
집속된 펨토초 레이저 빔에서 발생된 충격파를 이용한 유리기판 오염물 제거 연구
Abstract
The cleaning of particles below 1 μm on a substrate is a major concern in the display panel industry. The focused femtosecond Yb:KGW laser beam with an intensity of 2.42×1014W/cm2 is used for particle cleaning on a glass substrate. The force action of the shockwaves induced by the tightly focused laser beam presses down on particles and the particles are detached on the surface of the glass substrate. An image analysis software was used to measure the particle removal ratio. Over 110 shots of laser pulses were found at the optimal condition. A gap of less than 70 μm should be chosen between the focused laser beam and the particles for excellent laser cleaning on a glass substrate. With the smaller gap, the particle removal ratio can reach 95%; however, the surface of the glass substrate can be damaged within the beam propagation field.
Keywords:
Laser cleaning, Femtosecond laser, Glass substrate, Shockwave, SiO2 Particle1. 서 론
최근에는 구부리기 쉬운 디스플레이 패널을 만들기 위해 디스플레이 분야에서 얇은 유리의 활용도가 증가하고 있는 추세이다. 유리는 부서지기 쉽다는 단점을 가지고 있지만, 대다수 디스플레이 액정으로 사용되고 있다[1].
또한 과거 디스플레이 클리닝 공정상에서 2~3 마이크로미터 크기의 파티클(particle)은 큰 문제가 되지 않았지만 최근에는 디스플레이의 해상도의 발달로 인해 화소의 크기가 작아지게 되면서 1 마이크로미터 이하의 파티클의 제거의 필요성이 제기 되고 있다. 레이저를 활용한 세정 방법의 경우 반도체 및 디스플레이 분야에서 수마이크로~수백나노 크기의 입자를 제거하기 위한 방법으로 많은 연구가 수행 되어 왔다[2]. 이때 사용하는 가장 기본적인 3가지 방법으로 레이저의 어블레이션(ablation)을 이용하는 방법인 DLC (dry laser cleaning)[3], 액체를 기판위에 도포하여 클리닝하는 방법인 SLC (steam laser cleaning)[4], 충격파를 이용하여 기판 위를 클리닝하는 방법인 LSC (laser shockwave cleaning)[5-7] 가 있다. 이 외에도 3가지 방법을 혼합하거나 새로운 방법을 구상하여 다양한 조합으로 효율적으로 클리닝하는 방법이 연구 중에 있다. DLC 방식은 일반적으로 금속 위의 녹제거나 문화재를 복구하거나 수정할 때 많이 사용하고 있다[8-11]. 하지만 DLC 방식은 레이저의 집속 빔이 기판 위에 직접 닿아서 파티클 제거에는 좋은 효율을 보이지만 디스플레이의 유리 기판 표면에 데미지를 주게 되어 최종적인 제품의 품질에 영향을 미치게 된다. 또한 SLC 방식은 기판 위에 액체를 도포하여 클리닝 공정을 거친 다음 후처리 공정에서 액체를 완전히 제거해야 하는 단점이 있다.
본 연구에서는 디스플레이 유리표면에 손상을 입히지 않으며, SLC 방식처럼 표면에 액체를 도포하여 클리닝 과정 후 건조하는 번거로운 과정을 거치지 않는 LSC 방식을 이용하여 수 마이크로 이하 크기의 파티클을 제거하기 위한 최적의 조건을 찾고자 한다. LSC 방식은 레이저 빔 세기가 증가할수록, 그리고 빔 스폿과의 거리가 가까울수록 충격파의 세기의 증가와 압력의 증가로 인해 유리 기판에 붙어 있으려는 접착력보다 큰 힘이 작용하게 되는데 이는 나노미터크기의 작은 입자를 제거하기에 적절한 조건이 된다[12]. 또한 유리 기판에 레이저 노출시간이 길어지게 되면 유리 표면에 손상을 입게 되는데. 이를 확인하기 위하여 노출시간을 레이저 펄스의 수로 제어를 하여 실험을 하고자 한다. 이에 더하여 펄스 수를 제어를 하면서 유리 기판과 레이저 초점의 간격에 따른 유리 기판 표면에 손상과 클리닝 효율에 대한 실험을 진행한다.
