
유닛화 열전소자를 이용한 정수기 냉각장치의 AL 방열판 설계
Abstract
Delay in cooling and temperature control failure occurs owing to the thermal dissipation issues in a product during mass production. Hence, a comparative evaluation of cooling performance was conducted on four types of heat sinks: the initially applied foreign heat sink (No. 2), domestically produced heat sink that experienced cooling deficiencies during mass production (No. 1), and two newly designed heat sinks (No. 3 and 4). No. 3 and 4 were modified by adjusting the spacing and length of the fins through slight changes in fin height, thickness, and number, resulting in variation in weight compared to that of No. 2. This helped in identifying the issues in No. 1. The two newly designed heat sinks demonstrated excellent cooling performance and weight reduction of approximately 10% compared to that of No. 2. Ultimately, No. 4 was selected as the final production model.
Keywords:
Thermoelectric module(TEM), Heat absorbed, Heat dissipation, Water purifier, AL heat sink1. 서 론
산업 장치, 반도체 공정 장비에 사용되는 온도관리와 가전제품의 냉각을 위한 기존 방식으로 냉매(refrigerant) 가스를 사용하는 컴프레서 냉동기(compressor refrigerator)에 의한 열교환 방식이다. 냉동기의 냉매 사용은 지구 온난화의 주범으로 분류되어 친환경 대체냉매에 대한 연구가 진행되고 있다. 컴프레서 냉동기는 장치가 크고 복잡하며 진동 및 소음을 유발하고 온도제어의 편차가 큰 단점이 있다. 그래서 최근 들어 냉매 가스를 사용하지 않고, 정밀한 온도제어가 가능한 열전소자(TEM, thermoelectric module)를 이용한 전자 냉각 방식의 사용이 첨차 확대되고 있다. 이 방식은 다양한 분야의 산업 장치 또는 기기의 냉각을 위해서 그 활용도가 늘어나고 있다. 열전소자 냉각은 장치 구조가 단순하고, 소음 및 진동 발생이 최소화되었고, 냉매를 사용하지 않아 친환경이다. 단 기존 컴프레서 냉동기에 비해서 냉각성능이 50~60% 정도의 성능만을 발휘하는 단점을 가지고 있으나, 컴프레서의 온도제어는 ±1℃ 범위지만, 열전소자는 ±0.001℃의 정밀 제어가 가능한 특징을 가지고 있다. 최근 들어서 소형・고성능의 시스템 반도체 패키지(AP, AI 칩, 차량용 반도체 등)의 수요가 기하급수적으로 증가하고 있고, 생산 공정 장비 및 출하 과정의 제품 신뢰성이 요구됨으로서 메인 FAB 및 sub 장비와 장치의 냉각, 완제품 테스트 장치의 냉각 온도 및 유지를 위한 정밀온도 제어를 위해 TEM을 이용한 전자 냉각시스템이 활발하게 사용되고 있으며, 이에 대한 냉각시스템과 사용방식에 대한 연구가 활발하게 진행되고 있다[1,2].
최근 들어서는 대기업 가전제품에도 AI 하이브리드 냉각방식으로 컴프레서 단일 방식에 열전소자(peltier element)를 결합한 하이브리드 냉각방식을 채택하여 정밀 정온 제어를 통한 에너지 절감에 활용하고 있으며, 소형가전 제품에 사용이 점차 늘어나고 있다. 특히 소형가전인 정수기 분야에 활발하게 적용되고 있으며, 최근 많은 기업에서 국내 및 해외 진출을 위해서 현재 다양한 제품 개발이 활발하게 진행되고 있다[3-7]. 열전소자는 고체식 냉각방식으로 반영구적으로 사용할 수 있으며, 소형 열전소자 사용은 제품의 소형화 및 디자인을 자유롭게 변경할 수 있는 특징을 가지고 있어, 정수기의 소형화 설계를 통한 제품 차별화를 위해 활발하게 적용하고 있다.
열전소자를 사용 시 방열은 허용 공간 제약과 원가 등으로 인해 일반적으로 가장 단순한 알루미늄(AL) 방열판(heat sink)을 사용하고 있어 방열판 크기에 대한 제한이 가장 크다. 따라서 공간 제약에 의한 방열판 규격에 대해 논하고자 한다.
