
가공 방식에 따른 엔지니어링 플라스틱의 초음파 피로 특성 분석
Abstract
Engineering plastics are continuously being developed to achieve light weight and long life, and interest in fatigue is increasing to apply the plastics to various products. Plastic shows the properties of materials that vary depending on the processing; therefore, clear research and analysis are required. In this study, the characteristics of fatigue life according to the processing were confirmed for POM and ABS. The fatigue characteristics were measured using the ultrasonic fatigue test, and a specimen was manufactured through a mechanical processing using plastic deformation and laser processing using thermal energy. In the case of POM, similar fatigue characteristics were confirmed by achieving a compliant surface finish for the two processings. However, in the case of ABS, carbonization by heat welding was observed in laser processing. Consequently, stress concentration occurred during the fatigue test, and the fatigue characteristics were degraded compared with those of the mechanical processing.
Keywords:
Engineering plastic, ABS, POM, Mechanical processing, Laser processing, Ultarsonic fatigue test1. 서 론
경량화와 고수명의 달성을 위해 향상된 물성의 엔지니어링 플라스틱이 지속적으로 개발되고 있으며, 제품으로의 적용을 위해 재료의 기초 물성인 피로수명에 관한 관심이 증가하고 있다. 일반적으로 폴리머 계열 소재의 피로 물성은 재료의 특성상 짧은 사용주기로 인해 많은 연구가 이루어지지 않았지만 최근 개발 및 적용되고 있는 엔지니어링 플라스틱의 경우 경금속과 유사한 목적으로 경량화, 원가 절감, 생산성 향상에 장점이 있어 관련 연구가 활발히 진행되고 있다[1-3]. 대표적인 엔지니어링 플라스틱의 종류로는 Polyoxymethylene(POM), Polycarbonate(PC), Acrylonitrile butadiene styrene copolymer(ABS), Polystyrene(PS) 등이 있으며 이러한 재료는 전자제품의 커버, 샤프트 지지부, 기어, 구조체 부품 등으로 사용되고 있다[1-4]. 이러한 부품들은 높은 응력이 순간적으로 집중되고 반복적인 응력이 부가되는 등 다양한 피로 환경에서 동작하고 있으므로 제품의 수명 주기 동안 고장이 발생하지 않도록 설계 및 제조가 되어야 하며 이러한 내구 수명 기능을 충족시키기 위해서는 피로 수명에 대한 이해와 정량적인 실험이 매우 중요하다.
반면, 피로수명에 대한 물성은 실험에 많은 시간과 노력이 소요되며, 재료의 균질도, 표면 상태, 제조 환경 및 조건 등에 직접적인 영향을 받고 수명의 평가 결과에도 많은 편차가 발생하므로 이에 대한 특성을 정확히 파악하고 다수의 실험을 통한 통계학적인 오차의 분포를 확인하는 것이 매우 중요하다. 특히 플라스틱은 금속류에 비해 가공 방법에 따라 재료의 물성이 달라지는 특성을 나타내므로 이에 관한 명확한 연구 및 분석이 필요하다.
본 연구에서는 엔지니어링 플라스틱의 가공 방법에 따른 피로수명의 특성을 가속 피로 시험법 중 하나인 초음파 피로 시험법을 적용하여 분석하였다. 가공 방법으로는 소성변형을 이용한 기계적 가공 방법과 열에너지를 이용한 레이저 절단을 통해 시편을 제작하고 이에 따른 피로시험을 진행한 후 분석을 시행하였다.
2. 초음파 피로시험 준비
2.1 초음파 피로시험 시편 설계
전통적인 피로시험의 경우 시험 장치로부터 5~60 Hz의 낮은 주파수의 외력이 시편에 전달되며 강제로 인장, 압축 하중을 가하여 피로시험을 수행한다. 그러나 초음파 피로시험은 시편이 갖는 고유의 공진 주파수로 진동시 발생하는 응력을 이용하여 응력비(R)가 –1 인 상태에서 고속으로 피로시험을 수행한다. 시편은 한쪽 끝이 고정되지 않는 자유단을 갖는 상태로 시험 장치에 부착되고, 시험기에서 전달되는 가진 주파수는 시편의 길이 방향 인장-압축 Mode shape의 고유 주파수와 일치해야 한다. 따라서 20 kHz의 작동주파수에서 시편 중심에서 공진이 발생하는 시편의 설계를 위해 동탄성계수를 측정하고 이를 기반으로 시편의 정밀설계가 필수적이다[5].
