
고밀도 전자빔 조사 기반 대량의 미세홀 가공 실험 및 노이즈를 배제한 Micro CT 미세홀 형상 분석 연구
Abstract
Focused electron beam drilling is an advanced manufacturing process for rapid and mass penetration of the microholes on a metallic substrate. A focused electron beam can generate tapered microholes on the metallic substrate based on an ablation process with high thermal energy absorptance. To improve the geometrical qualities of microhole by optimizing the process parameters related to the electron beam, analyzing many cases of the intact microholes is important. However, analyzing for the geometrical shapes of microholes without any damage or deformation of the drilled substrate is time-consuming and requires a certain level of proficiency. In this study, micro computed tomography (micro CT) analysis of microholes on stainless steel substrates that were drilled with a focused electron beam depending on the beam currents was conducted. Moreover, using the overlapping method of masking layers, X-ray diffraction noises in the cross-sectional images of the drilled substrates were excluded during the microhole analysis.
Keywords:
Focused electron beam, Microhole drilling, Micro CT, Image processing, Nondestructive analysis1. 서 론
1.1 연구배경
최근 정밀 부품의 가공 및 제조 공정 분야에서는 자동차, 선박, 항공과 같은 대형-초대형 제품 산업뿐만 아닌 반도체와 같은 초소형 가공 산업에서도 그 수요가 증가함에 따라 초고속-초정밀 공정이 가능한 기술 개발에 이목이 집중되고 있다.[1,2] 특히 오늘날에는 스마트폰, 웨어러블 디바이스, 임플란트와 같은 초미세공정을 필수적으로 거쳐야하는 제품들이 우리 일상에 밀접하게 자리잡아가고 있어 초고속-초정밀 공정에 대한 수요가 지속적으로 늘어나는 추세이다. 이러한 배경속에서 고밀도 전자빔을 활용한 미세홀 연속 가공 공정은 초고속-초정밀 가공이 가능하다는 점에서 차세대 기술로 손꼽히고 있다. 100-150 keV 수준의 높은 가속 전압 환경에서 전자기적 렌즈를 통해 마이크로사이즈로 집속하여 타겟 소재에 조사하는 고밀도 전자빔 조사 기술은 가속된 전자의 고유 거동을 바탕으로 높은 침투율과 에너지 흡수율을 끌어낼 수 있어 일반적인 산업용 철강 소재뿐만 아닌 티타늄 합금과 복합소재와 같은 특수 소재에 대해서도 뛰어난 가공 수행 능력을 보장한다.[3-5] 또한 초당 100,000 홀 이상의 높은 가공 속도를 지니고 있어 앞서 언급한 초고속 제품 생산에 적합하다는 평가를 받고 있으며[2], 진공 분위기 내의 건식 공정으로 진행되어 조사 부위 이외에는 소재 오염이 거의 발생하지 않는다는 점이 타 공정기술과의 차별성을 만들어낸다.[6]