따라서, 본 연구에서 Z사의 열전소자는 Model No. 28***, 55×55×4.1h (mm) 35.4 V, 6.0 A 규격을 사용하는 B사의 해외수출 모델로서 소비자가 사용 중에 냉각 불량으로 인한 제품 리콜(recall)이 발생하였다. 따라서 사용자 요구에 적합한 제품의 방열 최적화를 통한 빠르고 균일한 냉각성능 유지하기 위한 연구이다. 제한된 공간 내에서 AL 방열판의 최적 방열성능을 발휘할 수 있도록 알루미늄 방열판 규격 설계를 진행하여 완제품에 적용하고자 본 연구를 진행하였다.
2. 열전소자 유닛 적용 정수기 냉수통
2.1 열전소자
열전소자는 Fig. 1과 같은 내부구조의 고체 냉각 방식으로 절연 세라믹 사이에 반복적으로 배치된 n, p 반도체 칩을 동판 전극으로 직렬 연결하고, 양끝단 전극에 전원 와이어를 연결하여 DC 전류를 인가하면 한쪽에서 열 흡수(heat absorbed)로 냉각되고, 반대쪽으로 방열(heat rejected)하는 구조이다. 열전소자는 금속내에 전류가 흐를 때 열류가 함께 흐르고, 양금속에서 열류가 서로 같지 않아 접촉면에서 열의 발생 또는 흡수하는 펠티어 효과(peltier effect)라는 현상이 일어난다. 열 발생과 흡수는 가역적이어서 한쪽 면에서 흡열하고 다른 쪽으로 열을 밀어내는 열펌프 역할로 냉각하는 방식으로 전류 극성을 바꾸면 열 펌핑 방향 및 전류량이 바뀌기 때문에 열량을 변화시킬 수 있는 특징을 갖는다. 또한 열전소자는 반영구적으로 사용 가능하다고 알려져 있다. 일반적으로 실리콘 또는 에폭시로 절연 세라믹 사이의 가장자리를 밀봉하거나, 밀봉하지 않은 상태로 사용하게 된다. 이때 오랜 시간 동안 냉각 및 가열의 반복적 구동으로 실링 소재의 시효경화로 인해서 절연 세라믹 판으로부터 박리가 일어나게 되고, 냉온에 의한 결로 혹은 주변에서 발생한 습기의 침투로 열전소자 내부 전극의 부식 발생과 절연 문제로 인하여 제품 불량으로 이어지게 된다. 이를 예방하고자 이전연구에서 열전소자 유닛화 방안을 진행하였고, 그 결과로 사용 내구성 및 냉각성능을 향상시킬 수 있었으며 결과를 기술했었다[7,8].
2.2 유닛화 열전소자 적용 냉수통
본 연구 대상인 소형 정수기 냉수통 Assy' 제품의 냉수통 크기는 85×80×138h (mm), 800 ml 용량으로 소재는 본체와 덮게 모두 SUS304 0.6 t로 제작되었다. 공급된 물의 냉각을 위해서 열전소자의 사용 내구성 향상과 성능을 극대화하기 위하여 유닛화 모듈을 사용해서 Fig. 2와 같이 B사 정수기의 냉수통에 적용하였다. 이때 빠른 냉각 및 성능향상을 위해서는 열전소자 한쪽 면에서 발생하는 많은 열량을 빠르게 방열시킬 필요가 있으나, 소형 정수기 제품 특성상 한정된 공간에서 방열판 최적화를 통한 방열을 달성하는 것은 상당한 노하우와 단열 등의 설계 기술이 요구된다.
열전소자의 적용 분야에 따른 방열 방법으로는 수냉 방식과 AL 방열판을 사용한 공랭식, 수냉과 공랭의 혼용하는 방식 등의 다양한 방열기구에 의한 방열이 구현되고 있으며, 또한 새로운 방열기구 및 융합 방식 등의 개발이 활발하게 이루어지고 있다. 수냉 방식의 경우 AL 냉각 자켓 또는 유로를 형성한 냉각 블럭을 사용하거나 다양한 형상의 열교환기가 사용되고 있으며, 공랭방식은 종래에 사용하는 단순한 구조의 AL 방열판, 히트파이프(heat pipe)와 방열 핀(heat radiator fin)이 결합 된 구조 또는 AL 방열판 블록 부분에 히트파이프를 심어 열확산을 빠르게 하는 구조로서 방열판에 방열 팬(fan)을 부착하여 방열판의 핀 쪽으로 공기를 불어 넣는 방식의 방열구조가 사용되고 있다.