2. 실험 장치 및 실험 방법
2.1 실험 장치 구성
레이저를 이용한 클리닝을 위한 구성은 Fig. 1과 같다. 233 fs의 펄스폭을 가진 Yb:KGW 레이저(Light conversion, PH2-10W)를 사용하였다. 이 레이저의 파장, 반복률, 펄스 에너지, M2은 각각 1030 nm, 50 kHz, 134 µJ, 1.2 이하이다. 그리고 배율이 20배이고, NA는 0.4이며, 동작거리(working distance)가 20 mm인 대물렌즈로 레이저 빔을 레이저 클리닝하는 유리 기판의 바로 위에서 유리 기판과 평행하게 초점 직경이 약 15.8 µm가 되도록 집속하였다. 레이저의 초점 위치는 Fig. 1의 유리 기판에 나타낸 x-y-z 방향으로 움직이는 3축 스테이지와 연동된 PC프로그램을 사용하여 제어하게 된다. 또한 레이저의 펄스 수는 레이저 발진기 소프트웨어를 사용하여 제어한다. Fig. 1에서 밸브로 공기압을 조절하여 공기가 빠르게 흐르도록 하면 유리 기판 쪽에서는 공기를 빨아들이게 되는 성질로 인해 유리 기판이 금형에 부착된다. 부착된 유리 기판은 z축으로 평탄도를 일정하게 갖게 되며, x축에 대한 평탄도는 스테이지 소프트웨어와 마이크로미터 조절나사를 이용하여 정밀하게 조절한다. 실험에서 사용한 유리 기판(Corning, Gorilla glass)은 디스플레이 패널로 사용되는 유리이다. 유리기판 위에 오염물질인 10 µm 이하 크기의 SiO2 입자를 무작위로 분사시켜서 붙어있게 하였다.
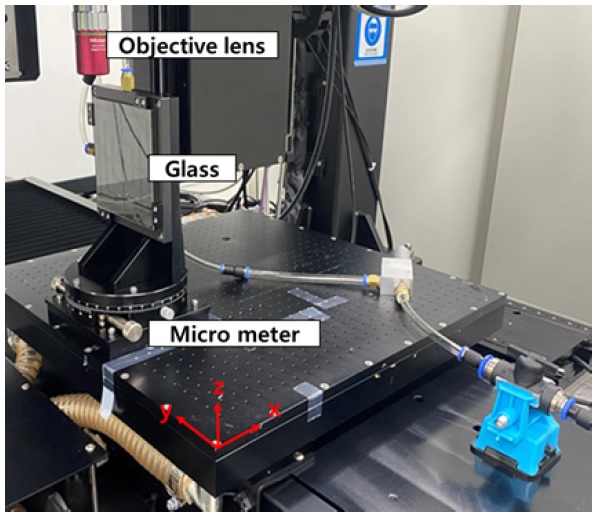
Photo of experimental set-up of a laser cleaning equipment for the removal of particles on a glass substrate by means of laser shockwave generated by focused femtosecond Yb:KGW laser beam
Table 1은 유리기판에 SiO2 입자를 무작위로 분사시키고 1분 동안 에어건으로 표면의 입자를 제거 후, 10개의 400×400 µm2 영역을 임의로 선택 후 선택한 영역에 대한 입자비율과 선택한 영역의 입자수를 개수한 결과이다. 입자의 초기조건이 균일함을 유지하기 위한 수치로 입자비율의 표준편차를 활용하였다. 또한, LSC 특성을 비교 시 입자비율이 유사한 샘플을 선택하여 사용하였다.
Fig. 2에서는 10개의 샘플 중에서 2개의 샘플을 임의로 선택하여 입자의 분포 및 형상을 도시하였다.
2.2 레이저 클리닝 변수
Fig. 3은 기판과 레이저 빔 초점의 구성을 나타낸 계략도이다. 레이저 빔 스폿과 유리 기판 사이의 간격을 조절하는 장치에서 대물렌즈가 스테이지에 부착되어 있으며, 스테이지를 x 축으로 움직임으로써 유리기판과 스폿 사이의 간격을 일정하게 조절한다. 레이저 빔은 Fig. 3에서 보듯이 유리 기판과 평행하게 입사하여 집속되면서 클리닝이 진행된다.