본 연구에서는 스테인리스강 시편 상에 고밀도 전자빔의 조사 전류별 대량의 미세홀 공정을 수행하였다. 전자빔 조사 기술 상의 주요 공정 조건인 조사 전류를 조절함에 따라 100-200 μm 수준의 관통된 미세홀들을 성공적으로 획득하였다. 금속 시편 상의 미세홀 공정 이후, 대량의 미세홀에 대한 기하학적 형상 측정 및 분석 간에는 높은 분석 난이도와 숙련도, 그리고 시간이 요구된다는 점을 주목하였다. 구체적으로 미세홀 분석 과정은 금속 시편을 절단하여 절단면을 획득한 후 폴리싱 등의 후처리를 거쳐 홀 단면을 획득하는 것이 일반적이다. 그러나 이러한 직접적 절단 방식의 경우 금속의 소성 변형 및 파괴를 유도할 수 있는 가공 장비를 활용하게 되는데, 이때 가공 툴에 의한 미세홀 붕괴가 발생할 수 있으며 측정자가 원하는 위치의 미세홀 단면을 선택적으로 획득하기에는 높은 난이도가 뒤따른다. 이러한 직접적인 시편 절단 방식의 단점과 비효율성을 해결하고자 마이크로 컴퓨터 단층촬영 장비(micro computed tomography, micro CT)를 활용한 시편 내부 촬영 방식을 채택하였다. 물론 기존에도 금속 소재를 대상으로 micro CT는 비파괴 검사 및 기공 검사에 주로 이용되어 왔으나,[7-9] 전자빔으로부터 관통된 미세홀의 형상 정보를 획득하기 위해 사용된 연구는 소수에 불과했다.[4] 또한 micro CT가 발생시키는 X선이 금속에 투과될 때의 이미지 노이즈는 필연적으로 발생하기 마련이나, 대량의 미세홀에 의한 다량의 이미지 노이즈를 다룬 사례는 극히 드물다고 할 수 있다. 본 연구는 금속 시편 내의 대량의 미세홀들을 micro CT로 분석하였을 때에 나타나는 다량의 이미지 노이즈를 관찰하였으며, 이를 배제하여 대량의 미세홀에 대한 형상적인 정보를 온전히 획득하는데에 성공하였다. 그 이후 조사 전류 별 미세홀 형상 특성에 대한 실험적인 분석을 성공적으로 수행하였다.
2. 고밀도 전자빔 기반의 미세홀 드릴링
2.1 고밀도 전자빔 조사를 통한 미세홀의 형성 원리
본 연구에서는 고출력의 전자빔 소스와 마이크로 스케일의 집속 영역을 바탕으로 고밀도 전자빔을 형성하여 이를 미세홀 드릴링 가공에 활용하였다. Fig. 1은 전자빔을 고밀도의 에너지원으로써 형성하고, 금속 소재 표면에 조사하기 위한 공정 장비의 내부 구성 요소와 조사 원리를 나타내고 있다. 음극 필라멘트(cathode filament)가 위치한 최상단부부터 조사된 전자빔과 금속 소재가 맞닥뜨리는 최하단부까지 살펴볼 때, 크게 빔 가속부, 빔 집속부, 그리고 진공 챔버로 이루어져 있다. 먼저 빔 가속부(beam acceleration)는 전류를 받아 고온이 된 음극 필라멘트에서 자유전자들을 방출하게 될 때, 이 자유전자들을 100-150 keV 수준의 높은 가속 전압에 노출시켜 음극-양극 방향으로 가속시키는 역할을 한다. 빔 집속부(beam focusing)는 빔 가속부에서 가속된 전자들이 두개의 솔레노이드 코일(solenoid coil)이 만들어내는 자기장을 통과시켜 가속된 전자들의 경로를 정렬하고 집속시킨다.[3,4,10] 이 때 가속된 전자가 지나는 경로 상에 위치한 스티그메이터(stigmator)는 집속되는 전자들의 경로가 의도하지 않은 방향으로 왜곡되어 나타나는 비점수차현상(astigmation)을 방지하는 역할을 한다.[11] 빔 가속부와 빔 집속부를 거쳐가며 형성된 고밀도의 전자빔은 진공 챔버(vacuum chamber) 내에서 소재 최상단 표면부터 탄성 혹은 비탄성 형태의 연쇄 충돌하게 된다. 이러한 연쇄 충돌은 가속된 전자들의 운동에너지를 열에너지로 변환시키게 되며 고체 상태의 소재는 표면으로부터 깊이 방향으로 증발 또는 용융 현상을 연쇄적으로 겪게 된다. 이러한 원리를 통해 마이크로 사이즈로 관통된 미세홀이 형성된다.[4]
2.2 금속 시편 셋업과 가공 조건 선정
고밀도 전자빔 조사를 통해 관통된 미세홀을 확보하기 위하여 Fig. 2(a)처럼 50 mm×50 mm×0.3 T 규격의 STS304 스테인리스강(stainless steel) 금속 시편을 제작하였다. 고밀도 전자빔이 금속 시편의 표면부터 바닥면까지 관통하게 될 때, 스테인리스강 시편 상의 조사지점은 소재 용융점 온도인 약 1,400℃ 기화점 온도인 3,000℃ 이상으로 온도가 올라가며 기화-용융의 상변화를 반복하게 된다. 이 때 발생하는 용융물들은 전자빔이 조사되는 동안 소재 기화압과 용융물 간의 표면 장력, 그리고 중력 등으로 인해 유동현상을 겪다가 전자빔 조사가 종료되면 열원이 사라져 재응고(resolidification)의 과정이 일어나게 된다.
