
단변량 지수 분석기반의 사출성형 불량원인 분석방법론 개발
Abstract
Plastic molding is an important manufacturing process due to its high productivity; rapid fault analysis is also important because of its high production volume. This study presents a fault diagnosis framework for plastic injection molding processes based on univariate analysis and association rules. The proposed approach divides process variables into several partitions. For each partition, we calculate support, confidence, and lift values to discover how these cause or are associated with defects. Using those results, we present visualization plots of the production data gathered from a plastic injection-molding machine. In the experimental section, we examine how the partitioned process variables are related to defects. In this way, workers not familiar with mathematics or data analytics can perform defect analyses and obtain an intuitive basis to easily interpret how plastic injection molding defects are related to process variables.
Keywords:
Injection molding, Data mining, Fault cause analysis, Univariate analysis, Association rules1. 서 론
1.1 사출성형 개요
사출성형은 플라스틱 원료를 가공하는 성형공법 중의 하나로 주조, 금형, 프레스, 용접 등과 함께 국가기반 산업의 근간을 이루는 주요 뿌리기술 중의 하나이다. 사출성형은 매우 큰 시장규모를 갖고 있지만 그만큼 경쟁도 치열해서 제조원가경쟁력이 매우 중요하다. 그러나 그 중요성에 비해 대부분의 중소중견 사출업체의 품질관리나 불량원인분석 역량은 많이 부족한 실정이다.
주요 사출공정순서는 재료가 호퍼에 공급되고 가열된 실린더 내부에서 스크류로 이동되어 용융되고 혼합이 된다. 그리고 용융물이 고압으로 금형으로 사출 후 냉각되고 이형되면 새로운 사이클이 다시 시작된다.
1.2 사출성형 불량원인분석 문제
사출공정을 통해 생산된 제품의 품질은 제품설계, 금형의 완성도, 성형기의 특성, 성형 조건설정 등 다양한 환경의 영향을 받는다. 사출의 주요공정조건으로는 온도, 속도, 압력, 위치, 시간 등이 있으며 실린더온도, 금형온도, 사출속도, 스크류 RPM, 사출압력, 보압, 배압, 공급위치, 절환위치, Cushion위치, 사출시간, 보압시간, 냉각시간 등 매우 다양한 변수들을 측정한다. 따라서 불량을 최소화하고 최적화된 생산을 하기 위해서는 꾸준한 공정관리와 품질분석이 필요하다[1].
기계학습의 발전에 따라 사출성형에서도 품질예측[1-4], 불량원인분석[5], 공정최적화[6-10], 공정상태진단[11-13], 최적설계[14] 등에 활용하는 경우가 점점 늘어나고 있다.
그러나 현장에서 제조를 담당하는 관리자나 작업자들이 일일이 매 사출 사이클이나 일간단위로 추적하고 불량이 생겼을 때 빠르게 분석하는 것은 매우 어려운 일이다. 데이터 분석기법과 관련된 전문적인 지식이나 도구, 서비스, 시스템이 필요한 경우가 많은데 현업에서 이를 모두 갖추고 대응하는 것은 어려운 일이고 검증되지 않은 경우가 많기에 검증과정을 거치는 것 또한 오래 걸리는 경우가 많다. 좀 더 정밀한 분석을 위해서 공정측면에서는 유한요소해석이나 CAE(Computer-Aided Engineering) 등 해석에 기반한 분석을 통해 의미있는 결과를 내는 경우도 있지만, 본 연구에서는 생산제조라인의 현업수준에서 좀 더 빠른 시간에 간단한 분석을 하는 지원방법이 필요한 경우에 초점을 두었다.