동탄성계수 측정을 위해 Fig. 1과 같이 ASTM E1875의 Sonic resonance method에 맞는 실험 장치를 구성하였다[6]. 시편에서 발생하는 공진의 측정은 Laser Doppler Velocimeter(LDV)를 사용하였으며, Fig. 2와 같이 공진주파수를 측정하였다. 측정된 첫 번째 공진 주파수를 바탕으로 식(1)을 통해 동탄성계수를 Table 1과 같이 계산하였다.
(1) |
이 식의 [f]는 Sonic resonance method를 통해 측정된 공진 주파수이며, [l]은 피로시험 시편의 길이, [ρ]는 밀도값이며 [Ed]는 식(1)을 통해 계산된 동탄성계수이다.
이후 시편은 Claude Bathias와 Paul C. Paris가 제안한 최대 응력 진폭식을 기반으로 설계하였다[7]. 시편의 형상 및 설계에 필요한 변수는 Fig. 3에 표기하였다. 각 변수는 앞서 계산한 동탄성계수를 바탕으로 계산되며, 이에 대한 식은 식(2)-(4)이다. 본 연구에서는 시편의 설계 매개변수의 영향을 줄이기 위해 Table 2와 같이 모든 시편의 R1, R2, L2값을 동일하게 설정하고 L1 값을 계산하여 설계 변수를 도출하였다
(2) |
(3) |
(4) |
2.2 초음파 피로시험 시편 제작
가공 방법에 따른 피로수명 비교를 위해 Hass Automation사의 VF-2머시닝센터를 활용한 절삭가공과 EV레이저사의 ELPC-TS Series(비금속용) CO2 레이저 가공기를 사용하여 시편을 제작하였다.
절삭가공에서의 각 치수의 정밀도는 ±30 μm 이내에서 관리되었으며 레이저 가공에서의 정밀도는 ±200 μm 수준에서 완성 시편의 공차를 유지하였다. 절삭가공에서는 절삭력에 의한 가공 중 변형 및 재료 특성으로 인한 취성 파괴 등을 최소화하고자 절삭 조건의 선정에 있어 엔드밀의 최대 절입 깊이를 100 μm 이하에서 가공하였다. CO2 레이저 가공에서는 열융착부 및 보조 가스에 의한 가공 중 시편의 흔들림으로 인한 문제를 고려하여 예상 소요 시편의 3배수를 가공하여 목표 공차 값 이내에서 완성된 시편만을 선별하여 초음파 피로 시험기에 시편을 고정할 수 있는 나사부를 절삭가공으로 가공하였으며 제작된 시편의 형상은 Fig. 4, 5와 같다.
Fig. 6은 재료 및 가공 방법에 따른 가공면의 특성을 보여 주고 있다. POM의 경우 흰색이므로 가공면의 확인이 어려워 색상 반전을 진행한 후 분석을 진행하였다. 시편 제작에서 POM의 경우 절삭가공 및 CO2 레이저 가공 모두에서 가공면의 양호한 표면 거칠기 상태를 확인할 수 있었으나, ABS의 경우 CO2 레이저 가공에서 열융착으로 인한 탄화 형상을 관찰할 수 있었다.
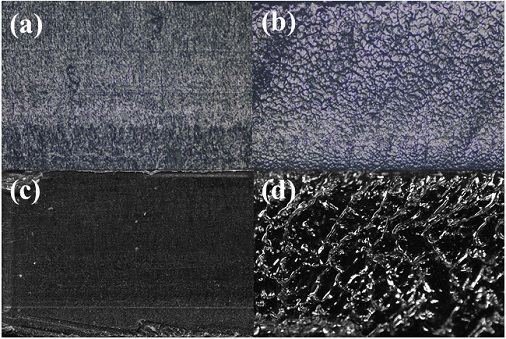
The processed surface of a specimen (a) POM, mechanical processing, (b) POM, laser processing (c) ABS, mechanical processing, (d) ABS, laser processing
초음파 피로시험에서는 진동파에 의한 공진 시험방법을 이용하기 때문에 시험 시편을 시험장비에 안정적이면서도 균일하게 고정하는 것이 중요하다. 이와 관련하여 시험 시편 나사부의 공차 관리 및 가공 방법은 매우 중요한 요소이다. 나사부 가공에 있어 제이제이툴스사의 목표 2HRB 003 020모델의 300 μm 2F Ball End Mill, 티엔티사의 주문형 60° Thread Mill, 에스케이씨사의 Threading Die를 각각 사용하여 나사부를 가공한 결과 300 μm 2F Ball End Mill과 주문형 60° Thread Mill에서 사항에 만족하는 나사 품질을 얻을 수 있었다. Threading Die의 경우 수나사 가공의 외경부 공차는 KS 등 관련된 산업 규격에는 만족하는 수준으로 가공되었으나 나사부 유격으로 인하여 시험 중 시편의 목 부러짐과 같은 비정상적인 시편 파괴를 확인할 수 있었다. 실험에 사용된 최종적인 시편 가공은 300 μm 2F Ball End Mill, 주문형 60° Thread Mill을 사용하여 시편 가공을 진행하였다.