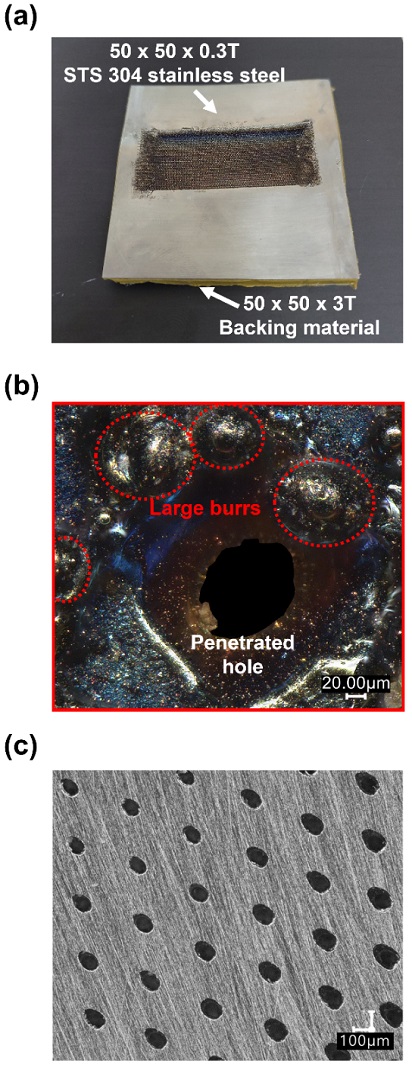
(a) STS 304 stainless steel substrate attaching the backing material, (b) large burrs around the microhole aftter electron beam irradiations, and (c) microholes after the mechanical polishing with 120-600 grits SiC paper
재응고가 일어나는 동안 완전히 응고되지 않은 용융물들은 중력이 지배적으로 작용함으로써 소재재 바닥부 방향으로 흘러내려가게 되고 관통된 영역을 막아버리는 결과를 초래하게 된다.[4,12] 이를 방지하기 위하여 소재 바닥부에 후면 소재(backing material)를 부착하였다. 후면 소재는 금속 시편에 비해 상대적으로 낮은 기화점 온도를 가지고 있어 금속 시편을 관통한 전자빔과 후면소재가 만날 때 조사 방향의 역방향으로 폭발적인 상승압을 유도하는 역할을 한다. 이는 금속 시편의 용융물이 전자빔 관통 영역을 틀어막은 채 재응고되는 현상을 방지하여 완전한 홀 관통을 유도하는 역할을 하게 된다. Fig. 2(b)에서는 후면 소재의 상승압으로 인해 용융물들이 밖으로 분출되어 burr가 형성된 모습을 나타낸다. 후면 소재는 구리와 황동의 혼합물로 구성되어 있으며, 50 mm×50 mm ×3 T의 규격으로 제작하여 Fig. 2(a)와 같이 금속 시편 바닥부에 부착하였다.[12] 본 연구에서는 조사 전류에 따른 미세홀의 형상 분석을 실시하기 위하여 Table 1과 같은 전자빔의 조사 조건으로 실험을 진행하였다. 조사 전류는 전자빔의 출력을 결정할 뿐만 아니라 집속 영역의 사이즈에도 영향을 끼치는 독립적인 인자로 알려져 있으며, 이는 전자빔의 에너지 밀도를 결정하는 가장 근본적인 공정 인자라고 판단하였다.