본 연구에서는 플라스틱으로 성형된 휴대폰 케이스 제조과정에서 불량이 빈번했던 사출기의 생산데이터를 토대로 연관규칙분석 기반의 단변량 분석을 통한 불량 원인 분석을 수행하였다. 모든 공정변수를 여러 개의 구간으로 나눈 뒤 각 공정변수와 구간에 대한 연관규칙 기반의 불량지수를 제시하였다. 그 결과 각 변수와 구간 별로 불량과의 인과관계를 쉽게 유추할 수 있으며 이를 순위로 나타내어 불량에 대한 높은 영향력을 가지는 변수를 선별할 수 있게 되었다. 또한 각 변수별로 양품과 불량지수를 같이 표시하여 불량과 관계가 높은 변수구간의 시각화를 그래프로 같이 제공한다. 본 연구에서 제안하는 방법은 다변량분석 기반의 모델들처럼 복잡한 이해 및 학습 과정이 필요하지 않으며, 따라서 빠르고 직관적인 분석을 제공하는 것이 가능하다. 또한 이를 대시보드화하여 현장의 작업자들에게 제공함으로써 해석기법과 같은 공정상 고도화분석을 수행하기 위한 사전 지식을 제공할 수 있게 되었다.
2. 본 론
2.1 불량원인 분석 프로세스 개요
본 연구의 전체 개요는 Fig. 1과 같다. 설비나 시스템으로부터 데이터를 수집하고 이를 전처리화하여 데이터셋으로 만든다. 그리고 이 데이터 내 개별 변수들을 일정한 구간으로 좀 더 상세하게 세분화한다. 구간화된 변수들을 본 연구에서 제시한 연관규칙 기반의 지수들을 포함한 다양한 지표들을 개발하여 계산하고 이를 수치화한다. 이렇게 개별 변수들의 구간별로 수치화된 지수들을 전체적으로 데이터화한 다음 실제 작업자들이 필요한 지표 및 변수들에 따라서 요약표로 도출해주거나 지수별 우선순위에 따라서 가시화한 결과를 보여주는 방법에 따르고 있다.
2.2 생산 및 불량데이터 수집
본 연구에 쓰인 데이터는 핸드폰 케이스 사출업체의 사출설비의 하루 생산 데이터를 인터페이스 받고 불량여부는 해당업체에서 표시하여 추가해주었다.
사출기 데이터는 Table 1과 같이 사출 생산순서(Process Number), 공정시간(Injection Time, Measuring Time, Process Time, Form Close Time), 사출속도와 관련된 정보(Max Injection Speed, Max Screw Speed, Avg Screw Speed), 사출압력과 관련된 정보(Max Injection Pressure, Switch Over Pressure, Max Back Pressure, Average Back Pressure), 사출온도와 관련된 정보(Oil Temperature, Hopper Temperature, Long Nozzle Temperature, Nozzle Temperature, Heater 1~4), 공정 내 용융수지 및 장비위치/지점과 관련된 정보(Cusion Location, Switch Over Location, Measuring Complete Location, Form Open Location), 불량여부(Faulty)를 포함한 1997개의 데이터를 수집하였다.
Faulty 변수분포를 통해 집계된 전체 데이터의 불량률은 약 4.86% = (97/1997)이다.
2.3 사출기 기초데이터 분석
주어진 데이터를 통해서 데이터의 모든 변수 별 상관관계를 Fig. 2와 같이 간략히 표시하였다. Fig. 2(a)와 같이 전체 변수를 Scatter Matrix 및 Heatmap형태로 표현해서 Scatter Plot, Density Plot, Correlation을 가시화해서 볼 수도 있지만 이는 변수의 개수가 적거나 주요 변수들을 어느 정도 알고 있다는 가정 하에서만 가능하다. 변수가 매우 많은 경우에는 이러한 형태의 시스템을 구현을 했을 때 작업자들이 어떤 변수를 어떻게 표현을 할 것이냐와 같은 다양한 선택의 문제들로부터 자유롭지 못하다. 그래서 Fig. 2(b)와 같이 우선 상관관계 값 기준으로 0.5가 넘는 값만 요약하여 우선적으로 파악을 하였다. 각 상관관계는 절대값이 0.5 이상인 숫자만 표시하였으며 양수는 푸른색, 음수는 연두색으로 표시하였고 1에 가까울수록 색을 진하게 표시하였다.