본 연구에서는 수요자의 요구에 따라 생산 원가 절감에 의한 양산이 가능하도록 일반적으로 가장 많이 사용하는 형태의 단순한 구조의 AL 방열판을 사용한 공랭식 방열을 적용하여, 제품규격에서 요구되는 냉각성능을 발휘하도록 방열판을 설계하고 양산품에 적용하도록 하였다.
3. 냉수통 냉각 테스트 및 고찰
3.1 냉수 탱크 냉각 부품 구성
본 연구에 사용된 소형 정수기는 일본으로 수출되는 B사의 양산 모델로서 냉수통 Assy'는 유닛화 열전소자를 적용한 전자 냉각 방식으로 Fig. 2 우측과 같은 형태의 제품으로 협력기업의 독자 기술이 적용되어있다. 사용된 열전소자는 Fig. 3과 같은 특성의 모델로 전자 냉각으로 냉수를 생산하게 되는데 냉각 시 발생하는 열전소자의 발열에 대해서 AL 방열판과 팬을 사용하여 방열하는 공랭식이다. 냉수통 Assy' 제품에서 요구되는 냉수 온도 확보를 위한 냉각성능을 발휘하도록 AL 방열판을 설계하고, 이를 적용하는 과정에 있어서 냉수통의 냉각 테스트를 진행하였다.
유닛화에 사용된 열전소자는 55×55×4.1t (mm)의 정사각형으로 35.4 V, 6.0 A 사양으로 거의 동일 성능을 갖는 Z사 28***** 모델로 Fig. 3과 같다. 열전소자의 성능지표를 나타내는 Δt 및 Z값은 70.6℃, 2.68과 유사한 성능의 제품을 사용하였고, 정수기 완제품의 열전소자 구동 DC 전원과 같은 DC 22 V를 인가하여 테스트를 진행하였다.
열전소자의 방열을 위한 AL 방열판은 설계 후 압출 성형으로 시제작하여 Fig. 4와 같은 규격의 4종류(No. 1~No. 4)를 사용하였다. No. 2는 최초 적용된 수입 방열판이고, No. 1은 최초 적용 방열판의 생산지 관리 부실에 따른 국산화 제품으로 양산과정에서 불량으로 이어진 제품이며, No. 3, 4는 신규 설계에의 시제작 되었으며 모두 AL-6063 소재 방열판이다. 방열판은 형상설계는 베이스 두께, 핀의 수, 두께 및 간격, 방열판 깊이 및 길이로 6개의 변수를 고려해야 하지만, 핀 두께는 핀 효율 98% 이상을 만족시키고 1.0 mm 이내로 압출 가능한 치수이므로 최적화가 필요가 없으므로 나머지 5개의 변수를 고려하게 된다. 그러나 본 연구 대상인 완제품 정수기는 이미 정해진 제한된 내부공간 때문에 냉수통 Assy'의 외형 크기를 변경할 수 없으므로 방열판 외형 크기 또한 변경이 어렵다. 따라서 방열판 전체를 최적화하지 않고, Fig. 4와 같이 핀의 두께, 개수에 따른 간격 및 높이에 대해서 미세하게 설계를 변경하여 결과적으로 목적 함수를 중량 변화로 설정해서 방열판의 냉각효율을 실험적으로 확인하였다.
3.2 냉각 성능 테스트 및 고찰
열전소자 유닛을 적용한 정수기 냉수통 Assy'의 냉각성능을 확인하기 위하여 양산용 냉수통에 AL 방열판(No. 1~No. 4) 4종류로 No. 3은 155×140×31h (mm), 44핀이고, 나머지 3종은 150× 140×31.7~ 32h (mm), 47핀 규격이다. 이들 방열판은 동일한 4.5 mm 베이스 두께에 방열 핀의 수, 두께, 높이, 길이 및 간격 등 규격의 미소한 차이로 방열판의 중량이 Fig. 4 처럼 46~1210 g 차이를 보이며, 여기에 120×120×25h (mm) 팬을 각각 장착한 150×180×190h (mm) 냉수통 Assy' 완제품에 대해서 방열판 규격 차이에 따른 열전소자 유닛의 냉각성능을 테스트하였다. 테스트 장치 구성은 Fig. 5와 같이 설치한 후 주위온도 30℃에서 32℃ 물을 냉수 탱크에 공급하는 조건에서 120분 동안 냉각성능에 대해서 비교 테스트를 진행하였다.