3. Micro CT를 활용한 미세홀 분석
3.1 Micro CT 촬영을 통한 3D 미세홀 형상 측정
마이크로 컴퓨터 단층 촬영 장치(micro CT)는 X선의 투과성과 회절성을 활용하여 동물 및 인체 내부에 존재하는 무기물의 형상을 영상화하는 기법으로써 의생명 분야 뿐만 아닌 난삭재 혹은 내부 관찰이 힘든 구조의 금속 내부의 비파괴 검사와 금속 용접부 또는 적층물의 기공 검사에도 지속적으로 활용되어오고 있다.[7-9] 본 연구에서는 비절단 방식의 micro CT 촬영을 통해 미세홀 시편의 훼손과 소모 없이 촬영하는 방식을 제안하고 수행하였다. 미세홀 시편 촬영에는 Bruker 사의 SkyScan1176 micro CT 장비를 활용하였다. 해당 장비는 쥐와 토끼 등의 소동물 생체를 분석하는 장비로 활용되고 있으며, 마이크로스케일의 분해능을 갖추고 있어 실험에 사용된 시편을 측정하는데에 적합하다고 판단하였다. Table 2에서는 CT 촬영의 촬영 조건을 나타낸다. Fig. 2의 (c)는 micro CT를 통해 촬영한 top view를, Fig. 3은 금속 시편의 3D 형상 이미지를 나타내고 있다. 조사 전류별로 실험된 금속 시편의 영상물은 top view에서 보았을 때 불필요한 공백 영역을 최소화한 후 약 2,000개의 단면 이미지로 구성이 되어있으며 각 단면 이미지의 해상도는 3964×480 비트맵 이미지로 저장되어 있다.
3.2 Micro CT 촬영물의 노이즈 제거
Micro CT에 사용되는 X선은 자외선보다 파장이 짧고 투과성이 뛰어나기 때문에 일반적인 생체부위나 비금속에 대해서는 뛰어난 분해능을 갖는다. 그러나 시험에 사용된 STS304 스테인리스강과 같은 고체 상태의 금속 시편은 구성 원자의 배열이 비금속에 비해 규칙성을 띠고 있어, X선이 금속 시편을 만나게 될 때 X선의 반사와 산란에 의한 회절현상이 발생한다.[13] Fig. 4(a)에서는 금속 시편 단면의 CT촬영본을 나타내며 회절현상이 X선이 시편 표면상에 진입할 때 한번, X선이 시편을 투과하고 이탈할 때 한번 총 2회 발생하고 있음을 알 수 있다. 이러한 회절 현상은 관심 영역(area of interest, AOI)을 마치 거울로 비춘 듯한 사영(射影) 형태의 노이즈를 발생시킨다. 노이즈를 배제하고 AOI를 명확히 나타내기 위하여 소재의 두께 정보와 픽셀 정보를 바탕으로 절단면 별로 마스킹 레이어를 제작하고, 이를 절단면 원본에 오버랩하여 Fig. 4(c)와 같은 관통된 미세홀을 포함한 금속 시편의 형상을 성공적으로 확보하였다.