변수별 상관관계를 토대로 분석을 하였을 때 주어진 변수 중에서는 단순히 불량여부(가장 우측과 하단 Faulty 변수)와 상관관계가 직접적으로 큰 변수는 없는 것을 확인할 수 있다. 각 변수간의 관계를 파악해보면 대부분 시간, 속도, 압력 등 설비 내 공정관계에서 물리적으로 어느 정도 연관이 있기 때문에 상관관계 자체는 높게 나오는 것을 확인할 수 있다. 그러나 이들이 불량과 어떤 관계가 있는지 상세하게 파악하는 것은 어렵기 때문에 일반적으로 Fig. 3 및 Fig. 4와 같은 개별 변수별 빈도분석과 분포도가 주로 사용된다.
일반적으로 근래 제조업에서는 불량률이 그리 높지 않은 편이고 대기업으로 갈수록 불량률이 매우 낮기 때문에 불량과 관련된 분류문제는 전형적인 클래스 불균형문제에 속한다. 그래서 양품과 불량을 변수에 대한 히스토그램으로 한꺼번에 표시하면 두 발생빈도 차이는 매우 크기 때문에 가시화가 되지 않아 히스토그램을 Fig. 3와 같이 따로 표현해야하는 불편함이 있다. 다변량 분석의 경우도 마찬가지로 변수들을 묶어서 분포를 표현해도 Fig. 4와 같이 불량과 양품이 명확히 구분이 되지 않는 경우가 많다. 따라서 본 연구는 Fig. 4와 같이 불량과 양품을 완전히 분리할 수 있는 변수가 없을 수 있다고 가정하고 진행하였다.
2.4 연관규칙 기반 공정변수구간의 불량연관지수 개발
본 연구에서는 불량원인분석을 위해서 개별 공정변수가 품질에 어떤 형향을 미치는지 지수화 하는 방법을 제시하고 이를 기반으로 분석하였다. 제시된 지수는 공정변수를 일정한 구간으로 나누고 각 구간들과 불량간의 관계를 연관규칙분석 기반으로 정의하는 방법을 사용하였다.
일반적으로 연관규칙분석에서는 Support (지지도), Confidence (신뢰도), Lift (향상도)와 같은 지표를 많이 사용한다. 각각 지표에 대해서 간략히 살펴보면 아래와 같다.
- Suppport = s(X→Y) = n(X ∩ Y) / N
: 전체 빈도에서 X와 Y를 함께 포함하는 비율을 의미
- Confidence = c(X→Y) = n(X ∩ Y) / n(X)
: 항목집합 X를 포함하는 거래 중에서 항목집합 Y도 포함하는 거래 비율(조건부 확률)을 의미
- Lift = Lift(X, Y) = c(X→Y) / s(Y)
: 항목집합 X가 주어지지 않았을 때의 항목집합 Y의 확률 대비 항목집합 X가 주어졌을 때 항목집합 Y의 확률 증가 비율을 의미
이러한 지표와 규칙을 통해서 설명가능하고 실행가능한 규칙을 찾는 것이 일반적인 연관규칙분석의 목적이다. 특히 근래에 많은 연구들에서 중점을 두고있는 부분이 설명가능하고 제어가능한 변수를 찾아서 불량원인에 대한 규명을 하거나 현상을 발견하고 다시 제어나 통제를 하는 것이다.
각 지표들 중에서 불량과 관련된 설명을 위해서 본 연구에서는 Lift를 중점적으로 다룰 것이다. 그 이유는 Lift(X, Y)가 1이면 X와 Y가 독립을 의미하며, 1보다 크면 양의 관계가 높고, 1보다 작다면 음의 관계가 높아서 독립적인 관계 아닐 확률이 높은 것을 의미하기 때문이다.