가공 방식의 특성상 절삭가공을 통한 가공 시편 1개의 평균 가공시간 대비 CO2 레이저 가공의 시편 가공 시간은 20배 이상의 빠른 장점이 있었지만, ABS 소재의 시편에서는 열융착부의 영향 등을 고려할 때 엔지니어링 플라스틱의 피로시험 시편 제작에 있어 공정 선택의 부분적 근거로 활용할 수 있음을 확인하였다.
2.3 초음파 피로시험 시스템
초음파 피로시험은 압전 세라믹으로부터 발생된 20 kHz 탄성 진동파에 의한 공진 시험방법이다. Transducer에서 발생 된 진동은 공진 주파수에 맞춰 설계된 Horn에 의해 증폭되어 시편에 전달된다. 시편 또한 20 kHz에서 공진이 발생하도록 설계하였기 때문에 시편의 중앙 파단 위치에서 최대 응력과 최소 변위가 발생하며, 최대 응력 집중이 반복되어 R= -1의 응력비를 갖는 피로시험이 진행된다.
초음파 피로시험 시스템은 Fig. 7과 같이 구성된다. 원하는 출력을 발생시키는 PZT Amplifier와 초음파 진동을 발생시키는 PZT Transducer, 진동을 증폭하여 시편으로 전달하는 Horn으로 구성된다. 시편 진동으로 인한 변위는 LDV로 측정되며 식(5)를 통해 시편 중앙 파단부에 부여되는 응력으로 환산하였다. 식(5)의 A0 값은 시편 파단 위치의 단면적이다.
(5) |
피로시험 시 시편의 중심에 최대 반복 응력이 순간적으로 가해지면서 열이 발생한다. 대부분의 물질이 온도의 변화에 따라 물성의 변화가 발생하며, 특히 녹는점이 낮은 폴리머 계열 소재에 가해지는 열은 피로수명에 주요한 영향을 주는 변수이다. 이를 해결하기 위해 Air Cooling nozzle을 사용하였고, 초음파 가진 ON/OFF 시간을 조절하여 열 영향을 최소화하였다.
3. 실험 분석
3.1 초음파 피로 특성
Fig. 8은 시편의 제작 방법에 따른 POM, ABS 소재에 대한 피로시험 결과이다. 두 소재 모두 분산이 크게 발생함을 확인하였다. 이는 시편의 두께가 얇아 Air Cooling nozzle에 의해 시편에 발생한 기생 변위의 영향과 내부의 기공과 같은 원재료 결함이 원인이 되어 발생한 것으로 판단된다.
POM의 경우 절삭가공 시편과 CO2 레이저 가공 시편의 피로 파괴 지점이 비슷하게 분포하는 반면 ABS의 경우 피로 파괴 지점이 여러 방향에서 나타나는 것을 확인할 수 있었다. 이는 Fig. 6의 가공면을 참조하였을 때 ABS의 CO2 레이저 가공에서 표면에 발생한 열융착으로 인하여 표면 거칠기가 매우 거칠게 나타났으며 이로 인하여 가공 표면의 거친 면이 미세 균열의 역할을 하여 초음파 피로시험 시 응력 집중의 부분적 원인이 되었으며 이에 따라 피로 특성이 낮게 측정된 것으로 판단된다.