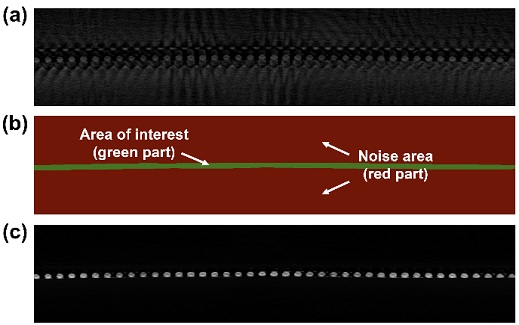
(a) The original cross-sectional image of the microholerilled substrate, (b) masking layer including AOI and noise area, and (c) processed cross-sectional image overlapped with an original image and a masking layer
마스킹 레이어를 제작하는 과정은, 먼저 미세홀을 포함한 시편의 단면 이미지를 불러온 뒤 시편의 두께를 픽셀 값으로 환산한 수치적 정보와 실제 시편의 프로파일을 바탕으로 도출한 형상적 정보를 바탕으로 실제 시편의 영역을 추적하고 이 영역을 AOI로 구분하였다. 실제 시편의 프로파일의 예시는 Fig. 5에서 확인할 수 있다. 그 다음, 실제 시편 영역 외의 나머지 영역들을 노이즈 영역이라고 판단한 뒤 Fig. 4(b)와 같이 AOI와 노이즈 영역을 종합하여 마스킹 레이어로 제작하였다. 최종적으로는 원본 단면 이미지와 마스킹 레이어를 오버랩하여 노이즈를 제거하는 방식을 진행하였다. 관심영역 설정-마스킹 레이어 제작-오버랩을 통한 노이즈 제거의 프로세스를 조사 전류별 시편 상의 약 2,000개의 단면 이미지에 개별적으로 적용하였으며 이를 수행 가능한 자체 제작 MATLAB 스크립트를 활용하였다. Fig. 4(c)에서는 마스킹 레이어를 적용한 노이즈가 제거된 시편의 이미지로써, 백회색에 가까운 영역은 가공되지 않은 금속 스테인리스강 영역이며, 검은색으로 나타난 영역은 비어있는 공간을 의미한다.
4. 실험 및 측정 결과
4.1 미세홀 형상의 특성 분석
미세홀 형상의 분석 과정에서, 고밀도 전자빔의 조사가 연속적으로 이루어진 금속 시편은 앞서 언급한 후면 소재의 폭발적인 상승압 효과를 받아 완전 관통이 일어났음을 확인할 수 있었다. Fig. 6의 (a)는 micro CT를 기반으로 촬영한 조사 전류별 홀 형상을 나타내고 있다. 홀 형상이 조사 전류가 증가함에 따라, 시편 최상단의 입구부 직경과 시편 바닥면의 출구부 직경이 모두 증가하고 있음을 알 수 있다.[2,4] 조사 전류 조건이 높아짐에 따라 더욱 뚜렷한 tapered hole의 형태가 나타남을 확인할 수 있는데, 이는 운동에너지-열에너지 전환에 의한 융삭 가공 방식의 공정의 대표적인 특성이라고 할 수 있다.[14] Fig. 6(b)의 경우 micro CT 촬영 분석 이후 각 금속 시편을 직접적으로 절단하여 획득한 실제 홀 형상의 이미지이다. 금속 시편 절단에는 시편과 그 내부의 미세홀의 손상을 최소화하기 위하여 와이어 방전 가공(wire electrical discharge machining) 방식을 활용하였으며 미세홀 단면부를 180-240 grits SiC 폴리싱 페이퍼로 연마한 후에 광학 현미경(optic microscope, OM)으로 촬영하였다. Fig. 6에서는 (b)와 같이 OM으로 촬영된 이미지를 micro CT의 촬영 결과물인 (a)와 비교해보았을 때, 조사 전류 조건에 따라 나타내는 홀 형상의 경향을 동일하게 나타내고 있다. 미세홀의 정성적인 형상을 확인하는 데에 실제 홀 형상과 비교하였을 때 micro CT를 충분히 활용할 수 있음을 알 수 있다.
4.2 Micro CT의 측정 정확도 검증
Micro CT 촬영본과 OM 촬영본의 비교를 통해 금속 시편 미세홀의 정성적인 형상과 그 경향이 차이가 없음을 확인하였다. 그러나 본 실험에 대한 micro CT 분석은 대량의 미세홀 가공을 진행한 금속 시편을 대상으로 하고 있기 때문에, 다량의 X선 회절현상에 의한 노이즈가 높은 수준으로 발생하게 된다.[13] 그렇기 때문에 micro CT 분석이 과연 정량적인 치수 측정 부문에서도 높은 정확도를 가질지 확인해보고자 치수 정확도 검증을 실시하였다. Fig. 7의 그래프는 조사 전류에 따른 분석 방법별 입구부 및 출구부 직경의 비교이며 검은색 막대는 OM을 통해 촬영하고 측정한 실제 시편의 미세홀 직경 측정값, 붉은색 선은 micro CT 촬영으로 획득한 미세홀 직경의 측정값을 나타낸다.