유닛화 열전소자를 이용한 냉수통의 냉각성능 실험을 위해서 GWinstek 및 A-BF사의 SMPS(DC power supply)로 열전소자를 구동하고, Fig. 6과 같이 냉수통 후면 외벽 상·중·하 위치에 k-type 열전대(thermocouple, 온도센서) 설치 후, 성형된 단열재로 감싸서 에너지 손실과 결로 생성을 방지하였고, Yokogawa사의 멀티레코더(MV-1000)를 사용하여 온도변화를 측정하였다. 또한 동시에 물(냉수) 온도는 냉수통 하부 중앙에 ø5, 길이 25 mm의 SUS 파이프를 설치하고 파이프 내에 온도센서를 삽입하여 설치하였고, 방열판 핀의 한쪽 면에도 열전대를 부착하여 온도변화를 확인하였다.
이처럼 4종의 방열판을 설계 시제작하여 냉각 테스트를 수행한 된 것은 국산화된 No. 1 방열판을 적용하여 양산 중인 냉수통 Assy'에서 알 수 없는 원인으로 냉각성능이 하락하고, 냉각제어에 문제가 발생하여 제품 불량으로 이어지는 사고가 발생하였으며, 이는 방열 문제가 발생한 것으로 예상되었다. 그래서 그 원인 파악과 완제품 내부의 제한된 공간에 적용이 가능한 최적 규격의 방열판을 설계하여 빠른 냉각과 성능향상이 요구되었고, 신규 방열판의 설계 및 시제작 테스트 후 신속한 양산 적용이 필요하게 되어 본 연구를 진행하게 되었다.
Table 1은 냉수통에 열전소자 유닛화 모듈을 장착하고, Fig. 4의 시제작 된 4종 AL 방열판과 방열 팬을 부착 후, 열전소자에 DC 22 V로 120분 동안 구동에 따른 냉수(냉각 센서)의 온도변화, 냉수통 외부 상・중・하부의 온도변화 및 방열판의 온도변화를 경과 시간에 따른 온도 데이터를 표로 기술하였고, 이 결과를 Fig. 7, 8에 온도 센서 설치 위치와 방열판에 따른 온도변화 그래프로 비교하였다.

Temperature distribution of the cold water tank during cooling operation with four types of heat sinks applied
Fig. 7은 냉수 탱크 Assy'의 각 온도 체크 위치에서 장착한 방열판 종류에 따른 온도변화를 비교하여 나타내었다. Table 1의 각 방열판 데이터의 파란색 사각 표시 부분은 정수기에서 요구되는 냉수 온도인 7.0℃에 도달하는 전후 시간대이며, 냉각 센서(cold sensor)에 의한 냉수 온도변화 비교를 Fig. 7(a)가 나타내었고, 이때 방열판 No. 3(흑색)이 약 48분 58초 정도로 가장 빠르게 7.0℃에 도달하였고 방열판은 약 41.2℃, No. 4(녹색) 약 55' 38" 약 40.1℃, No. 1(적색) 약 57' 06" 약 43.8℃, No. 2(청색) 약 61' 18" 약 44.4℃ 순으로 냉수 요구온도에 도달하고 방열판 온도가 높은 것을 알 수 있었다. 또한 냉수통 상・중・하부의 온도변화는 냉수가 요구온도까지 내려가는 경향인 냉수 센서와 같이 No. 3, 4, 1 및 2번 방열판 순으로 빠르게 냉각되는 것을 알 수 있었다. 그리고 No. 1 방열판을 제외한 모든 방열판의 경우 70분 이후에도 온도가 내려가는 양상을 보이며 지속적인 냉각이 이루어짐을 알 수 있었고, 이는 방열판의 방열성능이 적절함을 의미한다. No. 3 방열판의 핀 수는 3개가 적지만 길이가 5 mm 길고, 방열핀 간격과 중량이 2번째로 넓고 무거워 가장 우수한 냉각성능을 보였다. 즉 시제작한 4종의 방열판에서 중량이 무겁고 동시에 핀 간격이 넓은 방열판이 우수한 냉각성능을 보임을 알 수 있었다. 또한 방열판의 온도변화인 Fig. 7(d)를 보면 방열판의 표면 온도가 약 75분까지는 No. 4, 3, 1, 2 순으로 높고 거의 일정한 온도를 보이다가 최종적으로는 No. 3, 4, 2, 1 순으로 높은 것을 알 수 있으며, 이는 냉각을 위한 흡열량이 커짐에 따른 발열량이 증가하여 방열판 온도가 높아지는 것을 의미한다. 또한 No. 3과 No. 1 방열판의 경우 지속해서 일정한 온도를 유지함을 볼 수 있는데, 이는 열전소자의 냉각성능이 일정하게 유지되어 방열이 일정함을 의미한다.
