
선택적 레이저 용융방식 고분자 적층제조공정 시 적층조건에 따른 용융 풀 및 형상 재현성 변화에 관한 연구
Abstract
This study aims at securing the shape reproducibility of the final product manufactured using additive manufacturing. Accordingly, the width and depth of the melt pool were quantified by energy density according to the laser power and scan speed using scanning electron microscope analysis. The laser power and scan speed ranges were 5-50 W and 800-5800 mm/s, respectively. The minimum energy density and laser power for the output were 0.06 J/mm3 and 5 W, respectively. The optimal process condition within the tolerance range of the specimen was confirmed to be the energy density range of 0.24-0.35 J/mm3. For an energy density of 1.0 J/mm3 or higher, the melting point of the material is higher, and thermal flow convection occurs, resulting in a large expansion of the final product. This study confirmed the effect of the melt pool on the final product in a selective laser melting system.
Keywords:
Selective laser melting (SLM), Thermal fluid convection, Shape reproducibility, Melt pool, Polymer1. 서 론
최근 적층제조 기술은 맞춤형 제품 생산과 다품종 소량 생산 분야를 중심으로 수요가 꾸준히 증대하고 있으며 의료, 항공/우주 및 발전 분야 등 고부가가치 산업분야에서는 활발한 실용화도 진행되고 있다[1-2]. 대부분 금속 소재를 기반으로 하는 적층제조 기술들로 산업의 많은 부분을 차지하는 고분자 소재는 재료의 융점, 휘발성, 점성 등 고려해야하는 특성들이 많고 압출, 브로우 성형 등 기존 제조 방식 대비 경제적 측면, 기계적 측면에서의 격차[3]들로 인해 관련 연구가 미비한 실정이다. 하지만 고분자 소재의 활용 범위가 넓고 기존 제조 기술로 구현이 어려운 다양한 형태 제작이 가능하여 산업계에서의 요구는 지속적으로 증가하고 있는 추세이다.
본 연구는 고분자 소재의 산업 제품/부품 측면에서 정밀도, 정확도 및 기계적 물성 성능 등 실제 산업 적용에 중요한 요소임에 따라 허용오차 범위 ± 0.5% 이내의 최종품 형상 재현성을 갖는 적층제조공정 파라미터 데이터 확보를 하고자 하였다. 특히, 용융 풀(melt pool)은 레이저 에너지원의 열적 전도, 대류 및 증발 등[4]으로 소재가 용융되어 형성되는 것으로 레이저의 에너지 밀도에 따라 그 형태는 상이하며, 적층제조품의 형상 품질에 직접적 영향을 주는 요소이다. 파라미터별 용융 풀을 싱글과 멀티 레이어로 적층 제조하여 에너지 밀도에 따른 형상 변화 및 너비(width)와 깊이(depth)[5]를 정량적으로 분석하고 형상 재현성과의 상관관계에 대해 고찰하였다.
2. 실 험
2.1 적층 제조 공정의 용융 풀(melt pool)
본 연구에 활용한 선택적 레이저 용융 방식(selective laser melting)의 레이저 빔 직경은 약 0.5~0.65 mm이며, 열 에너지원인 CO2 레이저(파장 10.6 µm)에 의해 용융되는 과정을 Fig. 1에 나타내었다. 레이저 파워, 스캔스피드 등 파라미터별 상이한 에너지 밀도를 갖는 레이저는 열의 형태로 전달되어 소재를 용융시키며, 이 영역을 용융 풀(melt pool)이라고 한다. 적층 제조는 이 용융 풀이 일정한 간격과 두께로 겹쳐지며 3차원 형상을 형성하는 과정이다. 레이저의 열에너지는 대부분 소재를 용융시키는 에너지로 활용되고 일부는 반사되며, 또 일부는 용융 영역 주변 소재에 영향을 미치는 열 열향부(heat affected zone)로 전도된다. 에너지 밀도별로 용융 풀의 형상을 관찰하고 너비(width)와 깊이(depth) 등을 정량화하고 최종품의 수축률 측정을 통해 형상 재현성에 미치는 영향을 고찰하고자한다.
2.2 파라미터별 용융 풀 및 최종품 제작
본 연구는 70 W CO2 레이저를 사용하는 PBF (powder bed fusion) 방식의 고분자 적층 제조 시스템(EOS社 P396)을 활용하였으며, 소재는 자동차 부품 제조에 주로 활용되는 엔지니어링 플라스틱(Polyamide 12, PA2200)을 사용하였다. 소재의 적층 두께는 120 µm이고 적층 챔버 내 온도는 170℃ 내외이며, 적층 플랫폼 유지 온도는 130℃ 내외로 설정하였다.