이를 불량과 공정변수를 연결하기 위해서 각 지표의 의미를 불량구간과 연결하여
- 불량 Support = 구간 내 불량 개수/전체 데이터 개수
- 불량 Confidence = (구간 내 불량 개수/전체 데이터 개수) / (구간 내 데이터 개수/전체 데이터 개수) = 구간 내 불량 개수/구간 내 데이터 개수
- 불량 Lift = (구간 내 불량개수 / 구간 내 데이터 개수) / (전체 불량개수 / 전체 데이터 개수)
와 같이 정의하여 사용하였다. 예를 들어서 불량이 10개, 양품이 100개 있고 이를 구간 3개로 나누었다고 가정했을 때,
- 구간 A: 불량 5개, 양품 50개인 경우, 불량 Support = 5/110 = 0.05, 불량 Confidence = 5/55 = 0.09, 불량 Lift = 5/55 / 10/110 = 1.00
- 구간 B: 불량 1개, 양품 30개인 경우, 불량 Support = 1/110 = 0.01, 불량 Confidence = 1/31 = 0.03, 불량 Lift = 1/31 / 10/110 = 0.35
- 구간 C: 불량 4개, 양품 20개인 경우, 불량 Support = 4/110 = 0.03, 불량 Confidence = 4/24 = 0.17, 불량 Lift = 4/24 / 10/110 = 1.83
와 같이 표현할 수 있다. 각 구간을 살펴보았을 때 구간 A에서 발생하는 불량이 전체불량률(10/110)과 거의 비슷해서 변수 A 구간이 불량발생과 인과관계가 독립적이라고 볼 수 있으며 마찬가지로 B 구간의 경우에도 Lift가 0.35로 해당 구간이 불량발생에 대한 인과관계가 거의 없음을 확인할 수 있다. 그러나 구간 C의 경우 발생하는 불량인 Lift값이 1.83으로 훨씬 높다는 것을 확인할 수 있기 때문에 구간 C를 확인해보는 것이 불량원인분석에 도움이 될 수 있음을 확인할 수 있다. 이러한 지표를 그림으로 표현해보면 Fig. 5와 같다. Fig. 5에서는 데이터를 변수별로 구간을 나누고, 각 구간별로 양품과 불량에 대해서 지수화하여 동일한 밀도에서 표시될 수 있도록 분석 및 시각화하였다. 단순히 변수를 불량빈도 기준으로 분포를 그리는 것이 아니라 구간별로 불량발생이 높게 일어나는지 낮게 일어나는지 데이터 분석에 능숙하지 않은 작업자들도 쉽게 이해할 수 있게 시각화를 할 수 있는 장점이 있다. 이 그림은 지수들의 가시화를 위해서 밀도를 예시로 설명했지만 다른 방법으로도 변수와 구간에 대해서 가시화하는 것이 가능하며 가시화를 통해서 전체 불량발생 빈도보다 특정한 구간의 불량발생 빈도가 높은 구간을 찾아 원인분석의 단서를 제공하거나 직접적인 원인을 설명하는데 지수를 통해 수치적인 설명과 가시화를 함께 제공할 수 있다.
3. 실 험
3.1 실험데이터 수집 및 전처리
제안된 기법을 통한 실제 데이터 분석을 위해서 국내 가장 큰 핸드폰 케이스를 생산하는 한 개의 업체에서 사출기 1대의 1일치 생산데이터를 제공받았고, 수작업과 검증을 통해 불량여부 레이블이 추가된 생산데이터셋이 완성되었다. 분석 및 실험예시는 완성된 데이터셋을 활용하였고 개발 및 실험환경은 Intel i7–4790k 프로세서 및 16 GB 메모리사양에서 Jupyter Notebook / Python 3.6으로 진행하였다.