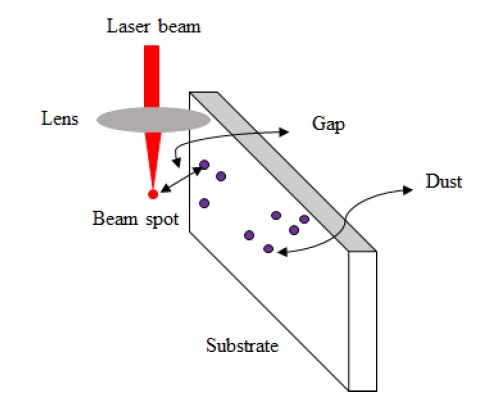
Schematic diagram describing the definition of the gap between a glass substrate and a laser beam spot
클리닝 시간과 클리닝 효율은 레이저 펄스의 수와 간격에 따라 변한다. 레이저는 50 kHz의 반복률을 사용하였으며, 단일 펄스와 단일 펄스 사이의 간격 시간이 20 ms이다. 펄스의 수를 제어 하였을 때 나타나는 클리닝 효과를 관찰하기 위해서 펄스의 수를 변환하면서 실험을 수행한다. 또한 레이저 초점에서 빔이 집속되면 높은 에너지밀도로 인해 충격파가 발생하게 되는데, 초점과 유리 기판이 근접할수록 입자의 제거에 필요한 임계 압력보다 높은 압력으로 인해 더 쉽게 제거되고 멀어질수록 임계압력과 비슷하거나 낮아지게 되므로 클리닝의 효율이 떨어지는 것을 예측할 수 있는데, 이를 실험적으로 관찰하고자 한다.
2.3 실험방법
유리 기판 위에 SiO2 입자 분사를 하게 되면 입자들끼리 응집을 하게 되어 크기가 커지는 입자가 발생한다. 레이저 클리닝으로 이 응집된 입자들 위로 빔을 집속시켜도 응집된 입자의 분해 및 재 부착 때문에 응집된 입자가 유리 기판에서 잘 떨어지지 않기 때문에 1차적으로 에어건을 통한 크게 응집된 입자를 제거한다. 이때 크기가 작은 입자들은 에어건의 압력보다 더 강한 접착력으로 유리 기판에 붙는다. 이러한 작은 크기의 입자를 제거하기 위해서 대물렌즈로 집속시킨 에너지 밀도가 높은 빔 스폿을 유리기판 위에 형성한 후, 이 집속된 빔이 공기 중에 주로 산소와 질소가 주로 브레이크다운을 일으키고 플라즈마를 생성한다. 이 플라즈마는 순식간에 퍼져나가는 충격파를 만들고, 이 충격파가 기판 위에 붙어있는 SiO2 입자를 제거한다. Fig. 4는 초고속 카메라(Kron technologies, Chronos 1.4)를 사용하여 클리닝 과정을 찍은 사진으로 Fig. 4(a)는 유리 기판의 단면을 옆에서 보여주는 것이고, (a)로부터 각각 6.659 ms, 10.395 ms, 41.112 ms 후에 찍은 단면 사진이 Fig. 4(b) ~ (d)이다. Fig. 4(b) ~ (d)에서 관찰된 유리 기판의 단면 상단에서 푸른 점인 플라즈마가 급속히 퍼져나가면서 발생하는 섬광을 볼 수 있다.
2.4 오염물 제거 분석 방법
클리닝 전과 후의 SiO2 입자의 제거율을 측정하기 위해 전용소프트웨어((주)이너뷰사, 이너뷰(Innerview))를 사용한다. Fig. 5(a)는 입자의 개수 및 면적을 분석하기 위한 소프트웨어의 사진이다. 분석 범위 면적에서 입자가 가진 면적의 비율을 이용하여 유리 기판에 부착된 SiO2의 제거율을 구할 수 있다. Fig. 5(b)는 프로그램을 통해 분석된 입자의 크기별 개수 분포도를 나타낸다. 클리닝의 범위 영향을 고려하여 400 µm × 300 µm의 영역을 설정하여 클리닝 전과 후의 비교 분석을 진행하였다. 입자의 크기는 지름이 1 µm 이하가 50 % 이상으로 구성되도록 하였다.
3. 실험 결과
3.1 집속빔과 기판사이의 간격에 따른 손상
레이저 클리닝 실험을 위해서는 레이저 집속 빔을 기판과의 일정한 간격을 두고 기판에 붙은 입자를 기판의 손상 없이 제거해야 하는데, 레이저 초점이 유리 기판으로부터 떨어진 간격의 정도에 따라 유리 기판에 가해지는 충격파의 손상이 달리진다. Fig. 6 에서는 유리기판에 평행한 레이저 빔의 집속과 레이저 빔 전파 형상을 도시하였다. 여기서 W0는 집속빔의 반경인 빔 웨이스트(beam waist), d는 집속빔의 중심과 기판의 간격 및 l은 유리기판의 길이의 반이다.