적층 공정은 Fig. 2와 같이 일반적으로 contour (red line)와 hatch (green line) 두 부분으로 진행되나, 본 연구에서는 싱글 및 멀티 레이어의 용융 풀 제작을 위해 actual contour (Fig. 2 ①) 조건에서 beam offset 및 hatch 과정 없이 contour만을 수행하여 적층하였다. 파라미터별 형상 재현성을 확인하기 위한 최종품 시편은 10×10×10 mm3의 큐빅 형태로 제작하였고, 파라미터에 따른 contour의 용융 풀이 형상 재현성에 미치는 영향을 확인하기 위해 최종품 시편의 모든 hatch는 레이저 파워 40 W, 스캔스피드 4000 mm/s의 조건으로 제작하였다.
용융 풀과 최종품 제작을 위한 공정 파라미터는 Table 1에 레이저 파워와 스캔스피드에 따른 에너지밀도로 나타내었고 에너지밀도는 (1)에 의해 산출되었다[7].
(1) |
(ED : energy density (J/mm3) / PL : power of laser beam (W, J/s) / dL : thickness of powder layer (mm) / hs : hatch distance during exposure (mm) / Vs : scan speed of the laser beam (mm/s))
파라미터별 제조된 최종품 시편의 형상 재현성은 수축률[8] 측정 (2)를 기준으로 하였으며 양의 값은 수축을 음의 값은 팽창을 의미한다.
(2) |
(Lc : Original CAD model dimension (mm) / Lm : Measured dimension on the specimen (mm))
2.3 시편 측정 및 분석
적층 제조된 싱글 및 멀티 레이어 용융 풀은 전계방출형 주사전자현미경(FE-SEM, FEI社 Quanta 250)을 활용해 너비와 깊이를 측정하였다. 싱글 레이어 용융 풀의 깊이 측정은 콜드 마운팅 후 샌드페이퍼와 융을 활용해 연마하였으며, 멀티 레이어 용융 풀 시편의 경우 연마 열에 의한 시편 훼손을 방지하기 위해 액체 질소를 이용해 파단면을 관찰하였다. 최종품 시편은 각 파라미터별 3개씩 제작하였으며, 디지털 버니어캘리퍼스(Mitutoyo社)를 이용하여 적층 방향의 수직방향(X, Y축)과 적층 방향(Z축)을 측정하였고, 측정된 값의 평균값과 표준편차를 도출하였다. 또한 최종품 시편의 첨단부 관찰을 위해 디지털 마이크로스코프(Keyence社 VHX-5000)활용하였다.
3. 본 론
3.1 파라미터별 용융 풀 형상 분석 결과
Fig. 3은 SEM 분석을 통해 파라미터별 싱글 레이어 용융 풀의 너비(a)와 깊이(a) 방향별 에너지 전달경로를 나타낸 것이다. 너비 방향으로의 용융 풀 형태는 Fig. 3(a)와 같이 레이저 빔 스캔경로 중앙부(red part)로 소재가 용융된 영역을 확인하였고, 이 용융된 영역 주위로 분말형태 소재가 붙어 있는 영역이 확인(yellow line)되었다. 깊이방향으로의 용융 풀 형태는 Fig. 3(b)와 같았으며 레이저가 지나간 영역(green line)으로 소재가 완전 용융되어 아래로 녹아내린 오목한 형태(red line)를 확인할 수 있었고, 그 주변으로 용융되지 못한 영역(yellow line)이 관찰되었다. Fig. 3(a)와 (b)의 용융되지 못한 영역(yellow line)은 열 영향부로 판단되고, 이는 레이저의 열에너지가 소재에 닿는 중앙부부터 멀어질수록 에너지를 잃게 되면서 열 영향부에서의 온도는 소재의 녹는점보다 낮아지게 되어 소재가 완전 용융되지 못한 채 서로 엉겨 붙어진 형태가 된 것으로 사료된다.
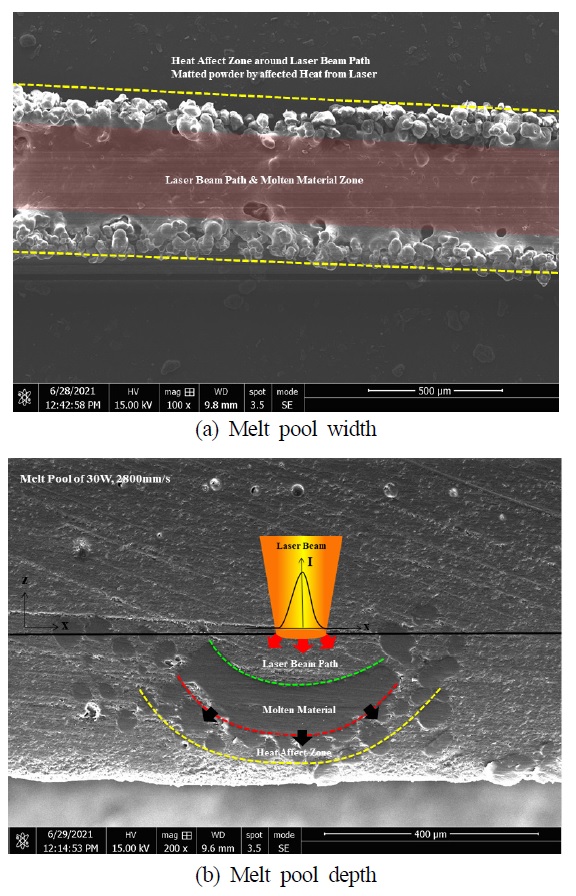
Schematic view of the laser beam path of the single layer melt pool width (a) and depth (b) by SEM images
Fig. 4는 전체 파라미터별 용융 풀의 너비(a)와 깊이(b)를 SEM 분석을 통해 비교한 이미지이다. 레이저 빔의 직경이 0.5 mm ~ 0.65 mm으로 일정할 때, 레이저 파워가 높아질수록 용융 풀의 너비는 넓어지고, 깊이는 깊어지는 것을 확인하였다. 반면, 스캔스피드가 증가할수록 너비는 좁아지고 깊이는 얕아지는 것이 관찰되었다.