수집된 데이터는 결측치, 오류 등을 이미 수행해놓은 데이터로 본 연구에서는 해당 데이터를 각 변수별로 임의로 구간 10개로 나누고 지표를 계산하여 진행하였다. 그리고 공정변수 중에서 일부 변수는 이산변수로 값의 종류가 10개가 되지 않는 변수가 존재해서 해당변수들은 이산값의 개수에 따라 구간을 10개 이하로 나누었다.
이렇게 변수들을 구간들로 나누었고 각 구간 별 불량 Lift 기준 상위 구간들 Table 2와 같이 변수, 변수 내 전체구간의 수, 해당 구간의 순서, 해당 구간의 공정변수 값 범위, 불량 Support, 불량 Confidence, 불량 Lift, 양품 Lift, 양품개수, 불량개수, 총개수로 표시하였다.
3.2 실험결과
실험데이터 기준으로 불량 Lift가 높은 주요 변수로는 Injection Time, Measuring Time, Process Time, Max Screw Speed, Average Screw Speed, Max Injection Pressure, Switch over Pressure, Average Back Pressure, Oil Temperature, Hopper Temperature, Heater 1, Heater 2가 있었고 이 변수들 중에서 특정구간이 전체평균 불량률보다 약 1.5~3.5배까지 높은 것을 확인할 수 있다. 예를 들어서 Injection Time이 3.93 ~ 3.95인 구간은 Injection Time 전체 10개 구간 중에서 2번째 구간에 해당하며 이 구간에서의 불량 Lift 값은 1.95로 전체불량률 약 5%보다 2배 가까이 높음을 의미하다. 특히 Switch over Pressure는 70.0 이상인 구간에서 불량Lift가 3.55로 불량률이 전체 불량률 대비 3.5배까지도 높은 것을 쉽게 확인할 수 있다. 단순히 Switch over Pressure가 불량인자가 될 수 있다는 것을 설명하는 것만이 아니라 그 공정값이 70.0 이상인 구간에서 양품 대비 불량이 매우 많이 유발하는 것을 확인하여 불량인자와 공정수준에 의한 불량을 한번에 설명하고 있다.
그리고 지수 중에서 불량 Support의 순위는 Lift 순위와 비례하지 않음을 알 수 있다. 불량 Confidence를 확인해보면 문제는 본 문제에서 구간과 데이터의 크기가 그리 크지 않아서 괜찮은 지표로 보이지만, 데이터의 크기에 따라서 단위가 변하기 때문에 설명이나 가시화를 위해서는 데이터의 크기가 커지거나 작아지는 것에 따라 보정을 해줘야 하는 문제가 발생한다. 따라서 불량 Support와 불량 Confidence는 불량 Lift를 계산하기 위해서 필요한 지표이고 실제 불량과 연관시켜 가장 표시하고 설명력있는 지표로 사용하기 위해서는 불량 Lift를 보는 것이 중요하다.
불량 Lift값에 의한 좀 더 상세한 가시화를 위해서 불량 Lift가 높은 몇 개 변수들에 대해서 히스토그램과 밀도분포를 그려보았다. Table 3과 Fig. 6를 보면 Switch over Pressure 공정변수의 양품과 불량의 커널밀도추정과 히스토그램을 표시하고 있다. 그리고 세로선으로 구간별 분할된 구간을 표시하였으며 Switch over Pressure의 경우 총 4개의 구간으로 나뉜 것을 확인할 수 있다. 4개의 구간 중에서 불량 Lift가 3.55로 가장 큰 구간을 붉은색 구간으로 표시하였다. 이러한 방법으로 불량 Lift가 높은 다른 변수들에 대해서도 가시화를 할 수 있을 것이다.