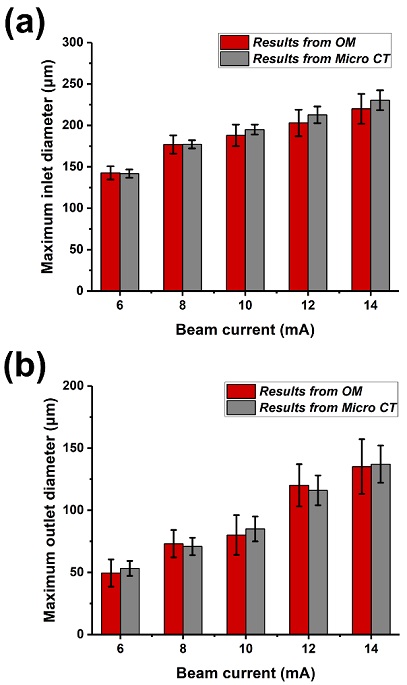
Accuracy validations of hole qualities between micro CT and OM for the (a) inlet and (b) outlet diameter of microholes
이 때의 직경값들은 미세홀 입구부 혹은 출구부의 최대 직경 길이로 정의하고 측정하였다. Fig. 2(c)와 Fig. 8과 같이, 미세홀의 입-출구부는 정원(正圓) 형태가 아닌 타원(楕圓) 형태인 경우가 다수 확인되고 있었기에 조사 전류별로 입구부 및 출구부에서 형성될 수 있는 장축의 길이를 대표값으로 설정하였다. 치수 실제 측정값과 micro CT 측정값 모두 30개 홀에 대한 평균치와 표준오차를 나타낸다. 실제 홀 직경 치수 대비 micro CT 촬영본의 치수는 약 0.16%의 최소 오차율, 6.11%의 최대 오차율을 가지고 있다. 이 때 오차율은 OM을 통한 측정값을 참값으로 하여 micro CT 측정 값에 대해 계산한 상대오차를 의미한다. 이러한 오차율이 발생하는 이유는 micro CT이 촬영 조건에 의해 1 픽셀당 약 13 μm의 환산값이 결정되어 스케일 상에서 발생하기 때문인 것으로 사료된다. 본 실험 및 연구에서는 조사 조건별로 단일 금속 시편 상에 약 3,000개의 연속적인 미세홀 가공을 진행하였다. 전자빔 조사는 열에너지 기반의 용융을 유도하기 때문에 고밀도 전자빔 조사 시 금속 시편 수평방향으로의 열에너지 전달이 필연적으로 발생하게 된다. 이 때 직전 번의 조사가 직후의 조사에 열 영향을 미치기 때문에 단일 금속 시편 내에서 미세홀 가공이 반복될수록 금속 시편의 내부 온도가 증가하게 되며 조사 전류가 높을수록 직전 가공에 의한 시편 상의 열 영향이 심화된다. 조사 전류가 증가함에 따라 타원형의 직경을 가지면서도 tapered hole의 형태로써 관통되는 미세홀의 출현 빈도가 증가하게 되어, OM으로 분석된 실제 측정값들은 error bar의 길이가 길어지는 것으로 확인할 수 있다. 금속 시편 상에 관통된 대량의 미세홀들은 micro CT 촬영 시 비록 금속 시편의 물리적, 구조적 특성에 따라 대량의 노이즈를 회피하는 것은 불가피하나, micro CT 촬영 이후 노이즈 문제를 보완함으로써 홀 형상의 정성적인 분석뿐만 아니라 정량적인 분석 또한 micro CT를 통해 진행하는 것은 적절하다고 판단하였다.