먼저, z 축 스테이지의 평탄도를 일정하는 것이 레이저 빔과 유리기판의 간격에 대한 연구에 중요한 지표로써, z 축 높이를 0, 100, 200, 300 µm 위치로 이동하면서 집속빔 크기가 일정하게 유지됨을 확인하였다. 초점 위치에서 집속빔의 직경 크기는 15.8 µm로 측정되었으며, 측정한 각 위치에서 집속빔 크기의 최대 오차는 300 µm 위치에서 3.7% 이내로 측정되었다.
Fig. 6에서는 초점위치에서 초점용 빔프로파일러(Metrolux, FM100-focus Monitor 100)을 사용하여 빔 크기 및 형상을 측정한 결과와 이 때 빔전파의 예측을 하기위해 식을 이용하여 도시하였다. 여기서 ZR은 레일레이 길이(Rayleigh length)이다.
(1) |
(2) |
수식 (2)에서 W0는 빔 반경으로 7.9 µm, λ는 레이저 빔의 파장으로 1030 nm를 사용하였다. LSC 공정은 주로 레이저 빔의 초점 근처에서 발생하지만, 레이저 빔이 전파시 직접적으로 기판에 영향을 배제하기 위해서는 해당 Z축의 위치에서 Fig. 7 그래프의 y 축 상단의 값으로 간격(d)를 유지해야 하며, Z = 300 µm일 때 값인 14.4 µm 이상을 유지하면 안정적으로 레이저 빔과 유리기판의 접촉을 배제 가능함을 예측할 수 있다.
Fig. 8(a)은 레이저 빔 초점을 유리 기판의 제일 위쪽 가장자리에서 z축 하단 방향으로 300 µm를 이동하고 레이저 초점과 유리 가판 사이의 간격이 2 µm인 상태에서 레이저 펄스를 수백만회 조사하여, 레이저를 수십 초 이상으로 길게 노출시켰다. 본 실험은 유리기판의 레이저 빔에 의한 손상을 보고자 하는 목적으로 입자의 분사 없이 수행하였다. 이 때 유리 가판의 손상 현상을 SEM (scanning electron microscope)(Carl Zeiss, Merlin compact)을 통해 관찰한 결과이며, Fig. 8(b)은 이 간격이 60 µm일 때 SEM을 통해 촬영한 사진이다. 레이저의 진행 방향은 Fig. 8(a)와 (b)에서 적색 화살표로 나타냈으며, 화살표 끝 부분이 초점이고 이 근처가 손상을 입는 곳이다. (b)에서는 광학 현미경 및 육안으로 화살표 밑의 손상부분을 뚜렷하게 볼 수 있지만, 간격이 Fig. 8(c)와 같이 70 µm 이상 일 때에는 레이저 충격파에 의한 손상이 관찰되지 않는다.
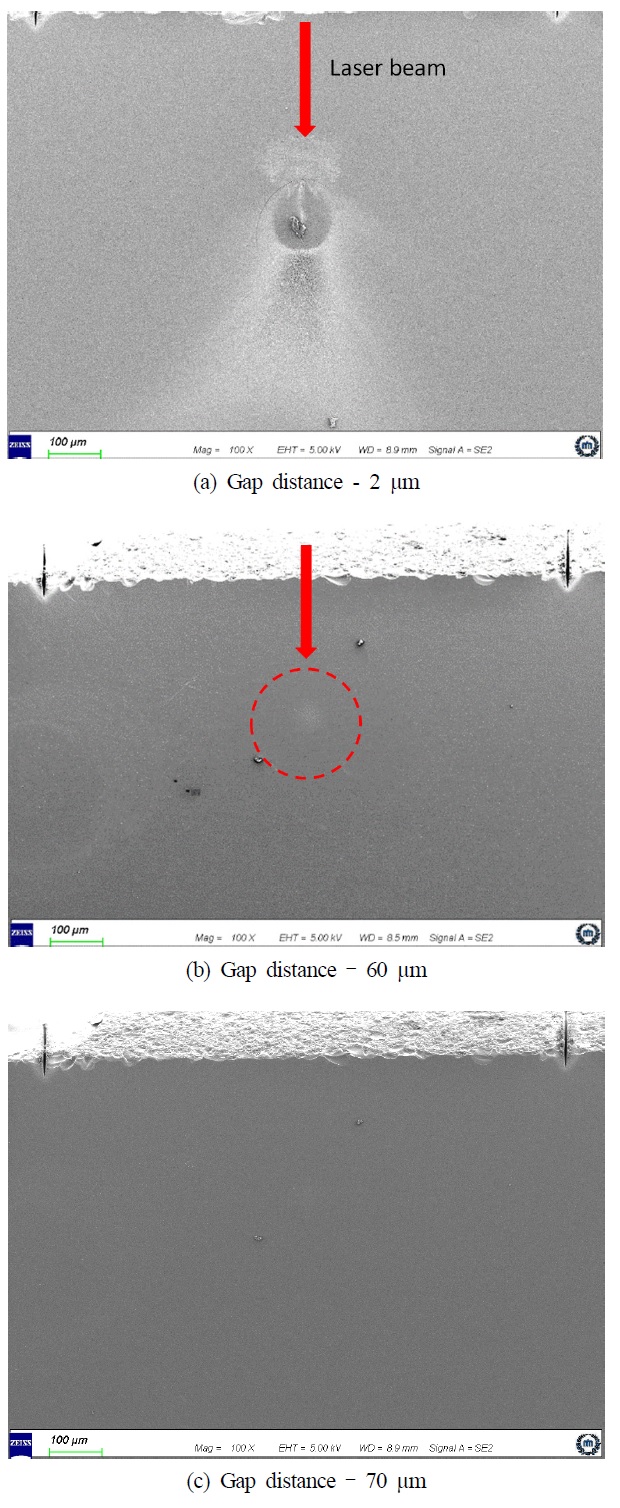
Photos of glass substrate surfaces with various gap distance to observe damage of a glass plate after laser cleaning