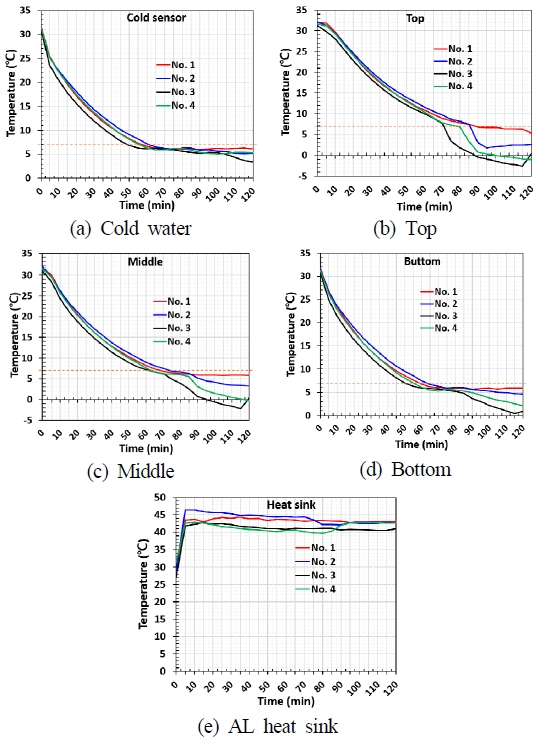
Comparison of temperature distribution at each position according to the installation of four types of heat sink
Fig. 8은 시제작 된 4종 AL 방열판을 적용한 냉수통 Assy' 상태의 냉각 테스트에서 각 온도측정 포인트인 냉수와 냉수통 외부 상·중·하부에서 5분 간격으로 측정한 온도변화 데이터인 Table 1의 No. 1~No. 4 방열판의 온도변화 그래프를 나타내었다. 초기 32℃로 공급된 원수(물)는 유닛화된 열전소자 모듈을 사용해서 냉각을 시작하여 5~6℃로 냉각되어 유지되는 120분 동안의 온도변화 과정을 나타내었다.
DC 22 V 전원이 인가되면 급격하게 온도가 내려가기 시작하여 냉수가 요구온도에 도달하게 된다. Table 1의 적색 사각 파선 데이터는 냉수통 외부 상・중・하부의 온도변화 데이터의그래프가 서로 교차하는 시간대 및 온도를 나타내었으며, 그래프에서 알 수 있듯이 온도변화를 보면 5.5~6℃ 사이에서 청색・흑색・녹색이 서로 교차하는 것을 알 수 있다.
이는 냉수통 냉각 테스트 과정에서 열전소자의 구동 전원에 대한 제어 포인트(control point)로 활용하게 되는데, 이 온도변화 데이터는 냉수통 Assy' 개발과정에 있어서 물의 냉각 테스트를 위한 열전소자 및 방열 팬의 구동을 제어하게 된다. 이 과정을 통과한 열전소자 유닛과 방열판 규격을 사용한 최종 테스트를 거쳐 냉수통 Assy' 개발을 완료한 후, 실질적인 제어는 정수기 완제품에 냉수통 Assy'를 장착한 상태에서는 냉수의 온도를 측정한 cold sensor 데이터를 토대로 냉수통의 구동을 제어하게 된다.