파라미터별 에너지 밀도를 나타낸 Table 1에서 레이저 파워 5 W 영역의 에너지 밀도 0.1 J/mm3 이하의 조건과 레이저 파워 10 W 영역의 에너지 밀도 0.05 J/mm3에서 소재의 완전 용융이 발생되지 않음에 따라 용융 풀 확인이 어려운 것을 Fig. 4를 통해 확인하였다.
이를 통해 용융 풀 확인이 가능한 최소 에너지 밀도가 0.06 J/mm3이라는 것을 확인 하였다. 하지만 최소 출력 에너지 밀도 0.06 J/mm3보다 높은 에너지 밀도 0.08 J/mm3를 갖는 5 W-1800 mm/s에서는 적층이 되지 않음에 따라 적층이 가능한 최소 레이저 파워가 5 W 이상이라는 것을 확인하였다.
Table 2와 Fig. 5는 동일 에너지 밀도 0.15 J/mm3(a)와 0.29 J/mm3(b)를 갖는 각각의 파라미터 조건 10 W-1800 mm/s와 20 W-3800 mm/s 그리고 40 W-3800 mm/s와 50 W-4800 mm/s에서의 용융 풀의 너비와 깊이를 비교한 결과이다. 에너지 밀도 식(1)의 해칭 간격과 레이어 두께가 일정할 때, (3)과 같이 에너지 밀도는 레이저 파워에 비례하고 스캔스피드에 반비례한다.
(3) |

Result of width and depth length of melt pool with same energy density of 0.15 J/mm3, 0.29 J/mm3(Unit: μm)
동일 에너지 밀도 조건을 갖기 위해서는 레이저 파워가 증가하면 스캔스피드도 함께 증가해야 한다. Fig. 4에 따르면 레이저 파워의 증가는 용융 풀의 너비와 깊이의 증가를, 스캔스피드의 증가는 용융 풀의 너비와 깊이의 감소의 결과를 확인하였다. 하지만 Table 2와 같이 동일 에너지 밀도 조건에서는 레이저 파워와 스캔스피드가 동시에 증가하게 될 경우의 용융 풀의 너비와 깊이를 확인한 결과 너비는 감소하고 깊이는 증가함에 따라 레이저 파워는 용융 풀의 깊이를, 스캔스피드는 용융 풀의 너비에 영향을 미친다는 것을 확인할 수 있었다.
Fig. 6은 적층 방향(Z축)으로 멀티 레이어 용융 풀의 단면을 확인한 결과이다. Fig. 6(a)와 (b)는 각각 30 W- 2800 mm/s (0.3 J/mm3)와 50 W-5800 mm/s (0.24 J/mm3)에서 출력된 시편으로 멀티 레이어 용융 풀(좌)이 적층 방향으로 쌓인 형태를 확인할 수 있었다. 싱글 레이어 용융 풀(우)와 층간 두께를 비교한 결과 유사한 두께 결과(열 영향부 제외)를 확인할 수 있었다. 또한 에너지 밀도 차이가 큰 Fig. 6(c)와 Fig. 6(d)는 파라미터 조건 5 W-800 mm/s (ED 0.17 J/mm3)와 50 W-800 mm/s (ED 1.74 J/mm3)으로 싱글 레이어의 용융 풀 층을 확인 할 수 없었다. Fig. 6(c)의 에너지 밀도는 소재의 완전 용융시킬 수 있는 온도에 미치지 못해 용융되지 못한 원소재의 형태 그대로의 형상으로 확인 되었고, Fig. 6(d)의 에너지 밀도는 많은 에너지를 넓고 깊은 면적으로 전달되어 이미 용융된 이전 영역까지 영향을 미치며 하나의 큰 덩어리의 형상처럼 된 것을 확인 할 수 있었다.