Fig. 9의 상단 사진은 레이저 어블레이션으로 인해 기판에 발생한 입자를 3만 배의 고배율로 확대한 사진이며, Fig. 9의 하단 사진들은 상단 사진의 초록색 사각형 부분의 불순물처럼 보이는 입자들에 대한 EDS (energy dispersive spectroscopy) 분석을 한 결과로 왼쪽 상단 사진부터 우측 하단 사진으로 각각 탄소(C), 산소(O), 나트륨(Na), 마그네슘(Mg), 알루미늄(Al), 실리콘(Si)의 분포도를 보여준다. 즉 Fig. 9의 하단 사진들은 상단 사진의 사각형 안을 EDS 맵핑 분석으로 진행한 것이며, 검출된 입자들의 종류와 분포도를 보여준다. 입자와 유리 기판의 성분이 다르다고 하면 각 성분에서 입자 모양대로 성분이 검출 되어야 하는데 6가지 성분의 분포도는 전체적으로 균일하기 때문에 상단 사진에서 나온 막대기나 둥근 부분의 성분은 유리 기판과 동일한 성분임을 알 수 있다. 즉 이 입자들은 레이저로 인한 유리기판의 표면 어블레이션(ablation)이 발생하여 생긴 입자임을 알 수 있다.
3.2 레이저 펄스 수에 따른 제거율
Fig. 8의 결과에 따라 유리 기판에 손상이 일어나지 않는 간격을 70 µm로 설정하였고, LSC 공정 시간을 단축하기 위하여 레이저 펄스수를 최소화 하는 것을 목표로 실험을 수행하였다. 즉 pc를 통한 레이저 셔터를 제어함으로써 레이저 펄스의 수를 3, 5, 10, 30, 50, 70, 90, 110회로 변화시켜 클리닝 제거율에 대해 실험을 하였다. 레이저의 단일 펄스 주기는 20 ms로 펄스의 수가 증가함에 따라 유리 기판에 노출되는 펄스의 수가 많아진다. 이 때 레이저 펄스의 수가 증가할수록 입자에 가해지는 충격파의 압력과의 접촉 시간이 길어지기 때문에 누적된 에너지로 인해 높은 클리닝의 효율을 보인다. Fig. 10(a)와 (b)는 각각 레이저 펄스 수가 110회 일 때 클리닝 전과 후의 유리 기판의 입자 분포 사진이며, 사진 중앙에 마킹 영역은 초점 위치를 도시하기 위하여 실험 전에 원점 위치를 레이저로 마킹한 지점이다. Fig. 10의 결과를 분석하여 레이저 펄스 수에 따른 제거율을 측정한 결과가 Fig. 11의 그래프이다. Fig. 11의 그래프에서 보듯이 펄스 수 30번부터 약 80% 이상의 클리닝 효율을 보이고 있지만 레이저 펄스수가 110회 이상일 때 가장 높은 클리닝 효율과 재현성이 나타나며 85% 이상의 제거율을 보인다. 즉, 30회 이상의 펄스 수에서는 제거율의 증가가 둔화됨을 알 수 있으며, 펄스 수 증가에 따른 기판의 손상을 고려하여 110회를 최적의 펄스 수로 설정하였다.