반면 Table 4와 Fig. 7과 같이 불량 Lift가 높지 않은 변수들에 대해서도 살펴보면 단순히 불량빈도가 높다고 해서 무조건 분석이 중요한 구간은 아니라는 것을 확인할 수 있다. 예를 들어서 Max Back Pressure 변수를 확인했을 때 가장 불량이 많이 일어나는 구간은 22.4 ~ 22.8로 앞서 불량 Lift가 3.55로 가장 높았던 Switch over Pressure의 70.0 이상인 구간보다 불량 개수는 2배로 넘지만 불량 Lift는 1.158로 불량과의 연관이 약하게 있어 중요도가 상대적으로 낮음을 표시하고 있다.
그리고 상세한 가시화 그림에서 사용하고 있는 커널밀도를 통해서 불량과 양품이 서로 다른 분포를 보이고 있음을 확인할 수 있지만 정확히 어떤 구간에서 어느 정도의 불량을 유발하는지 구체적으로 설명해주고 있지는 않다. 따라서 본 연구에서 제시하는 것처럼 구간을 나누고 불량 Lift값에 의해서 좀 더 상세하고 정량한다면 의사결정에 도움을 줄 수 있을 것이다.
각 변수별 가시화를 종합해서 Fig. 8과 같이 살펴보면 전체적으로 사출압력이 높고 그로 인해 사출속도가 빠르고 사출시간이 짧았을 것이며 이는 품질관리나 공정설계 측면에서는 허용된 기준치를 넘지 않았지만 실제로는 불량을 유발하는 원인 중에 하나였을 것이라 생각할 수 있다. 따라서 설계상 공정관리도에서 문제가 없었다고 하더라도 생산라인에서는 공정관리도를 조정하는 것이 필요하다는 것을 확인할 수 있다. 그리고 이를 간단한 분석과 지표의 활용을 통한 대시보드화를 통해 데이터분석에 익숙하지 않은 작업자들도 충분히 활용할 수 있는 기초를 마련할 수 있었다.
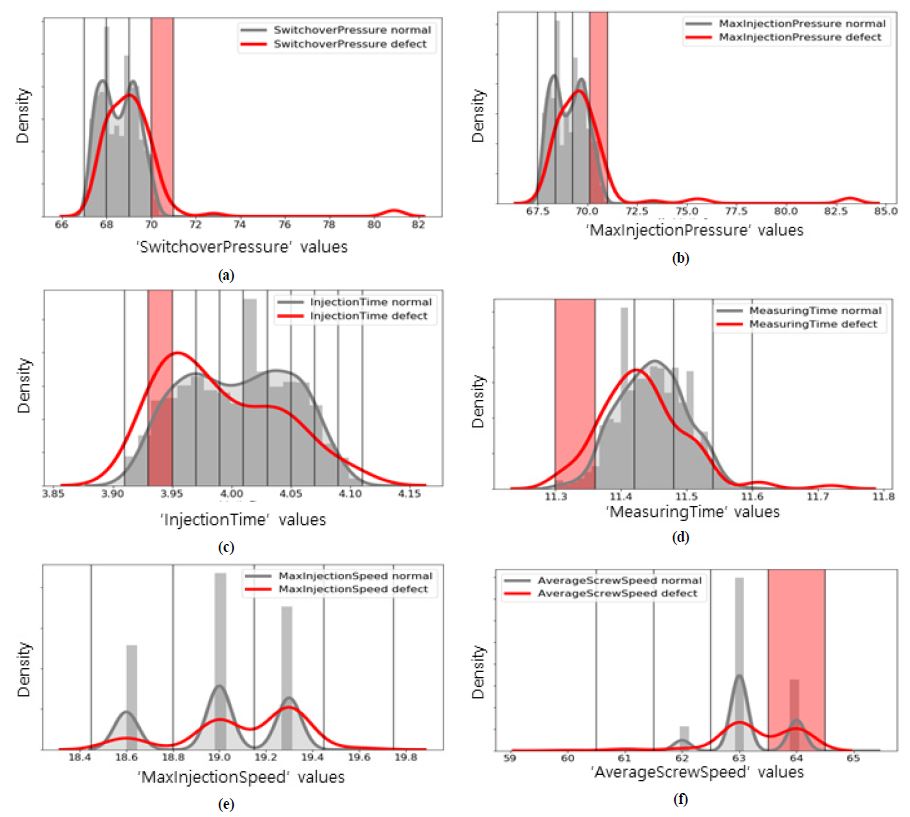
Density Plots of Partitioned Process Variables (a) ‘SwitchoverPressure’, (b) ‘MaxInjectionPressure’, (c) ‘InjectionTime’, (d) ‘Measuring Time’, (e) ‘MaxInjectionSpeed’, (f) ‘AverageScrewSpeed’
또한 제공받은 데이터에서는 불량유형이 주어지지 않았지만 이 방법을 불량유형에 따라 분석하고 가시화할 수 있다. 불량 Lift가 높은 변수 중에서 사출시간, 사출시간, 사출압력과 별개로 Hopper Temperature, Heater 1, Heater 2, Oil Temperature 변수들도 존재한다. 제공받은 불량유형과 관련한 데이터나 상세한 금형온도와 같은 데이터가 충분하지 않아서 온도와 관련된 분석은 불가능했지만 이러한 데이터와 변수들도 추가된다면 좀 더 상세한 분석도 충분히 가능하다.
4. 결 론
