으로 샌드 블라스팅 표면처리를 적용한 연구 사례에 대해서는 보고되지 않은 실정이다[6-7].
본 연구는 자동차 강판을 대상으로 샌드 블라스팅 표면처리를 진행하여 용접과정에서 발생하는 슬래그 제거 효과와 이에 따라 도장 부착성과 부식성능에 미치는 영향을 비교하고 분석하였다. 이러한 연구결과를 통해 자동차 부품이 부식으로 인한 손상을 줄이고, 수명이 향상될 것으로 기대된다.
2. 실험 준비
2.1 실험개요
본 실험재료는 용융아연도금강판(hot dipped galvanized iron)으로 자동차 현가장치 중 특히 리어 크로스멤버에 부식 방지 목적으로 많이 사용되는 강판이다. 용융아연도금강판은 아연도금을 합금화하여 처리한 강판으로서 용접 및 가공성이 우수한 장점을 가지고 있으며, 상세한 기계적 성질은 Table 1에 나타냈다.
실험 시편은 용접 후 표면처리를 하지 않은 일반 시편(normal)과 브러싱, 샌드 블라스팅 표면처리한 것으로 분류하였다. 분류된 시편은 전착도장 후 도장 부착성 시험과, 복합부식시험을 통하여 평가하고자 한다.
2.2 용접시편
양산조건과 유사한 시편 제작을 위해 YASKAWA 社의 용접로봇과 Fronius 社의 TPS4000 컨트롤러를 사용하여 CMT(cold metal transfer) 용접을 하였다. 용접조건은 Table 2와 같으며 리어 크로스멤버 구조상 겹치기 이음(lap joint) 이 많은 것을 고려하여 겹침 용접을 하였다.
2.3 표면처리
Fig. 2는 본 실험에서 사용된 시편의 표면처리 범위와 결과를 나타내고 있다. 표면처리 범위는 Fig. 2(a)와 같이 용접 시편에 형성된 슬래그 면적을 고려하여 선정하였으며, Fig. 2(b)와 같이 비드부(bead, BD)와 열영향부(heat affected zone, HAZ) 영역에 표면처리를 적용하였다. Fig. 2(c)는 브러싱 표면처리를 진행한 시편으로 크로스멤버 제작에 사용되는 양산장비를 활용하여 진행하였고, Fig. 2(d)는 샌드 블라스팅 표면처리를 진행한 시편으로 EST 社에서 제작한 흡입식 샌딩 장치를 활용하여 Fig. 3, Table 3과 같은 조건으로 진행하였다. 표면처리 결과 Fig. 2(c), (d) 시편의 비드부와 열영향부에 슬래그가 제거된 것을 확인할 수 있었다.
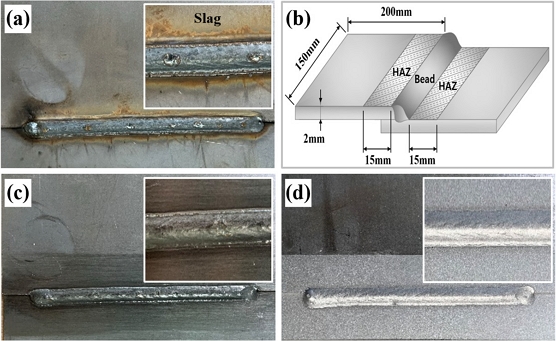
Results of surface treatment specimens: (a) welding specimen, (b) dimensions of surface treatment, (c) brushing specimen, (d) sand blasting specimen
3. 실험 결과
3.1 도장 부착성 시험 (cross-cut adhesion test)
도장 부착성 시험은 시편의 도막 부착성을 평가하기 위한 시험으로 ASTM D3359 (American society for testing and materials)를 참고하였다[8].
실험방법은 각 시편의 열영향부 상단(upper heat affected zone, Upr HAZ), 열영향부 하단(lower heat affected zone, Lwr HAZ), 용접 비드부 영역에 금긋기 칼을 이용하여 0.5 mm의 일정한 격자의 패턴을 만들었으며, Fig. 5(a)와 같은 방법으로 테이프를 부착하였다. 부착된 테이프는 3분 경과 후 Fig. 5(b)와 같이 120˚ 각도로 균일하게 인장력을 가하여 진행하였다. 실험에 사용된 테이프는 3M #610 제품으로 필름두께 0.036 mm, 연신률 15%, 점착력 47N/100 mm의 물리적 성질을 가지고 있으며 가로, 세로 각각 25.4 mm, 70 mm 길이로 절단하여 사용하였다.
Fig. 6은 각 시편의 실험 분석결과를 나타낸다. 용접 후표면처리를 하지 않은 시편은 용접 슬래그로 인하여 미도장 구간이 발생하였으며, Fig. 6(d)~(f)와 같이 열영향부와 비드부의 전착도장 도막(electro deposition coating, E-coat)이 박리되었다. 브러싱 시편은 Fig. 6(g)~6(i)와 같이 도막 박리현상은 없으나 열영향부 경계(fusion line)에서 미세한 미도장 구간이 존재하였다. 반면에 샌드 블라스팅 시편은 Fig. 6(j)~6(l)과 같이 미도장 구간과 도막 박리 현상 없이 도장층이 유지되는 것을 확인하였다.