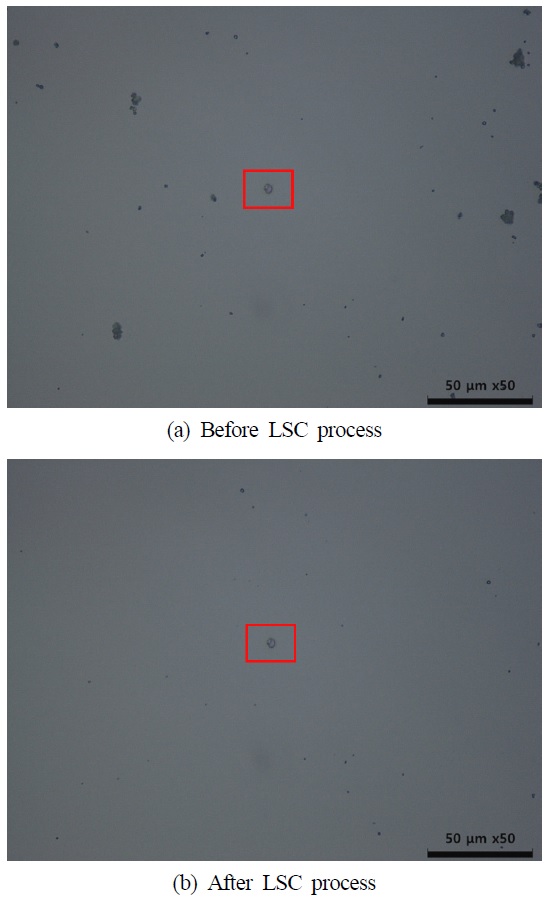
Result of LSC process applying 110 pulses by using optical microscope (50x); rectangle represents laser marking spot for reference positioning
3.3 기판과 레이저 빔 사이의 간격에 따른 제거율
Fig. 8와 Fig. 11의 결과로부터 레이저 초점과 유리 기판 사이의 간격과 레이저 펄스 수는 각각 70 µm,와 110회로 고정하였을 때, 제거율은 85%이다. 제거율이 85% 이지만 나머지 15%는 1 µm 이하의 매우 작은 입자가 유리 기판에 존재하는 것으로 추정된다. 제거율을 높이는 방법으로는 펄스의 수를 증가시키거나, 레이저 초점과 유리 기판 사이 간격을 좁히는 방법이 있다. 레이저 펄스의 수를 증가하는 경우는 유리 기판에 레이저를 오랜 시간 동안 노출시키게 된다. 이로 인해 일정 펄스 수 이상을 노출시키게 되면 유리표면에 물리적인 레이저 어블레이션의 발생과 열적인 손상이 발생할 수 있으므로, 노출 시간을 최소화하였을 때 간격을 변화시키면서 최적의 조건을 도출하였다.
Fig. 12는 레이저 펄스 수를 110회로 고정하고 간격에 따른 유리표면 손상 여부를 SEM 사진을 통하여 보다 상세히 관찰한 결과이다. Fig. 12는 레이저 빔의 초점과 유리기판의 간격을 70 µm와 20 µm로 설정하여 레이저 클리닝을 한 후, 유리 기판의 입자들의 분포도를 찍은 사진이다. 앞서 언급하였듯이 집속빔 전파시 빔과 유리기판이 접촉하는 않은 간격을 14.4 µm으로 도출하였으며, 그 이상인 20 µm으로 설정하였다. Fig. 12의 고배율 SEM 사진으로부터 열로 인한 손상이 없다는 것을 알 수 있으며, 레이저 어블레이션으로 인한 입자들의 발생도 일어나지 않음을 알 수가 있다. 클리닝 효율은 간격이 70 µm일 때 약 85% 가량으로 분석되었으며, 20 µm 이하로 간격이 좁아지면 95%까지 제거율이 증가된다.