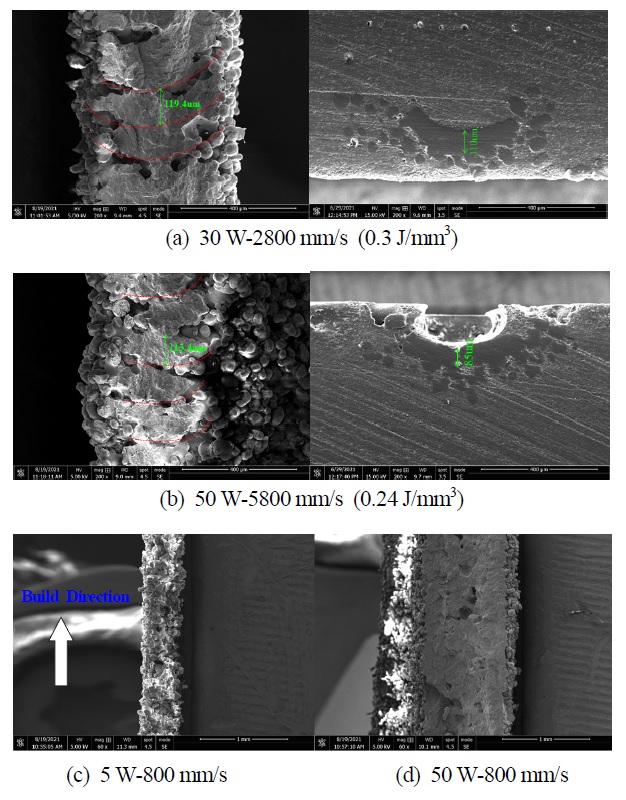
Melt pool SEM image of cross section on printed process of (a) 30 W-2800 mm/s (0.3 J/mm3) and (b) 50 W-5800 mm/s (0.24 J/mm3) with multi layer (left) and single layer (right), and the multi layer of (c) 5 W-800 mm/s and (d) 50 W-800 mm/s
Fig. 7(a)는 스캔스피드 800 mm/s, (b)는 레이저 파워 50 W를 기준으로 할 때의 용융 풀의 너비와 깊이를 에너지 밀도와 비교한 결과이다. 에너지 밀도가 상승할수록 용융 풀의 너비와 깊이가 증가하는 것을 확인 할 수 있었고 Fig. 7 (a)에서 용융 풀의 너비와 깊이의 변화가 레이저 파워 20 W의 에너지 밀도는 0.69 J/mm3조건에서 증가폭이 둔화되는 것을 확인할 수 있었다.
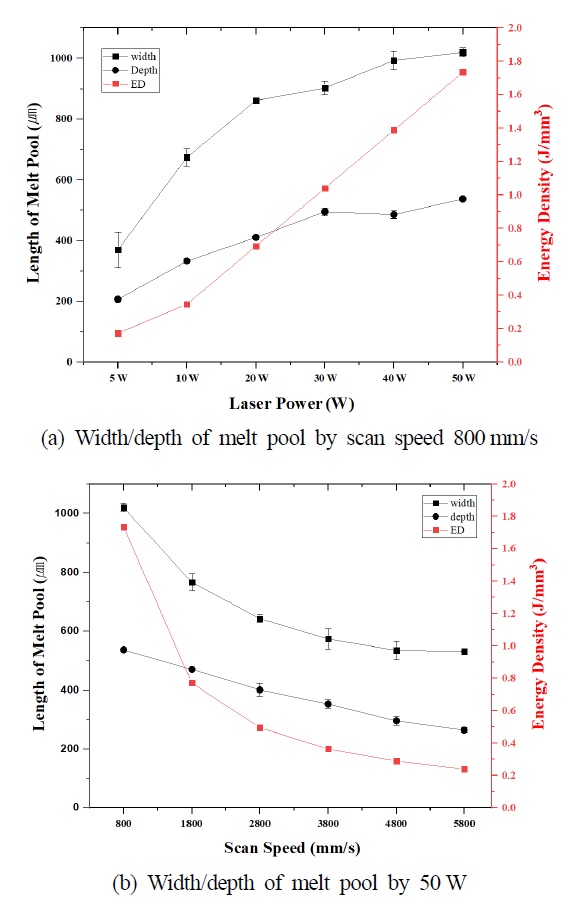
The comparison of energy density by parameter and width/depth of melt pool : (a) scan speed 800 mm/s by laser power and (b) laser power 50 W by scan speed
Fig. 7(b)의 용융 풀의 너비는 에너지 밀도에 비례하여 감소하는 경향을 보였지만, 깊이는 감소하지만 에너지 밀도에 비례하는 이상적인 감소 현상을 보이지 않았다. 이는 스캔스피드 1800 mm/s (0.77 J/mm3)이후에 증가폭이 둔화되는 것으로 사료되며 정확한 둔화 지점을 확인하기 위해 Fig. 8에 에너지 밀도 분포에 따른 용융 풀의 너비와 깊이를 확인해 보았다. 그 결과 너비와 깊이는 모두 에너지 밀도 0.6 J/mm3 이후 완만해 지는 것을 확인하였으며, Fig. 7(a)와 (b)의 둔화 지점 결과와도 유사한 것을 도출하였다.