도장 부착성은 식(1)과 같이 표현할 수 있으며, G는 도장 결합강도, P는 테이프에 가해진 인장력, B는 접착면적, θ는 테이프 접착면과 인장력이 가해지는 각도를 나타내며 P, B, θ값은 동일한 조건으로 진행하였다[9].
(1) |
이때 표면처리를 하지 않은 시편의 도장 결합강도 G값이 테이프의 점착력보다 작기 때문에 Fig. 6(d)~(f)와 같이 도막이 박리되는 현상이 발생하였다. 이는 전착도장 공정에서 진행하는 화학적인 전처리 방법으로는 도장 부착성 향상이 어렵다는 것을 말하며, 물리적인 방법이 필요하다는 것을 알 수 있다.
3.2 복합부식시험 (cyclic corrosion test, CCT)
CCT 시험은 제품의 부식성능 평가를 위한 방법으로 일정한 온도에서 시험하는 염수분무시험(salt spray test, SST) 과는 다르게 온도 변화와 습윤 상태를 구현하여 실차 주행조건과 유사하게 시험하는 방법이다. 시험은 Fig. 7과 같이 ITABASHI 社에서 개발된 장비를 사용하여 건조, 염수침지, 건조, 습윤, 건조, 저온의 cycle을 반복하였다. 1 cycle은 12시간 동안 진행된 CCT 시험 시간을 말하며 총 42일(1008시간) 동안 84 cycle의 부식시험을 하였다.
Fig. 8은 CCT 시험을 완료한 시편 외관을 분석한 것이다. Fig. 8(a), (b)시편에서 도장 부풀음(blister)과 부식(corrosion) 결함이 발생하였고, Fig. 8(c)시편은 결함 없이 도장층이 유지된 것을 확인하였다. 시편에 발생한 결함의 원인을 분석하고자 Fig. 9와 같이 모재부(BM), 비드부(BD), 열영향부(HAZ)에서 SEM(scanning electron microscope) 단면 분석을 진행하였다.
Fig. 10은 표면처리를 하지 않은 시편의 단면을 분석한 것으로 시험 전 Fig. 10(b), (c)와 같이 비드부와 열영향부에 약 10~11 μm의 산화층(oxide layer)과 도장층이 존재하였으며, 시험을 진행하는 과정에서 도장층이 박리되고 산화층이 약 20~30 μm으로 증가한 것을 Fig. 10(e), (f)를 통하여 확인하였다. Fig. 11은 브러싱 시편의 단면을 분석한 것으로 시험 전 약 5~6 μm의 산화층과 도장층이 존재하였고, 시험 후 도장층이 유지된 것을 확인하였다. 그러나 Fig. 11(e), (f)에 도장층이 존재하지 않는 것은 SEM 분석 시편을 제작하는 과정에서 단면 절단 시 컷팅날 진동에 의해 도장층이 박리되었기 때문이다. 그 원인은 CCT 시험 중 습도와 온도 변화가 반복되어 도장 결합강도가 낮은 부분에 도장 부풀음이 발생하고 내충격성이 감소하였기 때문에 박리된 것으로 판단된다. Fig. 12는 샌드 블라스팅 시편의 단면 분석한 것으로 Fig. 12(b), (c)와 같이 시험 전 산화층이 완전히 제거되었고 Fig. 12(e), (f)와 같이 시험 후에도 약 25 μm의 도장층이 유지된 것을 확인하였다.
결함이 발생한 시편 Fig. 8(a), (b)의 공통점은 시험 전 산화층이 존재하였고 Fig. 8(c) 시편은 산화층이 존재하지 않는 것을 알 수 있다. 또한 브러싱 표면처리의 경우 슬래그 제거는 가능하지만 산화층 제거에는 미흡하였다. 반면 샌드 블라스팅 표면처리는 슬래그 제거뿐만 아니라 산화층 제거에 매우 효과적이었다. 샌드 블라스팅은 고압으로 미세한 모래입자를 분사하기 때문에 용접 슬래그와 산화층 제거가 가능하고 표면 거칠기를 형성한다. 표면 거칠기가 증가하면 접착 메커니즘에 의해 접착 면적이 넓어지고, 분자 간의 상호작용이 증가되므로 접착성이 향상되어 도장층이 유지된 것으로 판단된다[10-11]. 하지만 과도한 표면처리를 할 경우 소재 두께가 감소하므로 적절한 표면처리를 통한 표면 거칠기 형성이 필요하다. 이와 같은 결과를 통하여 용접이 적용된 부품의 전착도장 공정에서 발생하는 부식 발생의 원인은 기존에 보고된 용접 슬래그보다는 용접 후 산화되어 형성된 산화층이 더 많은 영향을 미치는 것을 알 수 있다.