Fig. 13에서는 레이저 빔이 유리기판 상부에서 조사될 때, 4개의 영역에서 SEM 사진을 2,500배로 확대하여 기판의 손상을 관찰하였다. ④ 영역은 원점을 확인하기 위한 레이저 마킹 지점으로 LSC 공정에서의 기판 손상과 무관하며, 각 영역에서 기판 손상이 없음을 확인하였다.
Fig. 14(a)는 레이저 클리닝 전의 유리 기판에 붙은 입자들의 광학현미경을 찍은 분포 사진이고, (b)와 (c)는 레이저 펄스수를 110회로 고정한 후에 각각 간격이 30 µm와 150 µm일 때의 레이저 클리닝 후에 찍은 광학현미경 사진들로 프로그램을 사용하여 시각적으로 나타낸 것이다. 입자들은 노란색 테두리에 빨간색으로 채워져 있는 사진이며, 빨간색이 나타내는 곳이 작을수록 입자의 크기가 작다. 또한 사진에 나타나는 빨간색으로 표시가 되지 않는 검은 점들은 현미경 렌즈의 노이즈이다. 간격이 30 µm일 때는 마킹한 중심 부분에서 대부분의 작은 입자도 제거된 것을 알 수 있지만 150 µm일 때는 특히 작은 입자들이 제거가 안 된 것을 알 수 다. 이는 레이저에서 발생하는 충격파가 작은 입자들을 유리기판에 분리하기 위한 반데르발스힘에 충분하지 않다고 판단된다.
간격을 20 µm, 30 µm, 70 µm, 110 µm, 150 µm로 변화시키면서 측정한 제거율 그래프가 Fig. 15이다. 간격이 30 µm 이하에서는 제거율 90% 이상의 효율을 보이고 있으며 간격이 증가함에 따라 제거율은 선형적으로 감소함을 알 수 있다.
4. 결 론
펨토초 레이저의 초점에서 발생된 충격파를 이용하여 유리 기판 위에 수마이크로 크기의 오염물질인 SiO2를 제거하는 실험을 수행하였다. LSC 공정에서 오염물질이 제거되는 현상을 고속 카메라로 측정하였고, 장시간의 레이저 펄스를 노출시 유리기판에 손상이 발생함을 알 수 있었다. LSC 공정 시간 단축과 유리기판 손상을 최소화하기 위하여 펄스수를 110회로 최적화 하였으며, 집속빔의 중심과 기판사이의 간격이 70 µm일 때, 85% 정도 수준의 오염물질 제거율을 도출하였다. 집속빔의 지름의 크기는 15.8 µm이며, 레이저 빔 전파시 기판과의 접촉이 되지 않는 최소 간격은 14.4 µm로 예측하였으며, 실제 간격을 20 µm로 설정 후 기판의 손상이 발생하지 않음을 알 수 있었다.
이 간격에서 오염물질의 제거율은 95% 이상임을 알 수 있었으며, 간격을 점차적으로 증가시 LSC의 제거효율은 급격히 감소함을 알 수 있었다.
본 연구를 통하여, LSC의 주요 공정 요소는 레이저 펄스 에너지, 펄스 폭, 펄스 수에 따른 발생하는 에너지가 주변의 공간에 충격파를 발생하고 오염물질의 제거에 중요한 요소임을 알 수 있으며, 기판과의 간격은 레이저 빔 전파시 발생하는 접촉 및 열영향으로 인한 기판 손상과 관계가 밀접하며, 충격파와 오염물질의 상대거리에도 영향을 미침을 알 수 있었다.
결론적으로 유리기판의 손상을 최소화하기 위하여, 펄스 수는 최소화하는 것이 유리하며, 유리기판의 레이저 빔의 영향을 배제하는 범위에서 간격을 최소화 하는 것이 LSC 공정에서 중요함을 알 수 있었다.
Acknowledgments
이 연구는 한국기계연구원 주요사업인 “핵심 기계 설비 스마트 설계 플랫폼 기술 개발” 및 산업통산자원부 우수기업연구소 육성사업인 “지능형(Al/IoT/DDI/6G) 반도체 테스트를 위한 피치 33 μm, 20,000 pin급 수직형 인터페이스 프로브 및 공간변환기 개발(20014122)”에 의하여 수행되었습니다.