특히 Fig. 8(c)의 방열판 No. 3의 경우는 나머지 3개 방열판보다 약 0.2~0.3℃ 정도 낮은 온도에서 교차하였으며, 가장 빠르게 약 72분 42초에 교차하였고, (d) No. 4는 약 81분 35초, (a) No. 1은 약 117분 8초 그리고 (b) No. 2는 약 87분 5초 정도 순으로 냉수도 함께 교차함을 알 수 있었다. 여기서 No. 3의 경우 방열판의 핀 수가 3개 적고 핀 간격이 No. 1에 비해서 좁지만, No. 2, 4번에 비해서 넓고 방열판 길이가 5 mm 정도 길어서 성능향상에 영향을 미친것으로 보인다. 실제 냉수의 요구온도는 7℃이지만 냉수통 외부에서 측정된 온도는 6℃ 이전에서 교차하고 5℃ 이하로 점점 더 내려가지만, 냉수는 5℃ 전・후에서 유지되고 있는 것을 알 수 있다.
국산화를 통한 양산을 진행하던 No. 1 방열판인 Fig. 8(a) 그래프를 보면 냉각은 요구되는 성능이 나타나는 것처럼 보이지만 냉수통 외벽의 상・중・하부의 그래프가 교차하는 시간이 늦어지고, 더 이상 온도가 내려가지 않고 유지됨으로서 냉각제어가 실행되지 않고, 초기 냉수 생성이 늦음을 알 수 있었다. 그 원인을 보면 Fig. 4의 방열판 제원에서 알 수 있듯이 개발 초기 완제품에 적용된 No. 2 방열판과 비교할 때 핀 수는 같지만, 핀이 미세하게 얇아 간격이 넓어져서 전체 방열판의 중량이 16% 줄어서 121 g이 감소함으로써 이와 같은 현상이 발생한 것으로 판단되며, 열전소자 및 방열 팬 제어가 안되고, 냉각성능 지연 현상으로 이어져 제품 불량과 회수에 따른 경제적 손실로 이어지게 되었다. 방열판 No. 3의 경우 나머지 3종의 방열판에 비해서 방열판의 핀 수가 3개 적고 높이가 1 mm 낮지만, 상대적으로 핀 길이가 5 mm 길었다. No. 2에 비해 핀 간격이 넓고 방열판 중량이 6.1% 정도 줄었지만, 팬에 의한 강제 방열성능이 상승하여 가장 우수한 냉각성능을 보였다. 방열판 No. 4의 경우는 No. 2와 동일한 외형에서 방열판이 약간 얇아 핀의 간격이 넓어짐으로서 전체 중량이 9.3%인 70 g 정도 줄어들었으나, 0.05 mm 넓어진 핀 간격으로 팬에 의한 강제 방열성능이 상승하여 빠른 냉각성능이 구현되었다.
이처럼 B사와 초기 개발하여 판매 중인 제품에 적용된 No. 2 방열판에서 다양한 이유로 인해 No. 1 방열판으로 국산화하여 적용하던 중 원인불명으로 냉각성능 불량이 발생하게 되었었다. 따라서 그 원인을 분석하고 해결하는 과정에서 신규 방열판 No. 3과 No. 4를 추가하여 4종의 방열판에 대해서 방열과 냉각성능을 테스트하여 확인하였다.
그 결과 No. 2는 최초 성능을 유지하였고, 이를 기준으로 양산 중이던 No. 1 방열판은 중량이 과도하게 16%가 줄어들어 냉각성능 지연과 열전소자 및 팬의 구동 제어에 문제를 일으켰다. 신규 설계한 No. 3은 가장 우수한 냉각성능을 보였으나, 이미 양산 중인 정수기 내부에 냉수통 Assy'가 배치되는 공간이 제한되어 적용할 수 없었으며, No. 4 방열판의 경우는 방열판의 중량이 9.3% 줄어들었지만, 핀 간격이 0.05 mm 넓어져서 방열성능이 우수하여 초기 냉각성능이 5분 이상 빠르게 구현되었고, 신규양산품에 적용함이 적합할 것으로 판단되었다.
이처럼 국산화 과정의 냉각 불량의 원인 파악과 신규 방열판을 설계하고, 테스트한 결과 최초 방열판 대비 개발된 방열판의 중량 변화와 핀 간격이 방열성능에 가장 큰 영향을 미치는 것을 알 수 있었다.