5. 결 론
본 연구에서는 120 keV의 가속 전압 조건과 6-14 mA 범위의 조사 전류를 바탕으로 고밀도 전자빔 조사를 실시하여 스테인리스강 소재 상에 대량의 미세홀 가공을 실시하였다. 대량의 미세홀의 분석을 진행함에 있어 직접적이고 물리적인 가공 방식을 통해 미세홀의 절단면을 획득할 경우 미세홀이 소실 혹은 붕괴되는 문제점이 발생하였다. 이를 해결하고자 비절단식이면서도 간접적인 분석 방법인 micro CT 촬영 분석법을 제안하고 실시하였다. 대량의 미세홀을 포함하는 얇은 시편에서는 micro CT 분석 시 X선의 회절 현상이 심화되어 사영 형태의 노이즈들이 시편 표면에 다량으로 나타나는 문제가 발생하였으며, 자체 제작한 MATLAB 스크립트 기반의 마스킹 레이어 오버랩 방식으로 노이즈를 성공적으로 배제하였다. Micro CT 촬영 분석 이후, 촬영에 사용된 금속 시편을 직접 절단을 추가적으로 실시하여 미세홀 형상의 정성적-정량적 정확도를 검증하였으며 최소 오차율 0.16%, 최대 오차율 6.11%을 나타내었다. Micro CT를 이용한 비절단식 간접적 분석 방법은 실험된 시편을 훼손-소모하지 않는다는 장점이 있어 고밀도 전자빔 조사를 통해 생산된 제품의 품질 검사 혹은 후속 연구를 진행할 때에 있어 경제성과 효율성을 증대시킬 수 있음이 자명하다. Micro CT 촬영 분석 단계에서 노이즈 자체를 최적화하고 해상도를 증가시키는 분석적 연구가 추가적으로 진행된다면 별도의 이미지 프로세싱 및 후처리 없이도 더욱 선명하게 대량의 미세홀을 포함한 금속의 3D 형상물을 확보할 수 있을 것으로 기대된다.
Acknowledgments
이 연구는 한국연구재단의 기초연구사업 지원(과제번호: 2021R1I1A1A01051407, 2022R1A2C3007963)으로 수행되었습니다.
References
-
Joe, H. E., Kang, E. G., Jun, B. G., 2018, A Review of State of the Art of Electron Beam and Ion Beam Machining, J. Korean Soc. Precis. Eng., 35:3 241-252.
[https://doi.org/10.7736/KSPE.2018.35.3.241]
-
Kang, J. G., Min, B. K., Kang, E. G., 2021, Melting Depth Characteristics according to Electron Beam Dose for Electron Beam Micro-Hole Drilling, J. Korean Soc. Precis. Eng., 38:3 169-176.
[https://doi.org/10.7736/JKSPE.020.104]
-
Kim, J., Lee, W. J., Park, H. W., 2008, Temperature Predictive Model of the Large Pulsed Electron Beam (LPEB) Irradiation on Engineering Alloys, Appl. Therm. Eng., 128 151-158.
[https://doi.org/10.1016/j.applthermaleng.2017.08.142]
-
Park, H. M., Kang, J. G., Kim, J. S., Kang, E. G., Choi, S. K., Kim, J., Park, H. W., 2022, On the Paradox of the Destabilizing Effect of Damping in Non-Conservative Systems, Int. J. Therm. Sci., 177 107584.
[https://doi.org/10.1016/0020-7462(92)90065-F]
-
Kim, J., Lee, W. J., Park, H. W., 2016, The State of the Art in the Electron Beam Manufacturing Processes, Int. J. Precis. Eng. Manuf., 17:11 1575-1585.
[https://doi.org/10.1007/s12541-016-0184-8]
-
Kim, J., Kim, J. S., Kang, E. G., Lee, S. W., Park, H. W., 2013, Finite Element Analysis of Large-Electron-Beam Polishing-Induced Temperature Distribution, J. Korean Soc. Manuf. Technol. Eng., 22:6 931-936.