References
-
Auch, M. D. J., Soo, O. K., Ewald, G., Chua, S. J., 2002, Ultrathin Glass for Flexible OLED Application, Thin Solid Films, 417:1-2 47-50.
[https://doi.org/10.1016/S0040-6090(02)00647-8]
-
Graf, J., Luk’yanchuk, B. S., Mosbacher, M., Hong, M. H., Chong, C. T., Boneberg, J., Leiderer, P., 2007, Matrix Laser Cleaning: A New Technique for the Removal of Nanometer Sized Particles from Semiconductors, Appl. Phys. A, 88 227-230.
[https://doi.org/10.1007/s00339-007-4017-6]
-
Zhang, C. L., Bin, L. X., Wang, Z. G., Liu, C. M., Xiang, X., Lv, H. B., Yuan, X. D., Zu, X. T., 2011, Laser Cleaning Techniques for Removing Surface Particulate Contaminants on Sol-Gel SiO2 Films, Chinese Phys. Lett., 28:7 074205.
[https://doi.org/10.1088/0256-307X/28/7/074205]
-
Frank, P., Lang, F., Mosbacher, M., Boneberg, J., Leiderer, P., 2008, Infrared Steam Laser Cleaning, Appl. Phys. A: Materials Science and Processing, 93 1-4.
[https://doi.org/10.1007/s00339-008-4651-7]
-
Park, J. K., Yoon, J. W., Cho, S. H., 2012, Removal of Nanoparticles from a Silicon Wafer using Plasma Shockwaves Excited with a Femtosecond Laser, Appl. Surf. Sci., 258:17 6379-6383.
[https://doi.org/10.1016/j.apsusc.2012.03.044]
-
Varghese, I., Murthy Peri, M. D., Dunbar, T., Maynard, B., Thomas, D. A., Cetinkaya, C., 2008, Removal of Nanoparticles With Laser Induced Plasma, J. Adhes. Sci. Technol., 22:5-6 651-674.
[https://doi.org/10.1163/156856108X305561]
-
Kim, T. H., Cho, H. C., Busnaina, A., Park, J. G., Kim, D. S., 2013, Shockwave-induced Deformation of Organic Particles during Laser Shockwave Cleaning, J. Appl. Phys., 114:6 063104.
[https://doi.org/10.1063/1.4818307]
-
Esbert, R. M., Grossi, C. M., Rojo, A., Alonso, F. J., Montoto, M., Ordaz, J., Andrés, M. C., Escudero, C., Barrera, M., Sebastián, E., Rodríguez-Navarro, C., Elert, K., 2003, Application Limits of Q-switched Nd:YAG Laser Irradiation for Stone Cleaning based on Colour Measurements, J. Cult. Herit., 4 50-55.
[https://doi.org/10.1016/S1296-2074(02)01227-X]
-
Koh, Y. S., Sárady, I., 2003, Cleaning of Corroded Iron Artefacts using Pulsed TEA CO2– and Nd;YAG-lasers, J. Cult. Herit., 4 129-133.
[https://doi.org/10.1016/S1296-2074(02)01140-8]
-
Mazzinghi, P., Margheri, F., 2003, A Short Pulse, Free Running, Nd:YAG Laser for the Cleaning of Stone Cultural Heritage,Opt. Lasers Eng., 39:2 191-202.
[https://doi.org/10.1016/S0143-8166(01)00133-6]
- Morais, P. J., Gouveia, H., Apostal, I., Damian, V., Garoi, F., Iordache, I., Bojan, M., Apostal, D., Campo, J. A. R., Galli, R., 2010, Laser Beam in the Service of Paintings Restoration, Romanian Reports in Physics, 62:3 678-686.
- Yu, H. C., Li, H. Y., Wu, X., Yang, J., 2020, Dynamic Testing of Nanosecond Laser Pulse Induced Plasma Shockwave Propulsion for Microsphere, Appl. Phys. A: Materials Science & Processing, 126:63 1-8.
Master’s course in the Department of Photonics and Sensors, Hannam University.
His research interest is laser application and laser metrology
E-mail: myeongjun@kimm.re.kr
Professor in the Department of Photonics and Sensors, Hannam University.
His research interest is laser metrology, 3D scanning technology, and lens design.
E-mail: jhjo@hnu.kr
Principal researcher in Korea Institute of machinery & materials.
His research interest includes ultra-short pulsed laser machining, cleaning, and laser systems control
E-mail: khkim@kimm.re.kr