4. 결 론
양산 중인 정수기의 냉수통 Assy'의 방열판 규격의 변화로 인한 냉각성능이 떨어져 제품 불량이 발생함으로서 기존에 적용하던 방열판과 유사한 규격의 신규 방열판을 제작하여 동일 규격의 냉수통에 적용하여 냉각성능 테스트를 진행하였다. 신규 방열판은 이미 정수기 완제품이 양산중에 있어 내부공간 변경이 불가능하였다. 따라서 제한된 공간에 적용하기 위해서는 외형 크기를 변경할 수 없는 제약조건에 따라 방열판의 핀 두께, 간격 및 길이만을 설계 변경에 반영하여 진행하였으며, 최초 개발 후 초기 양산 방열판(No. 2), 국산화 후 양산에 적용한 방열판(No. 1), 신규 설계 2종(No. 3, 4)으로 총 4종류의 방열판에 대한 비교 냉각성능을 평가하였다.
그 결과 최초 양산했던 방열판 기준으로 국산화 적용 No. 2 방열판의 불량원인으로 16%의 과도한 중량 감소에 따른 냉각성능이 지연되었던 원인을 파악하였고, 신규 설계 시제작한 방열판의 경우는 방열판의 중량을 10% 이내에서 줄였지만, 핀 수 또는 두께 변경을 통한 핀 간격을 약 3~10% 정도 키움으로서 우수한 방열성능을 확보하여 초기 냉각 시간을 줄이고, 우수한 냉각성능을 구현할 수 있었다. 이 결과를 기초로 양산 제품 성능 및 원가 절감 등을 고려하여 최종적으로 No. 4 방열판을 양산에 적용하였으며, 방열판 설계 기술을 확보하였다.
Acknowledgments
이 논문은 2023년도 전주대학교 연구년 지원에 따라 이루어졌음.
References
-
Son, D. S., Dong, S. H., Lee, W. Y., 2021, Development of Automatic Temperature Control Module for Semiconductor Test Process Using Thermoelectric Element, J. Korean Soc. Manuf. Technol. Eng., 30:1 31-36
[https://doi.org/10.7735/ksmte.2021.30.1.31]
-
Lee, K. J., Jeong, K. S., Park, S. M., 2010, Improvement of the Uniformity of Temperature Distribution inside Semiconductor Test Equipment Chamber, Journal of The Korea Academia-Industrial cooperation Society, 11:10 3626-3632
[https://doi.org/10.5762/KAIS.2010.11.10.3626]
- Chun, H. S., Moon, S. E., 2015, Application Trends in Thermoelectric Materials, Electronics and Telecommunications Trends, 30:1 144-153.
- Yoo, S. Y., Hong, C. P., Shim, W. S., 2004, A Study on the Performance of Thermoelectric Module and Thermoelectric Cooling System, Korean Journal of Air-Conditioning and Refrigeration Engineering, 16:1 62-69.
- Im, C. H., 2014, Experimental Study on the Cooling Performance of a Refrigeration System using Thermoelectric Module, Master Thesis, Korea University, Republic of Korea.
-
Cho, Y. T., 2020, Forced Heat Dissipation in 120 W Street LED Using Thermoelectric Modules, J. Korean Soc. Manuf. Technol. Eng., 29:4 281-287
[https://doi.org/10.7735/ksmte.2020.29.4.281]
- Cho, Y. T., Ma, S. D., 2018, Cooling performance enhancement of small water purifier using the thermoelectric module, Proc. Korean Soc. Manuf. Technol. Eng. Autumn Conf., 123.
-
Cho, Y. T., 2024, Unitized Design of Thermoelectric Element for Electronic Cooling of Cold Water Tank in Small Water Purifiers, J. Korean Soc. Manuf. Technol. Eng., 33:3 141-146
[https://doi.org/10.7735/ksmte.2024.33.3.141]
An Associate professor at the Dept. of Basic Science, College of Engineering, Jeonju University.
He is interested in Product and Mechanical Design, Nondestructive Testing and Evaluation using Infrared Thermography.
E-mail: choyt@jj.ac.kr
Assistant Professor, Department of Artificial Intelligence Convergence, Kunjang University College.
He is interested in Product and Machine Design using 3D Printing, and Secondary Battery Performance and Evaluation.
E-mail: choi7889@kunjang.ac.kr