[https://doi.org/10.7735/ksmte.2013.22.6.931]
-
Macek, W., Martins, R. F., Branco, R., Marciniak, Z., Szala, M., Wroński, S., 2022, Fatigue fracture Morphology of AISI H13 Steel Obtained by Additive Manufacturing, Int. J. Fract., 235 79-98.
[https://doi.org/10.1007/s10704-022-00615-5]
-
Kim, C. Y., Kim, J. S., Lee, H., Park, M. K., Kim, S. W., Shin, S. S., Hwang, J. H., Kim, H. D., 2022, Effect of Laser Power Feedback Control on Mechanical Properties of Stainless Steel Part Built by Direct Energy Deposition, Journal of Welding and Joining, 38:2 197-202.
[https://doi.org/10.5781/JWJ.2020.38.2.10]
-
Choi, B. J., Yang, J. Y., Lee, M. G., Jeon, Y. H., 2021, Defect Analysis of Metal 3D Printing Process, J. Korean Soc. Manuf. Technol. Eng., 30:1 92-98.
[https://doi.org/10.7735/ksmte.2021.30.1.92]
- Kim, C. S., Kim, D. H., Park, M. J., Jang, D. Y., Han, D. C., 2007, Electron Beam Behaviors by the Electrostatic Lens in Triode Field Emission Gun, Trans. Korean Soc. Machine Tool Eng., 16:6 163-167.
-
Sun, B., Yin, B., Wang, P., Xu, G., Liu, J., Han, L., 2020, Analysis on Defocusing and Astigmatism of Electron Beam Selective Melting Machines, J. Phys.: Conf. Ser., 1654:1 012045.
[https://doi.org/10.1088/1742-6596/1654/1/012045]
-
Kim, S. H., Jung, S. T., Kim, H. J., Baek, S. Y., Kim, J. S., Kang, E. G., 2020, A Study on the Preparation Method of Vaporized Amplification Sheets and Electron Beam Machining Characteristics, J. Manuf. Process., 50 234-240.
[https://doi.org/10.1016/j.jmapro.2019.12.046]
-
Bouxsein, M. L., Boyd, S. K., Christiansen, B. A., Guldberg, R. E., Jepsen, K. J., Müller, R., 2010, Guidelines for Assessment of Bone Microstructure in Rodents using Micro–computed Tomography, J. Bone Miner. Res., 25:7 1468-1486.
[https://doi.org/10.1002/jbmr.141]
-
Yilbas, B. S., Aleem, A., 2004, Laser Hole Drilling Quality and Efficiency Assessment, Proc. Inst. Mech. Eng. Part B-J. Eng. Manuf., 218:2 225-233.
[https://doi.org/10.1243/095440504322886541]
Ph.D. candidate in the Mechanical Engineering at Ulsan National Institute of Science and Technology Mechanical Engineering.
His research interest is Electron beam machining process.
E-mail: gsdmi1942@unist.ac.kr
Ph.D. candidate in the School of Mechanical Engineering at Yonsei University and researcher in Korea Institute of Industrial Technology.
His research interest is Electron beam machining process.
E-mail: kang1380@kitech.re.kr
Researcher in Korea Institute of Industrial Technology.
His research interest is Electron beam machining process.
E-mail: totoro22@kitech.re.kr
Principle researcher in Korea Institute of Industrial Technology.
His research interest is plasma and electron beam processing and equipment technology.
E-mail: egkang@kitech.re.kr
Professor of Mechanical Engineering at Ulsan National Institute of Science and Technology.
His research interests lie in the synthesis and fabrication of multi-functional composite and the advanced manufacturing system.
E-mail: hwpark@unist.ac.kr
Assistant Professor of Mechanical Convergence Engineering at Gyeongsang National University.
His research interests mainly include composite machining and advanced manufacturing processes.
E-mail: jseo7717@gnu.ac.kr