본 연구에서는 핸드폰케이스의 사출성형의 불량원인분석 문제에 대해서 연관관계규칙 기반의 지수를 토대로 불량원인분석을 수행하고 이를 가시화 및 해석할 수 있는 방법을 보였다. 이를 위해 사출성형기로부터 수집된 공정변수를 구간별로 분할하고 연관규칙에 기반한 다양한 지수 중 불량 Lift를 활용하였다. 불량 Lift를 포함한 다양한 지수들은 공정변수의 각 구간이 불량과 어떠한 관계가 있는지 수치적으로 나타낼 수 있기 때문에 이를 활용하여 변수들 중에서 어떤 변수의 어떤 구간이 불량과 연관관계가 큰지 간단한 방법으로 분석하고 가시화 할 수 있다.
최근 인공지능 및 기계학습 관련 기술들의 발전으로 제조현장에서도 다양한 불량원인분석을 수행하고 있지만 많은 연구들이 결과들에 대한 해석이 어려운 모델을 사용하거나 해석을 위해서 데이터분석 전문가가 필요한 경우가 많다.
그에 반해 본 연구에서 사용한 지수기반의 방법론과 시각화 그래프들은 이를 시스템화하고 대시보드 개발을 통해 데이터 분석에 익숙하지 않은 현장의 작업자들과 엔지니어들도 간단한 방법으로 불량원인분석에 기초가 되는 데이터를 파악하고 직관적인 해석이 가능하며 이들이 직접 구간에 대한 조정을 통해 세밀한 분석과 데이터에 대한 통찰을 해보는 것이 가능하다.
비록 본 연구에서 활용된 데이터는 불량여부를 이진변수로 변환된 데이터였기에 분석의 결과가 단편적이지만 상세한 불량종류의 표시가 가능하다면 좀 더 고도화된 불량원인분석과 가시화도 가능할 것이다.
본 연구결과를 바탕으로 해당기업에서는 생산 속도를 과도하게 높이고자 공정 변수를 설정하면 불량이 많이 발생한다는 것을 확인했고, 해당 연구의 피드백을 받고 공정 조건 중 스크류 속도 및 압력의 한계치에 대한 관리도 수준을 이전의 설정보다는 낮게 조정하고 있다.
Acknowledgments
This study has been conducted with the support of the Korea Institute of Industrial Technology as “Machinability diagnosis and control system based on deep learning for self-optimized manufacturing system (KITECH EO-19-0430)” and work was supported by the Industrial Strategic Technology Development Program (20004537, Development of Manufacturing Big Data Collection and Analytics General Purpose Platform) funded By the Ministry of Trade, Industry & Energy (MOTIE, Korea).