이러한 특징은 Fig. 9의 피로 파단면에서도 확인할 수 있다. 피로 파괴는 일반적으로 표면부의 게재물이나 공동 등 결함 부위에서 시작하여 크랙이 시작되고 피로 파괴가 전파되는 것으로 알려져 있다. POM의 두 종류의 가공 시편과 ABS의 절삭가공 시편의 경우 비치마크(beach mark)를 따라 피로 파괴가 진행된 것을 확인할 수 있다.
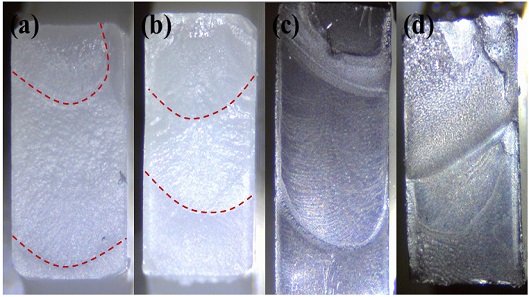
The overall view of the fatigue fracture surface (a) POM, mechanical processing, 20.02 MPa, 36889 cycle (b) POM, laser processing, 19.50 MPa, 31526 cycle (c) ABS mechanical processing, 13.93 MPa, 40383 cycle (d) ABS, laser processing, 12.90 MPa, 19525 cycle
반면, ABS의 CO2 레이저 가공 시편의 경우 표면부의 열융착 부분에서 응력의 집중으로 여러 방향에서 초기 균열이 발생한 것을 확인할 수 있다. 이러한 초기 균열이 크게 발생함으로 인해 피로 파괴와 소성파괴가 같이 발생한 것으로 보인다. 이로 인하여 ABS의 기계 가공 시편 대비 피로 특성이 현저하게 낮게 측정된 것을 확인할 수 있다.
3.2 시편 제조 방식 비교
실험 계획법 등을 통해 실험의 방식과, 시편의 필요 수량을 최적화 하여 진행하더라도 신뢰성 있는 실험 결과를 얻기 위해서는 실험 시 발생하는 문제를 고려하여 다수의 실험 시편이 요구된다.
만약 효율적이지 못한 공정의 선택으로 실험 시편이 제작되거나 최종 완성 시편의 품질이 실험에서 요구되는 수준에 만족하지 못한다면 재 작업으로 인해 소요되는 시간적 손실 및 초과 비용의 발생 실험 결과의 신뢰성 하락 등의 문제점을 갖게 된다.
엔지니어링 플라스틱의 평판형 초음파 피로시험 시편의 제작과 관련하여 POM, ABS 두 가지 소재에 대해서 1) 형상의 제작방법, 2) 공차 관리 적합 수준, 3) 가공시간, 4) 제작 평균비용 수준 등으로 주요 내용을 분류하여 비교하였을 때 Table 3, 4와 같은 내용을 확인할 수 있었다. 내용의 비교에 있어서는 시험 시편의 특성상 동일한 내용의 양산적 생산 방식의 접근이 아닌 일반적인 실험에서 요구되는 다양한 인자를 반영할 수 있는 다품종 소량 생산 방식의 접근을 기준하였으며 범용성 있는 CNC 공작기계에서의 실제 생산 방식과 원가 산정 방식으로 비교하였다. 제작 평균비용의 수준은 수치적 비교가 아닌 POM 레이저 가공의 방식을 보통으로 기준하여 결과값을 상대적으로 비교하는 것으로 결과를 표시하였다.
4. 결 론
본 연구에서는 엔지니어링 플라스틱(POM, ABS)에 대해 초음파 피로시험을 적용하였으며, 가공 방법에 따른 피로 특성 비교를 위해 머시닝센터를 활용한 절삭가공과 CO2 레이저 가공을 사용하였다.
초음파 피로시험 시편 설계를 위한 동탄성계수는 POM 2.02 GPa, ABS 1.645 GPa로 측정되었으며 실험환경에 맞는 시편을 설계하였다. 제작 시간 비교 결과 시편의 노치부 가공 시 절삭가공이 레이저 가공보다 20배 이상의 시간이 소요됨을 확인하였다. 또한, 가공 면의 분석결과 POM 소재는 두 가공 방법에 대해 준수한 표면 마감을 달성하였으나, ABS 소재는 절삭 가공시 양호한 표면 품질을 확보할 수 있었으나 가공시에는 열융착으로 인한 탄화 형상이 관측되었다. 이러한 특징은 피로시험에서 응력 집중을 발생시켜 피로 강도가 낮아지는 현상을 야기하였다.