4. 결 론
본 연구는 자동차 현가장치 중 리어 크로스멤버 제작에 많이 사용되는 590 Mpa급 강판을 대상으로 브러싱, 샌드 블라스팅 표면처리가 부식성능 향상에 미치는 영향을 연구하였다.
1) 도장 부착성 시험결과 표면처리를 하지 않은 시편은 도막이 박리되었으나 브러싱, 샌드 블라스팅 표면처리를 한 시편은 도막 박리 결함이 없었다.
2) CCT 시험 분석결과 용접부 부식의 주 원인은 용접 슬래그가 아닌 용접 후 형성된 산화층이 도장 부착성을 감소시키고 부식을 촉진시키는 원인으로 작용하는 것을 알 수 있다.
3) 표면처리하지 않은 시편과 비교하였을 때 브러싱 시편의 산화층 제거 효율은 약 50% 정도로 산화층 두께 감소에 영향을 주었고, 샌드 블라스팅 시편의 제거 효율은 100%로 산화층 제거뿐만 아니라 표면 거칠기를 형성하여 도장 부착성을 향상시킨 것으로 판단된다.
4) 향후 자동차 산업에서 부식성능 문제점이 대두되는 것을 고려할 때 샌드 블라스팅 표면처리를 양산에 접목할 경우 전착도장 품질과 부식성능 향상에 효과적으로 작용할 것으로 판단되며, 기술 확대 적용을 위하여 보다 다양한 연구가 활발히 지속되어야 할 것으로 생각된다.
Acknowledgments
이 연구는 산업통상자원부(MOTIE)와 한국에너지기술평가원(KETEP)의 지원을 받아 수행한 연구 과제입니다. (no.20206410100080).
References
- ConsumerInsight., 2021, viewed November 20, 2022, There is more corrosion on the ‘bottom’ than on the ‘painting’, and the ‘exhaust pipe’ is the worst, <https://www.consumerinsight.co.kr/voc_view.aspx?no=3205&id=pr4_list&PageNo=1&schFlag=0, >.
- Kim, S. C., 2021, viewed November 20, 2022, Calcium chloride, the cause of car corrosion... it must be removed before going to winter, Chemical News, < http://www.chemicalnews.co.kr/news/articleView.html?idxno=3719, >.
- Ki, W. T., Park, K. D., Park, S. M., Moon, K. S., 2008, The Effect of Compressive Residual Stress according to Corrosion Fatigue Life of Automobile Suspension Material, Transactions of the Korean Society of Automotive Engineers, 16:5 1-7.
-
Fujimoto, H., Akioka, K., Tokunaga, M., 2017, Effects of Shot Blasting on Corrosion Properties after Electrodeposition and Fatigue Properties of Arc Welds in Automotive Steel Sheets, Mater. Trans., 58:12 1715-1720.
[https://doi.org/10.2320/matertrans.P-M2017838]
- Lee, S. L., 2016, A Study on the Improvement of Welding Quality of CMT Weldment for Galvanized Steel Sheets(SGARC 440), Master Thesis, Chosun University, Republic of Korea.
- Kim, G. S., Han, S. W., Hyun, C. H., 2005, Development of Corrosion Rust Removing Unit for Small Ship Propeller, Journal of Ocean Engineering and Technology, 19:6 72-77.
- Kim, H. J., Choi, J. B., Kim, D. K., Choi, J. H., 2020, A Study on Properties of Aluminum Metal Surface by Sandblast Process and the Improvement of Electric Contact Resistance of Avionics, Proceedings of KSPE 2020 Conference, 760-761.
- ASTM, 2017, Standard Test Methods for Rating Adhesion by Tape Test, D3359-17, ASTM International, U.S.A..
- Park, D. M., 2021, Bonding Strength Analysis through T-peel Test in Ni-CNT-Ni Structure, Master Thesis, Pusan National University, Republic of Korea.
-
Lee, M. S., Kim, H. H., Kang, C. G., 2013, Effect of Surface Roughness of Al5052/CFRP Composites on the Adhesion and Mechanical Properties, Composites Research, 26:5 295-302.
[https://doi.org/10.7234/composres.2013.26.5.295]
-
Sharma, V., Sabiruddin, K., 2020, A Comparative Study of Sand-blasted and Electro-discharge-machined Surfaces of Steel Substrates, Sādhanā, 45 50.
[https://doi.org/10.1007/s12046-020-1267-x]
PhD. candidate in the Department of Mechanical Engineering, Ajou University.
His research interest is welding quality and Manufacturing processes.
E-mail: bcd5417@naver.com
Assistant Manager in Advance Verification Team Institute of technology, Seojin Industrial.
His research interest is automobiles Manufacturing process.
E-mail: dhkim1@seojin.com
General Manager in Advance Verification Team Institute of technology, Seojin Industrial.
His research interest is Manufacturing process using advanced mateirals.
E-mail: msong2@seojin.com
Professor in the Department of Mechanical Engineering, Ajou University.
His research interest is novel manufacturing processes.
E-mail: princaps@ajou.ac.kr