References
-
Chen, W.-C., Tai, P.-H., Wang, M.-W., Deng, W.-J., Chen, C.-T., 2008, A Neural Network-based Approach for Dynamic Quality Prediction in a Plastic Injection Molding Process, Expert Systems with Applications, 35:3 843-849.
[https://doi.org/10.1016/j.eswa.2007.07.037]
-
Li, E., Jia, L., Yu, J., 2002, A Genetic Neural Fuzzy System-based Quality Prediction Model for Injection Process, Computers & Chemical Engineering, 26:9 1253-1263.
[https://doi.org/10.1016/S0098-1354(02)00092-3]
- Min, B.-H., 1999, Quality Prediction of Injection Molded Part by Neural Network, Proceedings of KSPE 1999 spring conference., 1-4.
- Lee, K. H., Lee, Y. H., 2011, Rule Extraction to Predict Quality of Injection Molding Process using Decision Tree, Proceedings of the Korean Society for Precision Engineering 2011 Autumn Conference., 1-2.
- Kang, S. N., Huh, Y. J., Cho, H. C., 2002, A Study on the Application of Fuzzy Neural Network for Troubleshooting of Injection Molding Problems, Journal of the Korean Society of Precision Engineering, 19:11 83-88.
-
Kenig, S., Ben, D. A., Omer, M., Sadeh, A., 2001, Control of Properties in Injection Molding by Neural Networks, Engineering Applications of Artificial Intelligence, 14:6 819-823.
[https://doi.org/10.1016/S0952-1976(02)00006-4]
- Baek, J. Y., Kim, B. H., Lee, G. B., 2005, A Searching Method of Optimal Injection Molding Condition using Neural Network and Genetic Algorithm, Proceedings of the Korean Society for Precision Engineering 2005 Autumn Conference., 1-4.
- Ryu, K., Liau, Y. Y., Lee, H., 2018, Search for an Optimal Combination of Process Parameters in Injection Molding based on ANN, Proceedings of The Korean Institute of Industrial Engineers 2018 Spring Conference., 1-8.
-
Lo, W. C., Tsai, K. M., Hsieh, C. Y., 2009, Six Sigma Approach to Improve Surface Precision of Optical Lenses in the Injection-Molding Process, The International Journal of Advanced Manufacturing Technology, 41 885-896.
[https://doi.org/10.1007/s00170-008-1543-0]
-
Rhee, B. O., Tae, J. S., Choi, J. H., 2009, Injection Molding Cooling Circuit Optimization by Back-Propagation Algorithm, Journal of the Korean Society of Machine Tool Engineers, 18:4 430-435.
[https://doi.org/10.7736/KSPE.2014.31.11.1031]
-
Baek, D. S., Nam, J., Lee, S. W., 2014, A Development of Feature Extraction and Condition Diagnosis Algorithm for Lens Injection Molding Process, Journal of the Korean Society of Precision Engineering, 31:11 1031-1040.
[https://doi.org/10.7736/KSPE.2014.31.11.1031]
-
Ribeiro, B., 2005, Support Vector Machines for Quality Monitoring in a Plastic Injection Molding Process, IEEE Transactions on Systems Man and Cybernetics Part C., 35:3 401-410.
[https://doi.org/10.1109/TSMCC.2004.843228]
- Koh, B.-W., Kim, J.-S., Choi, H.-G., 2008, Estimation of Process Parameters Using QFD and Neural Networks in Injection Molding, IE Interfaces., 21:2 221-228.
- Park, K., Ahn, J. H., Choi, S. R., 2001, Optimal Design for Injection Molding Processes using Design of Experiments and Finite Element Analysis, Proceedings of the Korean Society for Technology of Plasticity Conference., 1-4.