본 연구를 통해 엔지니어링 플라스틱에 대해 가공 방식에 피로 특성의 분석과 더불어 제조관점에서의 시간과 비용 특성을 확인하였다. POM의 경우 CO2 레이저 가공으로 가공시간 대비 우수한 가공면의 표면 거칠기를 얻을 수 있으며 절삭가공과 유사한 피로 특성 또한 얻을 수 있음을 확인하였다. 이는 POM 소재와 관련한 각종 정밀 부품의 가공에 있어서 CO2 레이저 가공을 부품의 특성에 맞게 적절하게 활용할 경우 제작 시간 단축 및 비용적 측면에서 이점을 가져갈 수 있다고 판단된다. ABS의 경우 열융착으로 인한 탄화면의 영향으로 피로수명에 미치는 부정적 영향이 크므로 가공면의 표면 마감과 준수한 피로 특성을 기대할 수 있는 절삭가공 공정의 선택이 적합할 것으로 판단된다.
Acknowledgments
이 연구는 산업통상자원부(MOTIE)와 한국에너지기술평가원(KETEP)의 지원을 받아 수행한 연구 과제입니다. (no.20206410100080)
References
-
Chauhan, V., Ka¨rki, T., Varis, J., 2019, Review of Natural Fiber-reinforced Engineering Plastic Composites, Their Applications in the Transportation Sector and Processing Techniques, J. Thermoplast. Compos. Mater., 35:8 1169-1209.
[https://doi.org/10.1177/0892705719889095]
-
Kurt, M., Kaynak, Y., Bagci, E., Demirer, H., Kurt, M., 2009, Dimensional Analyses and Surface Quality of the Laser Cutting Process for Engineering Plastics, Int. J. Adv. Manuf. Technol., 41 259-267.
[https://doi.org/10.1007/s00170-008-1468-7]
-
Kim, T. Y., Kim, H. S., Shin, H. G., 2014, Investigation into the Drilling Characteristics of Carbon Fiber Reinforced Plastic (CFRP) with Variation of the Stacking Sequence Angle, J. Korean Soc. Manuf. Technol. Eng., 23:3 250-258.
[https://doi.org/10.7735/ksmte.2014.23.3.250]
-
Tarantili, P.A., Mitsakaki, A. N., Petoussi, M. A., 2010, Processing and Properties of Engineering Plastics Recycled from Waste Electrical and Electronic Equipment (WEEE), Polym. Degrad. Stabil., 95:3 405-410.
[https://doi.org/10.1016/j.polymdegradstab.2009.11.029]
-
Yeom., H. H., Jung, Y. C., Kim, C. Y., Kang, K.Y., Lee, M. G., Hong, M. S., Jeon, Y. H., 2015, Ultrasonic Fatigue Test for a High Strength Steel Plate, J. Korean Soc. Manuf. Technol. Eng., 24:6 589-593.
[https://doi.org/10.7735/ksmte.2015.24.6.589]
- ASTM, 2021, Standard Test Method for Dynamic Young’s Modulus, Shear Modulus, and Poisson’s Ratio by Sonic Resonance, ASTM E1875-20a, ASTM International, West Conshohocken, PA.
-
Bathias, C., Paris, P., 2005, Gigacycle Fatigue in Mechanical Practice, Marcel Dekker, New York.
[https://doi.org/10.1201/9780203020609]
Ph.D. candidate in the Department of Mechanical Engineering, Ajou University.
His research interest are high-precision machining and welding performance and efficiency.
E-mail: sky12080@ajou.ac.kr
M.Sc. in the Department of Mechanical Engineering, Ajou University.
His research interest is Composite 3D printing and fatigue life.
E-mail: dudwo5012@ajou.ac.kr
Postdoctoral researcher in Department of Mechanical Engineering, Ajou University.
His research interest is Metal 3D printing with FEM analysis.
E-mail: did9594@ajou.ac.kr
Staff Engineer in Samsung Electronics Co., Ltd.
His research interest is high cycle fatigue.
E-mail: hyunho.yeom@samsung.com
Principal Engineer in Samsung Electronics Co., Ltd.
His research interest is Structural and Fatigue Analysis.
E-mail: cm0107.park@samsung.com
Professor in the Department of Mechanical Engineering, Ajou University.
His research interest are developing novel manufacturing processes using heat and vibration and their effects of processes on the material characteristics.
E-mail: princaps@ajou.ac.kr