3.2 Contour 시편의 오차 허용 범위 내 수축률
Fig. 9는 파라미터별 최종품 시편의 첨단부 형상을 광학 현미경을 통해 확인한 결과이다. 에너지 밀도 조건 1.04 J/mm3 이상을 갖는 시편(yellow box)는 첨단부를 잃고 형상 재현성이 저하되는 것을 확인하였고, 에너지 밀도 조건 0.1 J/mm3 이하를 갖는 시편은 층 간 수축 변형으로 층간 박리(red box)되는 것을 확인하였다. Fig. 10은 파라미터별 최종품 시편의 수축률을 적층 방향의 수직 방향(X축)과 적층 방향(Z축)으로 측정한 결과를 나타낸 것이다(이하 적층 방향의 수직 방향은 X축, 적층 방향은 Y축이라함). 최종품 시편의 X축과 Y축은 유사한 수축률을 나타내어 Fig. 10은 X축(a)과 Z축(b)의 결과만을 활용하였다. 최종품 시편의 허용 오차범위(tolerance range) ± 0.5% (기준 시편 10×10×10 mm3, 약 50 um 이하)를 기준으로 수축률이 양의 값이면 수축, 음의 값이면 팽창을 의미한다. 본 연구에서 사용한 수축과 팽창은 공정 중 발생하는 고분자 소재의 변형을 의미하는 것이 아니며 파라미터별 용융 풀의 형상이 최종품의 형상 재현성에 미치는 영향을 확인하기 위한 의미로 활용되었다.
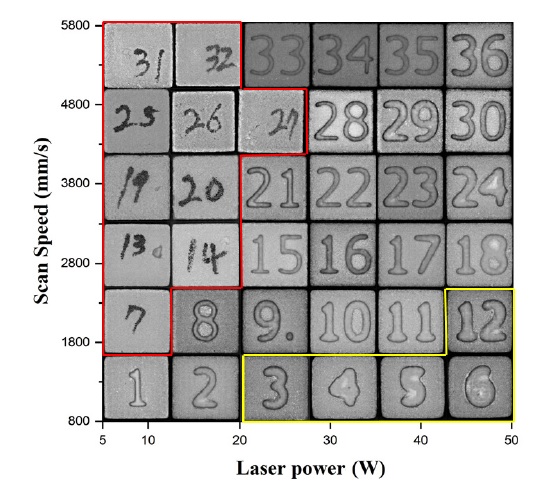
Result of optical microscope of cubic specimens which is printed only contour without hatch by parameter ; laser power from 5 W to 50 W and scan speed from 800 mm/s to 5800 mm/s
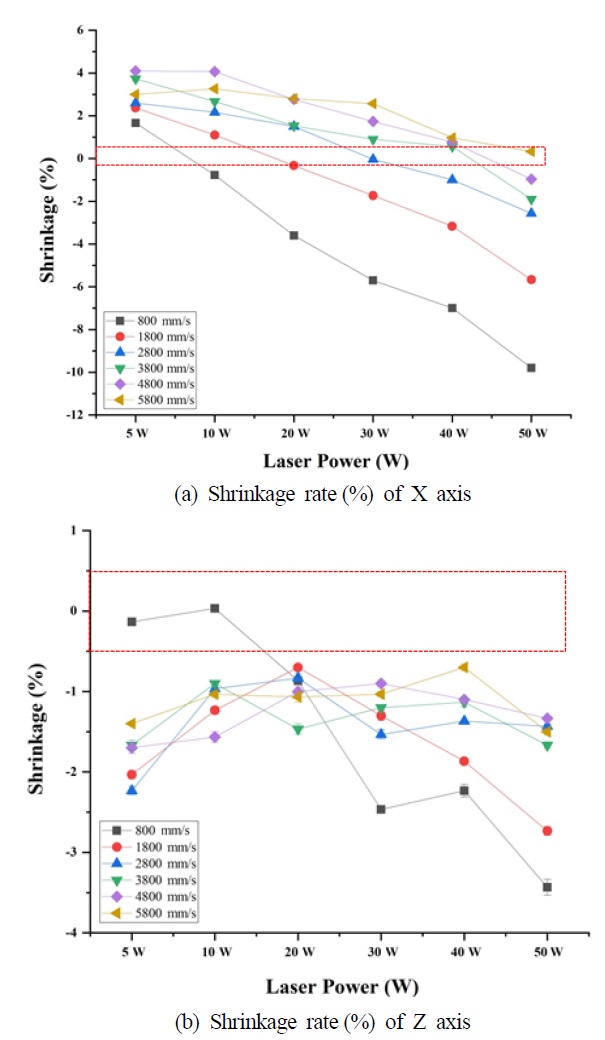
The shrinkage rate (%) of X (a), Z (b) axis which is printed contour by parameter (red box is tolerance range)
Fig. 10(a)의 X축의 수축률 확인 결과 레이저 파워가 높아질수록, 스캔스피드가 느릴수록 팽창 현상이 관찰 되었다. 이는 Fig. 11을 통해 최종품의 수축률에 따른 용융 풀의 너비와 깊이 결과를 통해 확인할 수 있었다. 최종품 시편의 팽창은 에너지 밀도가 커지며 동일한 레이저 빔 크기에서 Fig. 11의 용융 풀의 너비(a)와 깊이(b) 영역이 넓어지고 깊어지는 것에 영향을 받아 팽창된 것을 확인 할 수 있었다. 반면 레이저 파워가 낮을수록, 스캔스피드가 빠를수록 최종품 시편의 수축 현상이 확인 되었는데 이는 Fig. 11에서 용융풀의 너비(a)와 깊이(b) 영역이 좁고 얕아져 최종품의 수축에 영향을 미치는 것을 확인하였다. 결론적으로 X축에서 허용 오차 범위 ± 0.5% 내에 드는 조건은 30 W-2800 mm/s (0.30 J/mm3)이며, 허용 오차범위 근접한 조건은 에너지 밀도 0.24 J/mm3 ~ 0.35 J/mm3 범위가 형상 정밀도에 최적의 조건이라는 것을 도출하였다.
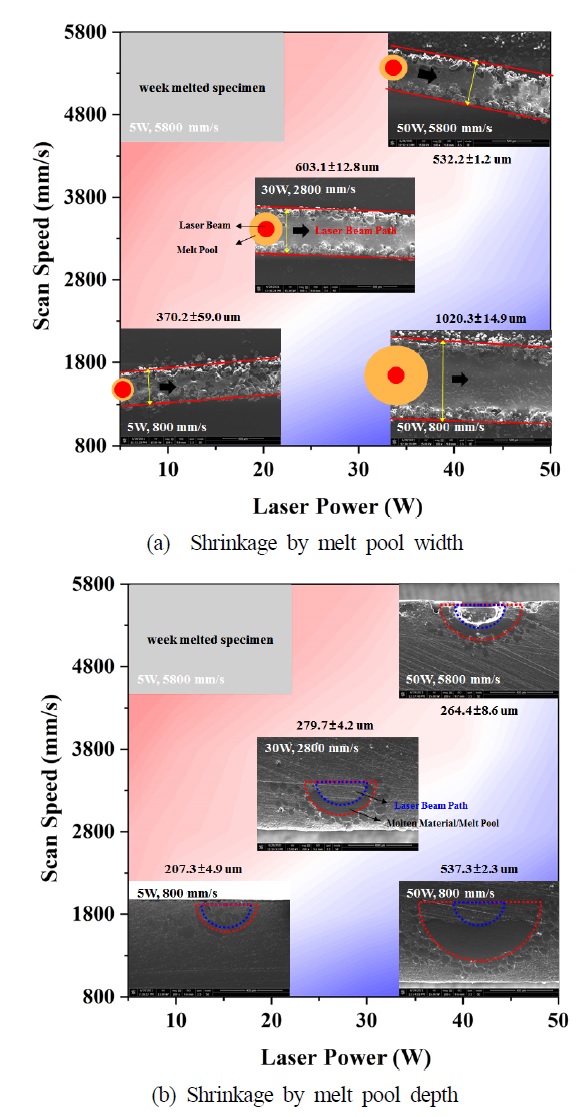
Result of comparison of melt pool width (a) and (b) depth by shrinkage (red) and expansion (blue) of cubic specimen
Fig. 10(b)는 최종품 시편의 적층 방향(Z축)로 수축률을 확인한 결과이며 대부분 허용 오차 범위 밖으로 팽창한 것을 확인할 수 있었다. 그 이유는 Fig. 6(a)와 (b)의 멀티 레이어 용융 풀에서 확인하였듯이 용융 풀이 일정하게 적층이 되지 못하여 용융 풀 간 발생된 공극에 의한 오차[9]로 인해 대부분의 조건들에서 팽창이 일어난 것으로 판단된다. 대부분의 파라미터에서 팽창률 1% ~ 2%에 분포되어 있는 것과 달리 Fig. 10(b)의 레이저 파워 30 W 이상과 스캔스피드 800 mm/s와 1800 mm/s에서 2% 이상의 큰 팽창을 확인 할 수 있었다. 대부분의 용융 풀은 Fig. 12(a)와 같이 중앙부를 중심으로 소재가 용융되며 아래로 오목해진 형태인 반면 큰 팽창률을 보인 시편은 Fig. 12(b)와 같이 용융 풀이 위로 볼록하게 팽창되어 있는 형상을 확인 할 수 있었다. 이런 현상이 일어나는 조건은 1.04 J/mm3~ 1.74 J/mm3로 고에너지 밀도에서 주로 발생되었다. 이는 Fig. 12(b)의 1.74 J/mm3 고에너지 밀도 조건에서 소재의 용융 풀 내 온도가 상승하게 되면서 용융되는 소재의 양이 증가하고 용융된 소재의 열적 유동 대류(thermal fluid convection)[10]도 크게 상승하며 발생된 팽창 현상인 것으로 사료되고 Fig. 12(b)가 Fig. 12(a)보다 상대적으로 높은 용융 풀 내 온도를 갖는 것으로 추정된다.
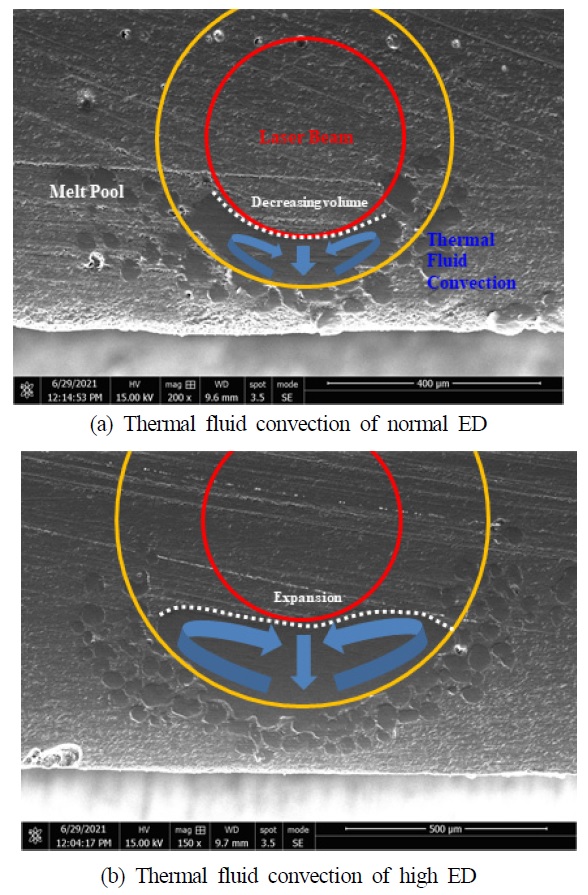
Schematic of thermal expansion, thermal fluid convection of melt pool that occurred through the printing process within (a) 30 W-2800 mm/s at ED 0.3 J/mm3 and (b) 5 W-800 mm/s at ED 1.74 J/mm3
Fig. 13은 신규 소재와 재사용 소재를 1:1 비율로 섞은 나이론 12계 혼합 소재의 DSC 분석을 한 결과를 통해 고에너지 밀도에서의 용융 온도를 추정해 보았다. 결정화 온도(Tc)와 녹는 온도(Tm) 사이의 적층이 가능한 온도 범위를 “SLM melting window”라고 한다[11]. DSC 분석을 통해 본 연구에 사용한 소재의 “SLM melting window”는 145℃ ~ 179℃ 사이임을 확인하였다. 하지만 이 온도 범위는 선택적 레이저 용융 방식에서 소재가 용융 풀을 형성하게 되는 온도 범위를 의미하는 것이지 공정 최적 온도 범위를 의미하는 것은 아니다.
Fig. 14는 최종품 시편의 수축률 분석을 통해 최적 형상 재현성을 갖는 에너지 밀도 조건(red line)을 중심으로 수축(red area)와 팽창(blue area)를 분포를 나타낸 것으로 최적 형상 재현성을 갖는 에너지 밀도는 공정 최적 온도를 갖는 조건을 의미한다고 할 때 에너지 밀도 0.24 J/mm3 ~ 0.35 J/mm3가 공정 최적 온도 조건임을 도출할 수 있다. 이 공정 최적 온도를 기준으로 기준 에너지 밀도 이하(수축, red area)에서는 용융 풀 내 온도가 결정화 온도(Tc) 근처로 최소한의 용융 풀은 형성은 되지만 층간 결합을 약하게 해 쉽게 수축 변형이 발생되었으며 기준 에너지 밀도 이상(팽창, blue area)에서는 용융 풀 내 온도가 녹는점(Tm)에 근접해져 많은 양의 소재가 활발한 열적 유동 대류를 하며 큰 용융 풀을 형성하게 되어 첨단부를 잃고 팽창 변형이 발생하는 등 형상 재현성이 저하되는 것을 확인하였다.
4. 결 론
본 연구는 레이저 파워와 스캔 스피드의 파라미터에 따른 에너지 밀도별 용융 풀의 너비(width)와 깊이(depth)를 정량화함으로서 최종품 시편의 형상 재현성 확보를 하고자 하였다.
그 결과 용융 풀을 형성하기 위한 최소 에너지 밀도는 0.06 J/mm3이며 최소 레이저 파워는 5 W 이상임을 확인하였다.
또한 허용 오차 범위 ± 0.5% 내의 최적 형상 재현성을 갖는 에너지 밀도 조건은 0.24 J/mm3 ~ 0.35 J/mm3임을 도출하였으며 이 조건에서의 용융 풀 내 온도가 공정 최적 온도를 갖는 조건임을 확인 할 수 있었다.
에너지 밀도별 용융 풀의 형상 및 너비와 깊이 확인을 통해 낮은 에너지 밀도 조건에서의 용융 풀 내 온도는 결정화 온도에 가까워 일반적인 용융 풀을 형성하기에 부족하여 최종품의 박리 및 수축 변형을 야기하게 되었다. 또한 높은 에너지 밀도에서의 용융 풀 내 온도는 녹는점에 가까워 소재의 열적 유동 대류가 활발해져 큰 용융 풀이 형성되면서 최종품의 첨단부 및 팽창 변형을 시키는 것을 확인할 수 있었다. 결과적으로 레이저 파워 및 스캔스피드에 따른 에너지 밀도의 열에너지는 용융 풀 내 소재에 전달되는 온도가 상이하며 이에 따라 다양한 형태의 용융 풀을 형성하여 최종품의 수축 및 팽창 변형에 영향을 미치는 것을 확인 할 수 있었다.
본 연구에서 확보한 최적 형상 재현성 조건이 일반 산업계에 적용 가능한 기계적 특성을 포함하는 것은 아니다. 하지만 선택적 레이저 용융 방식의 적층 제조 시스템이 최종적으로 실제 산업계에 적용하기 위해 가져야할 기계적 물성을 확보하는데 기초 자료가 될 것이다. 향후 최종품의 형상 재현성과 함께 산업계 요구 성능에 맞는 기계적 특성을 제어할 수 있는 공정 최적화 연구가 지속적으로 수행되어야 할 것이다.
Acknowledgments
본 연구는 산업통산자원부 “재생・재건 산업기술 실증 및 제품 인허가 지원체계 구축(P0018140)” 사업의 연구비 지원에 의해 수행되었습니다.
References
-
Ferro, C. G., Varetti, S., Pasquale, D. G., Maggiore, P., 2018, Lattice Structured Impact Absorber with Embedded Anti-icing System for Aircraft Wings Fabricated with Additive SLM Process, Mater. Today Commun., 15 185-189.
[https://doi.org/10.1016/j.mtcomm.2018.03.007]
-
Dzian, A., Živčák, J., Penciak, R., Hudák, R., 2018, Implantation of a 3D-printed Titanium Sternum in a Patient with a Sternal Tumor, World J. Surg. Oncol., 16:7 1-4.
[https://doi.org/10.1186/s12957-018-1315-8]
-
Malca, C., Santos, C., Sena, M., Mateus, A., 2018, Development of SLM Cellular Structures for Injection Molds Manufacturing, Science and Technology of Materials, 30:1 13-22.
[https://doi.org/10.1016/j.stmat.2018.03.001]
-
Ebrahimi, A., Kleijn, R. C., Richardson, M. I., 2021, Numerical Study of Molten Metal Melt Pool Behaviour during Conduction-mode Laser Spot Melting, J. Phys. D: Appl. Phys., 54 105304.
[https://doi.org/10.1088/1361-6463/abca62]
-
Chandrakanth, K., Sazzad, H. A., Asmed, M., Raghavan, S., 2017, Effect of Laser Power and Scan Speed on Melt Pool Characteristics of Commercially Pure Titanium (CP-Ti), J. Mater. Eng. Perform., 26 3560-3568.
[https://doi.org/10.1007/s11665-017-2768-6]
-
Antonella, S., Alireza, N., 2019, Microstructural Porosity in Additive Manufacturing: The Formation and Detection of Pores in Metal Parts Fabricated by Powder Bed Fusion, J. Adv. Manuf. Process., 2019:1 e10021.
[https://doi.org/10.1002/amp2.10021]
-
Drexler, M., Lexow, M., Drummer, D., 2015, Selective Laser Melting of Polymer Powder – Part Mechanics as Function of Exposure Speed, Phys. Procedia, 78 328-336.
[https://doi.org/10.1016/j.phpro.2015.11.047]
-
Raghunath, N., Pandey, P. M., 2007, Improving Accuracy through Shrinkage Modelling by using Taguchi Method in Selective Laser Sintering,Int. J. Mach. Tools Manuf., 47:6 985-995.
[https://doi.org/10.1016/j.ijmachtools.2006.07.001]
- Giovanni, G. A., Junior, F, N., De Arruda, L. V. , 2013, Weld Discontinuities Classification using Principal Component Analysis and Support Vector Machine, XI Simpósio Brasileiro de Automação Inteligente.
-
Dikshit, B., Zende, G. R., Bhatia, M. S., Sur, B. M., 2009, Convection in Molten Pool Created by a Concentrated Energy Flux on a Solid Metal Target, Phys. Fluids, 21:8 084105.
[https://doi.org/10.1063/1.3210763]
-
Schmid, M., Wegener, K., 2016, Additive Manufacturing: Polymers applicable for Laser Sintering (LS), Procedia Eng., 149 457-464.
[https://doi.org/10.1016/j.proeng.2016.06.692]
Researcher in the Functional Materials and Components R&D Group, Korea Institute of Industrial Technology.
Her research interests are polymer based additive manufacturing of selective laser malting type.
E-mail: ejshim@kitech.re.kr